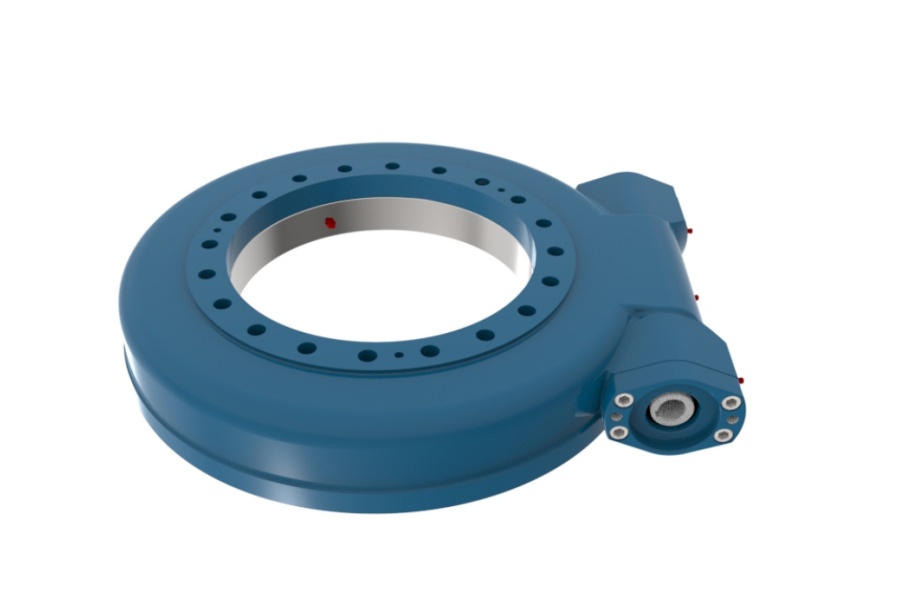
The WE17 Worm Gear Drive: Engineering the Impossible in Motion Control
What is the Worm Gear Drive WE17?
The Worm Gear Drive WE17 represents the pinnacle of precision power transmission technology, engineered specifically for scenarios demanding immense torque multiplication, compact design, and unwavering reliability under duress.
At its core, it utilizes a hardened steel worm screw engaging with a bronze or specialized alloy worm wheel. This unique configuration creates a high reduction ratio in a single stage, allowing a small input force to generate massive output torque. Unlike conventional gearboxes, the WE17's design inherently provides self-locking capabilities under certain ratios, preventing back-driving and enhancing safety in vertical or holding applications. It's meticulously crafted for industrial, aerospace, and research applications where failure is not an option, featuring advanced materials, precision grinding, optimized lubrication systems, and robust sealing to withstand contamination and extreme operating conditions. The WE17 isn't just a gearbox; it's a meticulously engineered solution for transmitting power efficiently and reliably in the most demanding environments on Earth and beyond.
Conquering the Cosmos: WE17 Microgravity Environment Deceleration Performance
The harsh realities of space, particularly microgravity, pose unique challenges for mechanical systems like gear drives. Lubrication behavior drastically changes, with oils potentially floating away or failing to adequately coat surfaces, leading to increased wear or catastrophic failure. Traditional thermal management becomes less effective without convection. The WE17 worm drive is uniquely engineered to overcome these obstacles. Its design incorporates specialized forced-oil lubrication systems with scavenge pumps ensuring continuous oil flow over critical worm and wheel surfaces, regardless of gravitational orientation. Advanced synthetic lubricants with exceptional wetting characteristics and low volatility are specified to perform reliably in vacuum and extreme temperature swings. Materials are selected for dimensional stability under thermal cycling and low outgassing properties to prevent contamination of sensitive spacecraft instruments. The inherent compactness and high torque density of the worm drive architecture minimize system mass and volume, crucial for space applications. Rigorous testing in simulated microgravity and thermal vacuum chambers validates the WE17's ability to provide precise, reliable deceleration and positioning control for satellite deployment mechanisms, robotic arms on space stations, planetary rover actuators, and scientific instrument drives, proving its capability where conventional drives falter.
Megawatt Muscle: Scaling the WE17 for Heavy Industrial Domination
While often associated with compact applications, the fundamental principles of the WE17 worm drive are expertly scaled to create robust megawatt-class drive systems for the most demanding industrial tasks. Scaling involves overcoming significant thermal and mechanical challenges.
Massive worm shafts are crafted from ultra-high-strength alloys, undergoing precision grinding and specialized heat treatments like induction hardening or nitriding to achieve unparalleled surface hardness and core toughness.
Correspondingly large worm wheels utilize advanced bronze alloys or even ductile iron with specialized polymer composites, engineered for high load capacity and wear resistance under extreme pressure. Efficient heat dissipation becomes paramount.
MW-scale WE17 systems incorporate sophisticated cooling strategies, including integrated water or oil cooling jackets around the housing, forced-air ventilation systems, and optimized oil circulation with high-capacity external coolers. Advanced bearing technology, often involving hydrodynamic or hydrostatic principles, supports the enormous radial and thrust loads generated.
Precision manufacturing ensures perfect alignment and tooth contact patterns to distribute loads evenly, minimizing stress concentrations and maximizing service life. These behemoths deliver immense torque for driving massive rotary kilns in cement production, powering heavy-duty ship winches and offshore cranes, actuating giant sluice gates in hydroelectric plants, and providing the core drive for large-scale material handling systems like bucket wheel excavators in mining. The WE17 architecture proves that worm drives can indeed be the powerhouse solution for multi-megawatt applications.
Shielding the Spin: WE17 Material Science for Strong Magnetic Field Eddy Current Suppression
Operating high-precision gear drives within strong static or dynamic magnetic fields, such as those found in MRI machines, particle accelerators (like synchrotrons or cyclotrons), fusion reactors, or specialized magnetic processing equipment, introduces a critical challenge: eddy currents. Induced currents within conductive components (like the worm wheel or housing) by changing magnetic fields generate parasitic heat (Joule heating) and create opposing Lorentz forces that manifest as drag torque, vibration, and positioning errors. Standard metallic components are unusable.
The WE17 adapted for such environments undergoes a radical material transformation. The core innovation lies in replacing conductive worm wheels with high-performance engineering ceramics (like silicon nitride - Si3N4) or specialized composite materials reinforced with non-conductive fibers. These materials exhibit exceptional mechanical strength, wear resistance, and near-zero electrical conductivity, effectively eliminating eddy currents.
Supporting components like shafts, bearings, and housings utilize non-magnetic alloys (e.g., specific austenitic stainless steels like 316L, titanium alloys like Ti-6Al-4V, or high-strength aluminum alloys like 7075-T6). These alloys are selected for their excellent mechanical properties combined with low magnetic permeability and low electrical conductivity. Even fasteners and seals are meticulously chosen to be non-magnetic and non-conductive. Rigorous Finite Element Analysis (FEA) guides material selection and component design to minimize residual magnetic susceptibility and eddy current paths. The result is a WE17 drive that delivers precise, smooth motion and reliable torque transmission without generating disruptive heat or forces, enabling critical operations within the heart of powerful magnetic fields.
Unpacking the Power: Defining Features of the WE17 Worm Gear Drive
The WE17 Worm Gear Drive distinguishes itself through a constellation of meticulously engineered features designed for peak performance and endurance.
Its most celebrated attribute is exceptional torque density, delivering immense output torque from a remarkably compact and lightweight package, optimizing space utilization in complex machinery. Achieving reduction ratios exceeding 100:1 in a single stage is routine, drastically simplifying drivetrain design compared to multi-stage alternatives.
A critical feature is its inherent self-locking capability under specific reduction ratios, providing failsafe holding power essential for vertical lifts, positioning stages, and safety-critical applications without needing external brakes.
Precision-ground worm and wheel profiles, coupled with advanced manufacturing tolerances and specialized surface finishes, ensure exceptionally smooth, quiet operation with minimal vibration, even at high loads. Robust construction utilizing high-grade alloys and advanced heat treatments guarantees outstanding durability and resistance to wear and pitting under heavy shock loads and continuous operation. Sophisticated sealing systems, employing multiple labyrinth seals, specialized lip seals, or magnetic seals combined with high-performance grease or oil lubrication, provide exceptional protection against ingress of dust, moisture, and other contaminants, extending service life dramatically in harsh environments. Advanced thermal management features, including optimized housing fins, integrated cooling channels, or provisions for forced air/oil, effectively dissipate heat generated under high loads. Finally, versatile mounting configurations (foot, flange, shaft mount) and adaptable input/output options offer maximum flexibility for seamless integration into diverse mechanical systems, making the WE17 an incredibly adaptable and powerful solution.
Where Excellence Performs: Diverse Applications of the WE17 Drive
The unique combination of power, compactness, reliability, and control offered by the WE17 Worm Gear Drive makes it indispensable across a vast spectrum of demanding industries.
In heavy industrial automation, it powers robotic arms for welding and material handling, drives conveyor systems moving massive loads, and operates heavy-duty valves and gates in processing plants. The construction and mining sectors rely on WE17 drives for excavator slew mechanisms, crane hoists and slewing rings, and conveyor drives, benefiting from their high torque and shock load resistance.
Material handling thrives on the WE17, driving palletizers, automated storage and retrieval systems (AS/RS), heavy-duty lifts, and dock levelers with precision and holding security. Aerospace and defense applications leverage its reliability in aircraft cargo handling systems, missile actuator controls, radar positioning drives, and ground support equipment.
Medical technology utilizes specialized WE17 variants for precise positioning in radiation therapy machines (LINACs), MRI patient table movement (using non-magnetic versions), and sophisticated surgical robotics requiring smooth, powerful motion. Renewable energy employs them for solar tracker azimuth and elevation drives and for adjusting pitch in large wind turbine blades. Research pushes boundaries with WE17 drives powering actuators in particle accelerators (using eddy-current-suppressed versions), telescope positioning systems requiring extreme precision, and experimental apparatus in harsh environments. From factory floors to orbital platforms, the WE17 delivers reliable power transmission where it matters most.
Understanding Investment: Key Factors Influencing WE17 Worm Gear Drive Pricing
The price of a WE17 Worm Gear Drive is not a simple figure but reflects the culmination of sophisticated engineering, materials, and manufacturing processes required to meet its demanding specifications. Material selection is paramount; the use of ultra-high-strength alloy steels for the worm, specialized bronze alloys or advanced composites for the wheel, and non-magnetic alloys (like titanium or specific stainless steels) for specialized versions significantly increases raw material costs compared to standard gearboxes.
The complexity and precision of manufacturing are major cost drivers. Precision grinding of the hardened worm thread and worm wheel teeth to achieve the necessary tolerances, surface finishes, and perfect meshing requires advanced CNC machinery and highly skilled labor, representing a substantial portion of the cost.
Required reduction ratio and torque capacity directly impact size and material volume; larger, higher-torque drives naturally cost more due to increased material usage and machining time. Specialized features demanded by the application add cost layers; this includes integrated encoders or resolvers for feedback, non-standard mounting configurations (custom flanges or shafts), forced lubrication systems with pumps and coolers, advanced thermal management solutions (water cooling jackets), and extensive sealing systems for extreme environments (IP69K). Compliance with stringent certifications like ATEX for explosive atmospheres or specific aerospace/military standards (MIL-STD, DO-160) involves additional testing and documentation costs. Finally, order volume plays a role; low-volume production runs for highly customized units incur higher per-unit costs compared to standardized, higher-volume configurations. The WE17's price reflects its value proposition: exceptional performance, reliability, and longevity in the most challenging applications.
Engineered for the Edge: The WE17 Legacy
The Worm Gear Drive WE17 stands as a testament to precision engineering conquering extreme operational frontiers. From the relentless demands of megawatt industrial drives to the unforgiving void of space and the disruptive forces of powerful magnetic fields, the WE17 consistently delivers uncompromising torque, unwavering reliability, and precise control.
Its defining features – exceptional torque density, high reduction ratios, inherent self-locking, robust construction, and advanced sealing – are not merely specifications but solutions forged for real-world challenges. Whether automating a factory floor, positioning a satellite component in orbit, enabling cutting-edge medical treatment, or driving fundamental scientific discovery, the WE17 provides the robust, dependable motion control foundation.
Understanding its value requires recognizing the sophisticated materials, meticulous manufacturing, and specialized adaptations that justify its investment. For applications where failure is catastrophic and performance is non-negotiable, the WE17 Worm Gear Drive remains the engineered choice, powering progress at the very edge of what's mechanically possible.
Supplier of Worm Gear Drive WE17
LYRADRIVE professional team is ready to provide you with precise selection support, flexible non-standard customization solutions (special shaft extensions, flanges, seals, coatings, etc.), and timely, localized technical services. We are committed to being your trusted power transmission partner, helping you effectively reduce overall equipment operating costs and enhance production efficiency.