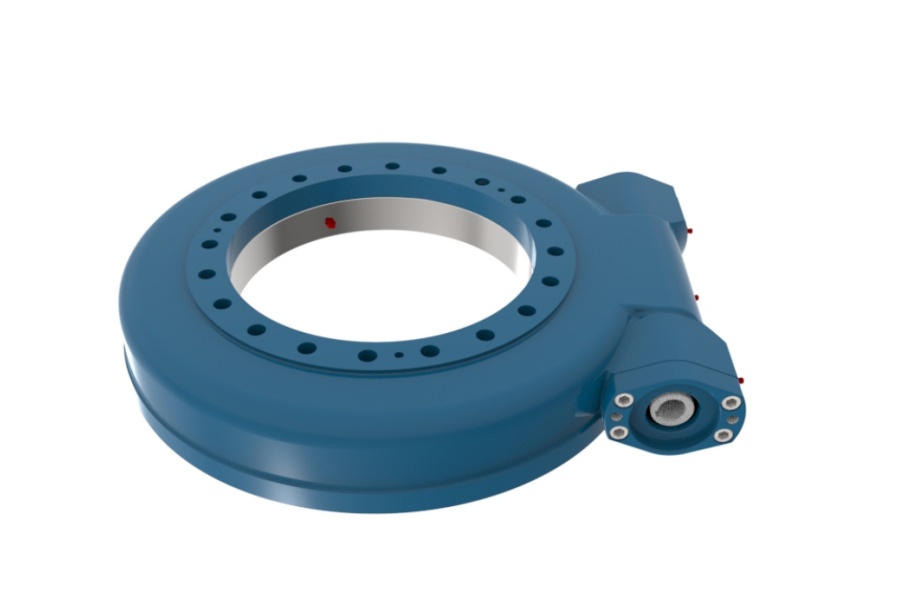
The SE17 Enveloping Slewing Drive: Mastering Torque and Endurance Where Others Fail
What is the Enveloping Slewing Drive SE17?
The Enveloping Slewing Drive SE17 represents a pinnacle of rotary motion technology. It's a compact yet immensely robust drive unit integrating a high-capacity slewing bearing, a precision gearbox (typically worm-driven), mounting structure, seals, and often a motor, into a single, self-contained package. The defining "enveloping" feature refers to its unique worm gear design. Here, the worm wheel partially wraps around the worm shaft. This crucial geometry dramatically increases the contact area between the worm threads and the wheel teeth compared to standard designs. The result is significantly higher torque transmission capability within a remarkably compact footprint. The SE17 designation signifies its specific size, torque rating, and design characteristics, tailored for applications demanding exceptional power density and resilience against harsh operating conditions, including heavy loads, shock, vibration, subsea pressures, and arctic temperatures.
High Torque Density: The SE17's Defining Power
The core superpower of the Enveloping Slewing Drive SE17 lies in its extraordinary torque output relative to its size – its torque density. The enveloping worm gear principle is fundamental to this achievement. By maximizing the contact area between the worm and wheel, the SE17 distributes immense forces over a larger surface, drastically reducing localized stress and preventing premature wear or deformation. This design allows it to generate significantly higher torque than similarly sized conventional slewing drives using spur or helical gears, or even standard worm gears. This high torque density translates directly into practical advantages: enabling lighter overall machinery structures, reducing spatial requirements in cramped installations, improving power-to-weight ratios for mobile equipment, and providing a substantial safety margin for handling peak loads and unexpected shocks. For engineers pushing the boundaries of performance within space and weight constraints, the SE17's torque capability is revolutionary.
Conquering Subsea Peril: Preventing Slewing Drive Failure
Subsea equipment operates in one of Earth's most hostile environments: crushing pressures, corrosive saltwater, abrasive sediments, and near-zero accessibility for maintenance. Slewing drive failure here isn't just inconvenient; it's catastrophic, leading to costly downtime, complex retrieval operations, and potential environmental risks. The Enveloping Slewing Drive SE17 is specifically engineered to defy these challenges. Its robust, sealed housing is designed to withstand extreme hydrostatic pressure, preventing seawater ingress that causes corrosion and lubrication washout. Advanced multi-stage sealing systems, often incorporating special elastomers and exclusion barriers, keep contaminants out and vital grease in. Critical internal components utilize corrosion-resistant alloys or receive specialized coatings. Crucially, the enveloping gear design's inherent high contact area and reduced stress minimize wear particle generation, a major cause of internal damage in sealed environments. The SE17's reliability under these relentless conditions makes it indispensable for remotely operated vehicles (ROVs), subsea manipulators, trenching systems, and subsea production equipment, ensuring mission success far beneath the waves.
Defying the Deep Freeze: Reliable Operation at -50°C
Arctic operations, cryogenic facilities, and high-altitude applications demand equipment that functions flawlessly in bone-chilling cold. Standard lubricants solidify, metals become brittle, seals lose elasticity, and tolerances shift, often leading to slewing drive seizure or catastrophic failure. The Enveloping Slewing Drive SE17 is meticulously designed and tested to operate reliably down to -50°C and beyond. This requires a holistic approach. Specialized low-temperature greases are selected, formulated to maintain proper viscosity and lubricity even in extreme cold, preventing excessive friction and wear. Critical internal components, such as bearings and gears, utilize steels with proven toughness and impact resistance at sub-zero temperatures to prevent brittle fracture. Seals are crafted from elastomers specifically engineered to retain flexibility and sealing capability in deep freeze conditions. Furthermore, manufacturing tolerances and assembly processes are optimized to account for thermal contraction, ensuring smooth, binding-free rotation regardless of the plummeting mercury. This certified low-temperature capability opens doors for the SE17 in applications like icebreaking vessel cranes, Arctic drilling rigs, cryogenic storage handling systems, and Antarctic research equipment.
Unpacking the SE17's Engineered Advantages
The Enveloping Slewing Drive SE17 isn't just about brute force or surviving extremes; it integrates numerous features for superior performance:
Unmatched Torque Density: The enveloping worm gear principle delivers exceptional torque in a compact package.
Self-Locking Capability (Optional): The worm drive design inherently provides a high holding brake ratio, preventing back-driving under load without needing an external brake (depending on ratio/design).
High Rigidity & Precision: Robust construction ensures minimal deflection under load, providing precise positioning and smooth motion control.
Integrated Design: Combines bearing, gearing, housing, and often motor mount into one unit, simplifying installation and saving space.
Extreme Environmental Sealing: Multi-stage seals and pressure-compensated designs protect against water, dust, grit, and high pressure ingress.
Corrosion Resistance: Utilizes high-grade materials, protective coatings, and stainless steel options for longevity in harsh conditions.
Wide Temperature Range: Specifically engineered versions operate reliably from -50°C to well above +80°C.
High Load Capacity: Designed to handle significant axial, radial, and moment loads simultaneously.
Low Maintenance: High-quality seals and long-life lubricants minimize maintenance intervals, crucial for remote or inaccessible installations.
Customization: Often available with various mounting configurations, flange options, gear ratios, motor interfaces, and sealing levels.
Where the SE17 Dominates: Diverse Applications Demanding Excellence
The unique combination of power, compactness, and resilience makes the Enveloping Slewing Drive SE17 the drive of choice across numerous demanding sectors:
Subsea Technology: ROVs, AUVs, subsea manipulators, trenching systems, cable lay equipment, subsea production tooling.
Heavy Machinery: Crane jibs and hooks, heavy-duty positioning stages, material handling robots, mining equipment slew rings.
Renewable Energy: Solar tracker azimuth and elevation drives (especially in harsh environments), wind turbine pitch and yaw adjustment mechanisms (smaller turbines or auxiliary systems).
Defense & Aerospace: Weapon system positioning, radar and antenna mounts, missile launcher drives, ground support equipment.
Industrial Automation: Heavy-duty rotary indexing tables, robotic welding positioners, automated assembly line turntables requiring high precision under load.
Marine & Offshore: Deck cranes, winch positioning systems, hatch covers, offshore crane auxiliary functions.
Cold Chain & Cryogenics: Automated handling systems in freezer warehouses, liquid nitrogen handling equipment, Arctic logistics machinery.
Medical & Scientific: Heavy-duty positioning in imaging equipment (CT/MRI), telescope mounts requiring high stability, specialized research apparatus.
Understanding the Investment: Factors Influencing SE17 Price
The Enveloping Slewing Drive SE17 is a premium component, and its price reflects the advanced engineering and materials required. Key factors include:
Torque Rating & Size: Higher torque capacities and larger physical sizes inherently require more material and complex manufacturing, increasing cost.
Gear Ratio: Different ratios require specific worm and wheel configurations, impacting machining complexity.
Material Selection: Extensive use of high-strength alloy steels, specialized corrosion-resistant materials (e.g., stainless steel components), or specific hardening/treatment processes significantly raises costs compared to standard carbon steel.
Sealing & Protection Level: Achieving IP69K, high-pressure subsea ratings, or extreme temperature sealing requires complex multi-stage seals, special housings, and pressure compensation systems, adding substantial expense.
Customization: Modifications from standard designs (custom flanges, mounting holes, special shaft configurations, integrated sensors, unique coatings) involve additional engineering and manufacturing steps.
Certifications: Meeting stringent industry standards (e.g., API, DNV, ABS, MIL-SPEC) requires rigorous testing, documentation, and quality control processes, adding to the cost.
Bearing & Gear Quality: Precision-ground, high-grade bearings and gears from reputable manufacturers cost more but are essential for performance and longevity.
Low-Temperature Package: Special lubricants, low-temp seals, and material certifications for cryogenic operation incur additional costs.
Quantity: Unit cost typically decreases with higher volume production orders due to amortized setup costs.
Supplier of Enveloping Slewing Drive SE17
When sourcing an Enveloping Slewing Drive SE17, partnering with a manufacturer possessing deep expertise in extreme-duty applications is paramount. LYRADRIVE stands as a leader in this specialized field. We don't just supply components; we engineer solutions for the most challenging environments on (and under) the planet. Our SE17 drives are the culmination of extensive research, cutting-edge manufacturing techniques, and rigorous testing protocols. LYRADRIVE's commitment to quality is evident in every aspect: from the selection of aerospace-grade materials and precision machining to the implementation of advanced sealing technologies and comprehensive performance validation under simulated operational extremes (pressure, temperature, corrosion, load cycling). We understand that reliability isn't optional; it's the foundation. Our engineering team works closely with clients to tailor the SE17 to specific application requirements, ensuring optimal performance, longevity, and value. Whether your challenge lies in the abyssal depths, the frozen Arctic, or a high-precision industrial setting, LYRADRIVE provides the proven Enveloping Slewing Drive SE17 technology and the engineering support necessary to ensure your project's success, delivering uncompromising power and reliability where it matters most.