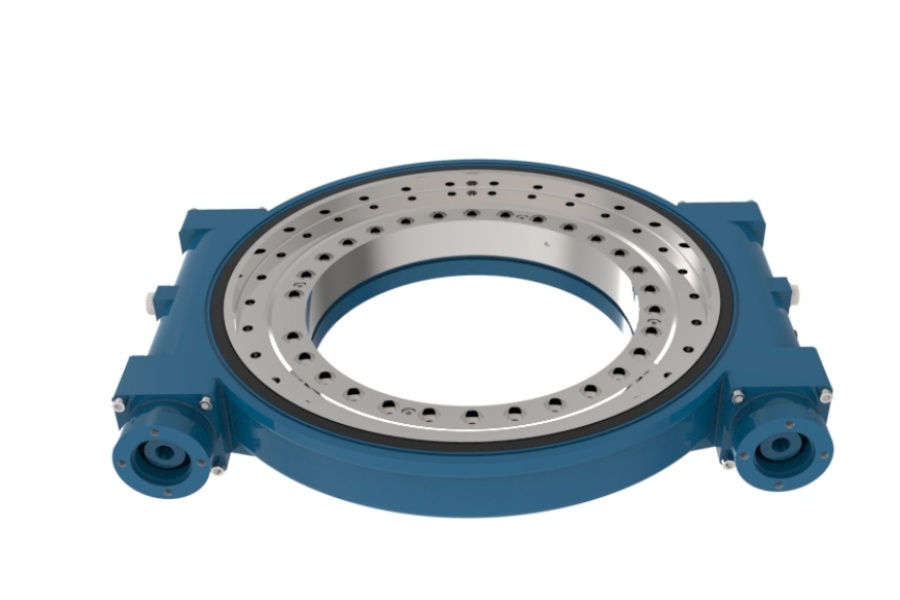
Unleashing Unmatched Power and Control: Your Guide to the Double Worm Slewing Drive WED 25
What is the Double Worm Slewing Drive WED 25?
The Double Worm Slewing Drive WED 25 is a highly engineered rotational drive mechanism combining a robust slewing bearing with a dual-worm gear reduction system. This specific model, designated WED 25, signifies its design series and likely relates to its torque capacity or physical dimensions. At its core, it integrates a large-diameter internal gear ring mounted within the drive's housing with two precisely matched worm screws positioned 180 degrees apart. These worms engage with the gear ring teeth simultaneously. When the input shafts connected to the worms are driven (typically by electric or hydraulic motors), the rotational motion is converted into a powerful, controlled, and highly precise rotation of the housing relative to the base or vice-versa. This unique double-worm configuration is fundamental to its superior performance characteristics, setting it apart from single-worm or pinion-driven alternatives. It's engineered to handle significant radial, axial, and moment loads simultaneously while providing smooth, backlash-minimized rotation under heavy stress.
Double Worm Drive for Crane Applications: The Backbone of Rotation
In the demanding world of crane operations, reliability, safety, and precise control are non-negotiable. The Double Worm Slewing Drive WED 25 is exceptionally well-suited for slewing applications on various crane types, including knuckle boom cranes, offshore cranes, and smaller gantry cranes. Its double-worm design provides inherent safety through fail-safe redundancy. Should one worm drive experience an unexpected failure, the second worm immediately takes over the load, preventing catastrophic uncontrolled rotation – a critical safety feature when handling heavy or sensitive loads. Furthermore, the self-locking nature of the worm gear principle ensures the crane superstructure or boom holds its position securely without drift, even when motors are disengaged or power is lost. This eliminates the need for complex, separate braking systems, enhancing reliability. The WED 25's compact design allows for efficient integration into crane turntables, providing high torque output relative to its size, crucial for slewing loads efficiently. Its robust construction withstands the harsh vibrations, shock loads, and environmental conditions typical on construction sites, vessels, or industrial settings.
Slewing Drive WED 25 Manual: Essential Knowledge for Operation and Care
While specific operational procedures and maintenance schedules must always be sourced from the official LYRADRIVE WED 25 manual provided with the unit or obtained directly from the manufacturer, understanding core manual principles is vital. The manual details critical information such as installation torque specifications for mounting bolts, ensuring the drive is securely fastened to its base and superstructure to handle dynamic loads safely. Alignment procedures are meticulously outlined, as misalignment between the drive and connected components can drastically reduce bearing life and gear performance. Lubrication specifications are paramount; the manual specifies the correct type and grade of lubricant (grease or oil), initial fill volumes, and crucial re-lubrication intervals based on operating hours, load conditions, and environment. Neglecting lubrication is a primary cause of premature drive failure. Load limitations (axial, radial, moment) are clearly defined, and operators must ensure the drive is never subjected to loads exceeding these ratings. The manual also covers inspection routines, highlighting what to look for during visual checks (e.g., seal integrity, unusual noise, lubricant leaks) and scheduled maintenance tasks like gear tooth inspection or backlash measurement. Troubleshooting guides help diagnose common issues like excessive noise, overheating, or erratic movement. Strict adherence to the WED 25 manual is essential for achieving maximum service life, safety, and optimal performance.
Unpacking the Power: Key Features of the Double Worm Slewing Drive WED 25
The WED 25 stands out due to a suite of features engineered for demanding performance
Dual-Worm Redundancy: Two independent worm drives engage the main gear ring simultaneously. This provides inherent fail-safe operation. If one worm fails (e.g., due to a broken shaft or severe gear damage), the other worm immediately takes over the full load, preventing uncontrolled slewing – a critical safety feature.
Superior Self-Locking: The high friction angle inherent in the worm gear design creates a natural braking effect. When input rotation stops, the drive locks its position instantly and reliably without needing external brakes, holding loads securely against back-driving forces.
Exceptional Load Capacity: Engineered with robust bearings (typically crossed roller or triple race roller) and hardened, precision-ground gears (worms and ring gear), the WED 25 handles substantial combined loads – high axial forces, significant radial loads, and large tilting moments – simultaneously and efficiently.
High Precision & Low Backlash: Precision manufacturing of the worm and ring gear mesh ensures minimal backlash (typically specified in arc-minutes). This translates to highly accurate positioning and repeatability, crucial for applications requiring fine control.
Compact & Integrated Design: The WED 25 integrates the slewing bearing, gear reduction, and mounting structure into a single, space-saving unit. This simplifies installation, reduces overall system complexity and weight, and offers a clean design solution.
High Efficiency & Smooth Operation: Optimized gear geometry and high-quality manufacturing result in efficient power transmission and remarkably smooth, quiet rotation, even under heavy load and low speeds.
Robust Construction & Durability: Manufactured from high-strength alloys, featuring hardened gear surfaces, and equipped with effective sealing solutions, the WED 25 is built to endure harsh environments, including exposure to dust, moisture, temperature extremes, and corrosive elements.
High Torque Density: The double-worm design allows the WED 25 to deliver a very high torque output relative to its physical size and weight, making it highly efficient for space-constrained applications.
Versatile Mounting & Input Options: Typically offering multiple mounting hole patterns on both the inner and outer rings, and various input shaft configurations (splined, keyed, flanged) adaptable to different motors or hydraulic systems.
Where Power Meets Precision: Diverse Applications of the WED 25
The unique blend of power, precision, safety, and compactness makes the Double Worm Slewing Drive WED 25 indispensable across numerous industries:
Material Handling & Cranes: Knuckle boom cranes (truck-mounted, marine), offshore cranes, small gantry cranes, crane attachments (rotators), automated guided vehicles (AGVs) requiring rotation, heavy-duty turntables for positioning loads.
Renewable Energy: Solar tracking systems (concentrated solar power - CSP, large photovoltaic - PV trackers) where precise sun following and high wind load resistance are critical. Wind turbine yaw drive backups or small turbine mechanisms.
Industrial Automation & Robotics: Heavy-duty robotic welding cells, material transfer arms, indexing tables for machining, palletizing/depalletizing systems, large valve actuators requiring precise angular control.
Construction Equipment: Access platforms (cherry pickers, scissor lifts - for turntable rotation), drilling rigs (rotary table drive), compactors, specialized foundation equipment.
Defense & Aerospace: Radar and antenna positioning systems, weapon system mounts, missile launcher positioning, ground support equipment requiring reliable and precise rotation.
Medical & Rehabilitation: Heavy-duty patient lifting and transfer equipment, specialized therapy tables requiring smooth, controlled movement.
Agriculture: Large irrigation systems requiring rotational movement, specialized harvesting equipment, heavy-duty spreaders.
Mining & Minerals Processing: Screening equipment drives, feeder mechanisms, conveyor diverters requiring robust rotation under heavy load and abrasive conditions.
Stage & Entertainment: Heavy-duty stage turntables, lighting truss rotation systems requiring silent and reliable operation.
Understanding Investment: Factors Influencing Double Worm Slewing Drive WED 25 Price
The cost of a Double Worm Slewing Drive WED 25 is not a single fixed figure but varies significantly based on several key factors:
Torque Capacity & Size: The fundamental "25" designation often correlates with a specific torque range. Drives designed for higher nominal and peak torque loads require larger, more robust components (gears, bearings, housing), increasing material costs and manufacturing complexity significantly. Larger physical dimensions also contribute to higher cost.
Load Ratings (Axial, Radial, Moment): Beyond torque, the specific load ratings required dictate bearing size and type (e.g., triple race roller bearings cost more than double race), gear tooth geometry, and housing strength. Drives rated for extreme combined loads command a premium.
Precision Requirements (Backlash): Achieving ultra-low backlash (e.g., <1 arc-minute) demands significantly higher manufacturing precision, specialized grinding processes, meticulous assembly, and potentially tighter tolerances on all components, all adding substantial cost compared to drives with standard backlash tolerances.
Materials & Heat Treatment: The grade of steel used for gears and bearings, along with the specific hardening processes (carburizing, induction hardening, nitriding) and depth of hardening, directly impact durability, wear resistance, and cost. Corrosion-resistant coatings or stainless steel components add further expense.
Sealing & Environmental Protection: Standard IP65 sealing is common. Requirements for higher IP ratings (IP67, IP69K), special seal materials for extreme temperatures or chemical resistance, or marine-grade corrosion protection (e.g., anodizing, special paints) increase cost.
Customization & Options: Modifications from the standard WED 25 design drive costs up. This includes special input shaft configurations (splines, keys, flanges), custom mounting hole patterns, integrated sensors (absolute/encoders, temperature, vibration), special lubrication systems (centralized greasing), unique coatings, or non-standard backlash levels. Even special paint colors add cost.
Quantity & Order Volume: Unit pricing is always higher for single units or small batches. Significant discounts are typically applied for larger volume orders due to economies of scale in manufacturing and procurement.
Manufacturer & Brand Reputation: Established manufacturers with proven quality control, rigorous testing protocols, extensive R&D, and global support networks often command higher prices due to the inherent value of reliability, longevity, and technical support. Premium brands justify cost through superior performance and reduced lifecycle costs.
Geographic Location & Supply Chain: Manufacturing location, logistics costs, import duties, taxes, and local market dynamics all influence the final delivered price to the customer.
Supplier of Double Worm Slewing Drive WED 25
When sourcing a critical component like the Double Worm Slewing Drive WED 25, choosing the right supplier is paramount. LYRADRIVE stands as a leading global manufacturer specializing in high-performance slewing drives, bearings, and gearboxes. Choosing LYRADRIVE for your WED 25 needs offers distinct advantages. They possess deep engineering expertise in slewing technology, allowing them to not only supply standard WED 25 units but also provide expert consultation and robust customization capabilities to tailor the drive precisely to your unique application requirements, ensuring optimal fit and performance. LYRADRIVE prioritizes manufacturing excellence, utilizing advanced production techniques, stringent quality control measures (ISO certified), and high-grade materials to ensure every WED 25 drive delivers exceptional durability, reliability, and meets specified performance criteria consistently. Their commitment extends beyond the sale with comprehensive global technical support and readily available spare parts, minimizing downtime and ensuring the long-term operational efficiency of your equipment. Furthermore, LYRADRIVE offers flexible production scales, efficiently catering to projects ranging from single prototype units to large-volume production runs. By partnering with LYRADRIVE, you gain access to a reliable source of innovative, high-quality WED 25 slewing drives backed by the technical knowledge and support necessary for the success of your demanding rotational applications.