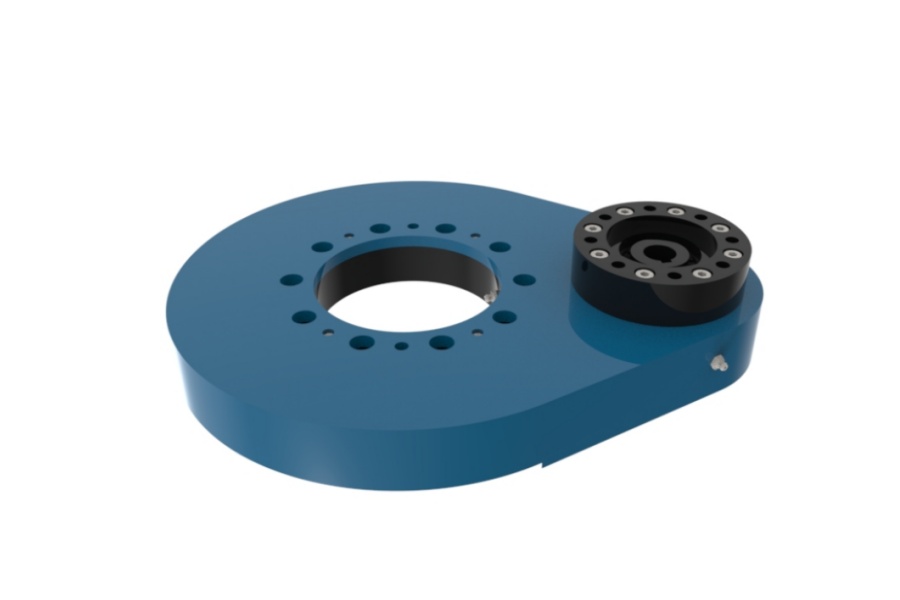
Revolution in Motion: The SP-I 0229 Light Slewing Drive Powering Precision Automation
What is the Lightweight Slewing Ring Gear Drive SP-I 0229?
The SP-I 0229 represents a specific class of gear mechanism known as a lightweight slewing ring drive or external gear slewing bearing drive. It integrates a hardened external gear ring, precision rolling elements (balls or rollers), and mounting interfaces into a single, compact assembly. Unlike bulky traditional slewing rings, the SP-I 0229 prioritizes minimal weight and footprint while maintaining essential load capacity and rotational accuracy. Its core function is to facilitate controlled, often continuous, rotational movement between two machine parts – typically a stationary base and a rotating platform – efficiently transmitting torque from a drive motor (often via a pinion) while handling axial, radial, and moment loads simultaneously.
The Heart of Automation: Enabling Precision Rotation
This drive is fundamentally an Automation Rotation Unit. Its primary role is to provide the controlled rotary motion essential in countless automated systems. Think robotic arms needing precise articulation for welding or assembly, indexing tables positioning components under a camera or tool, medical scanners rotating imaging components, or automated guided vehicles (AGVs) with rotating transfer platforms. The SP-I 0229 excels as the core component enabling these rotational axes. Its compact design allows it to be integrated directly into the joint or pivot point of machinery, minimizing overall system complexity and space requirements. The unit handles the demanding task of supporting loads and transferring motion reliably, freeing engineers from designing complex rotary bearings and drives from scratch.
The Driving Force: Integrated Small Reducer Concepts
While the SP-I 0229 itself is the output stage, its effective operation often relies on pairing with a Small Reducer or gearmotor. This reducer acts as the prime mover, stepping down the high speed, low torque output of a standard electric motor to the lower speed, higher torque input required to drive the pinion meshing with the SP-I 0229's gear ring. Compact planetary gearboxes, precision worm gear reducers, or even integrated servo gearmotors are common choices. The reducer selection is critical: it must deliver sufficient torque to overcome the load and friction within the slewing drive, provide the desired output speed for the application, and fit within the spatial constraints. The synergy between the robust SP-I 0229 slewing drive and a precisely matched small reducer creates a complete, highly efficient rotary drive solution.
Core Technology: Robust Gear Transmission
At its essence, the SP-I 0229 functions via Gear Transmission. The hardened external gear teeth cut into its outer ring mesh precisely with a smaller drive pinion connected to the output shaft of the reducer/motor. As the pinion rotates, it drives the large gear ring, resulting in the rotation of the entire structure attached to the slewing drive. This gear meshing is the fundamental power transmission path. Precision manufacturing of these gears is paramount for smooth operation, minimal backlash (play between teeth), high efficiency, low noise generation, and long service life. Advanced grinding techniques ensure optimal tooth profiles and surface finishes. The gear transmission within the SP-I 0229 is designed to handle significant operational forces reliably, making it far more robust than simple bearings or bushings for demanding rotational tasks.
Key Features Defining the SP-I 0229 Advantage
The Lightweight Slewing Ring Gear Drive SP-I 0229 stands out due to a compelling set of engineered features tailored for modern automation. Its most defining characteristic is its exceptional lightweight construction, achieved through optimized structural design and material selection, drastically reducing inertia and enabling use on moving platforms. Compactness is paramount, featuring a low cross-sectional height and minimal footprint for seamless integration into tight spaces. Despite its size, it delivers significant load capacity, adeptly managing combined axial, radial, and tilting moment loads common in dynamic applications. Engineered for high rotational precision and minimal backlash, it ensures repeatable positioning accuracy crucial for robotics and assembly. Smooth and quiet operation results from precision-ground gearing and optimized preload. Robust sealing protects internal components from dust, dirt, and splashes, enhancing reliability in harsh environments. Designed for ease of integration, it features standardized mounting patterns and readily accessible lubrication points. Finally, its high efficiency minimizes power loss and heat generation during operation.
Diverse Applications Leveraging Compact Rotary Power
The Lightweight Slewing Ring Gear Drive SP-I 0229 finds extensive application across industries demanding precise, reliable, and space-efficient rotation. In Industrial Robotics, it forms critical joints in articulated arms for material handling, welding, and assembly, enabling precise motion within compact arm designs. Automated Material Handling systems utilize it in rotary indexing tables, pallet positioners, and transfer carousels for precise component positioning. Within Packaging Machinery, it drives rotating filling heads, capping stations, and label applicators requiring smooth motion. Medical and Laboratory Automation benefits from its precision and cleanliness in diagnostic equipment, sample handlers, and surgical robot joints. Automated Guided Vehicles (AGVs) and Mobile Robots rely on it for rotating transfer platforms, lifting columns, and sensor mounts where low weight is critical for battery life and maneuverability. Solar Tracking Systems employ it to precisely orient panels, leveraging its durability and load capacity. Semiconductor Manufacturing equipment uses it in wafer handling stages and inspection tools requiring ultra-clean, precise motion. Defense and Aerospace applications value its compact power for sensor turrets and communication platforms. Construction Equipment incorporates it into compact machinery controls and instrumentation.
Understanding SP-I 0229 Pricing Dynamics
Several key factors influence the Price of the Lightweight Slewing Ring Gear Drive SP-I 0229. Material selection is fundamental; high-grade alloy steels for rings and rolling elements, along with specialized seals and lubricants, significantly impact cost. The precision level required plays a major role; drives manufactured to ultra-tight tolerances for minimal backlash and high positional accuracy command a premium due to advanced machining and grinding processes. Load capacity and size specifications directly correlate to cost; a drive rated for higher loads or featuring larger dimensions inherently requires more material and robust manufacturing. Customization adds expense; modifications like special mounting holes, unique lubrication systems, specific seal types (e.g., high-temperature), special coatings (corrosion resistance), or non-standard gear modules increase manufacturing complexity. Order volume is crucial; larger production runs benefit from economies of scale, reducing the unit cost significantly compared to small-batch or prototype orders. Required certifications (e.g., ISO, specific industry standards) add to testing and documentation costs. Finally, the complexity of the internal rolling element design (ball vs. roller, single vs. double row) and the quality of seals and bearings contribute to the final price point.
Supplier of Lightweight Slewing Ring Gear Drive SP-I 0229
When seeking a reliable supplier for the Lightweight Slewing Ring Gear Drive SP-I 0229 and similar advanced motion solutions, LYRADRIVE stands as a leading partner. We specialize in the design, engineering, and manufacturing of high-precision slewing drives, gearboxes, and integrated rotary solutions. Our expertise lies in understanding complex application requirements and delivering optimized components like the SP-I 0229 that excel in performance, reliability, and integration ease. LYRADRIVE emphasizes rigorous quality control throughout the manufacturing process, utilizing state-of-the-art machining and inspection equipment to ensure every unit meets stringent specifications for precision, load capacity, and durability. Beyond standard catalog offerings, we provide significant engineering support for customization, tailoring solutions to unique spatial constraints, specific load profiles, environmental conditions, or interface requirements. Our technical team offers comprehensive application engineering assistance, helping customers select the optimal drive configuration, integrate it effectively, and troubleshoot any challenges. Committed to innovation, LYRADRIVE continuously refines designs like the SP-I 0229 to push the boundaries of power density, efficiency, and compactness, ensuring our customers have access to the most advanced rotary transmission technology for their automation challenges. Partnering with LYRADRIVE means securing not just a component, but a dedicated resource for achieving superior motion control performance.