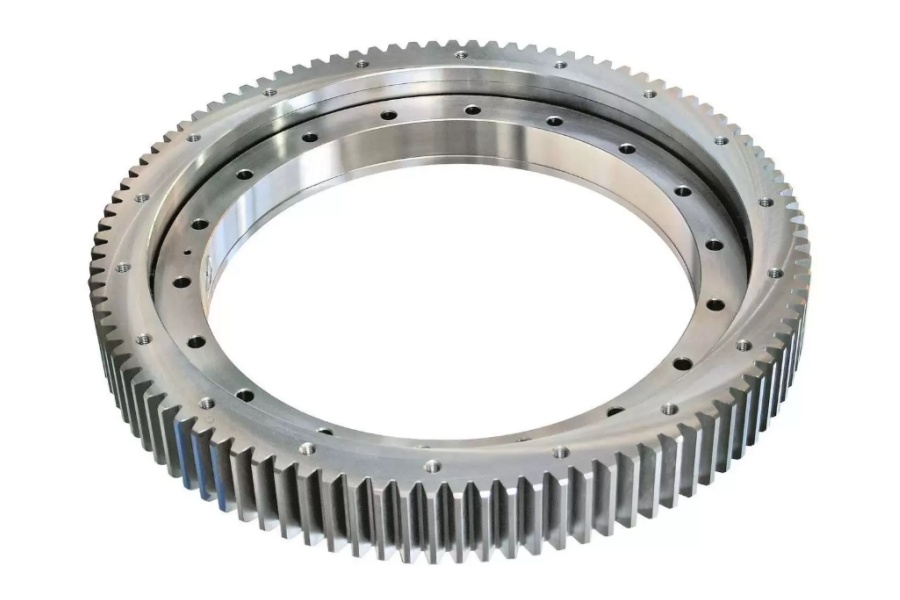
The Rotational Core of Heavy Machinery: Slewing Bearing
The slewing bearing is the core load-bearing component enabling 360° smooth rotation in heavy equipment. Through its integrated design, it replaces traditional bearing systems, handling complex loads in sectors like construction machinery and renewable energy, ensuring safe and efficient operation.
What is a Slewing Bearing?
A slewing bearing is an extra-large rolling-element bearing composed of inner and outer rings, rolling elements (balls/rollers), spacer blocks, and a sealing system. Its core value lies in simultaneously withstanding axial forces, radial forces, overturning moments, and torque, directly connecting a machine’s rotating and fixed structures. Geared variants also integrate internal/external gear rings to mesh with drive units for power transmission.
Core Characteristics of Slewing Bearings
Composite Load Capacity: A single bearing handles kiloton-level axial forces + hundred-ton-level radial forces + high overturning moments.
Highly Integrated Structure: Combines support, rotation, and force transmission functions, reducing assembly components by 40%.
Ultra-Long Service Life: Crafted from high-carbon chromium steel (e.g., 42CrMo), surface hardness HRC58-62, lifespan exceeding 50,000 hours.
Extreme Environment Adaptability: IP66 sealing and specialty grease tolerate temperatures from -40°C to 120°C, dust, and corrosive media.
Customization Flexibility: Supports bespoke configurations for gear tooth profiles (involute/cycloidal), mounting hole patterns, and oil passageways.
Core Application Fields
Construction Machinery: Excavator swing rings, crane slewing platforms
Clean Energy: Wind turbine yaw/pitch systems, solar tracker bases
Industrial Equipment: Tunnel boring machine cutterheads, port cranes, welding positioners
Specialized Sectors: Radar antenna pedestals, missile launchers, medical CT scanner gantries
Critical Role in Excavators
In hydraulic excavators, the slewing bearing is the key connector between the upper structure and undercarriage, performing three core tasks:
Supporting the entire machine’s operating weight (30-50 tons axial load)
Resisting digging reaction overturning forces (500-2,000 kN•m moments)
Enabling 360° continuous rotation of the upper structure (via hydraulic motor-driven gear ring)
Its impact resistance and sealing reliability directly determine equipment durability in harsh conditions like mud and gravel.
Precision Assembly Key Points
Slewing bearing assembly quality directly impacts lifespan. Critical controls include:
Mounting Surface Flatness: Base flatness error ≤0.1mm/m to prevent localized stress concentration.
Bolt Preload: Controlled via torque + angle method, preload deviation ≤5%.
Gear Meshing Calibration: Tooth flank clearance 0.1-0.3mm (per DIN 3967 standard).
Lubrication System Integration: Automatic greasing channels ensure lifelong raceway lubrication.
Professional assembly requires laser alignment tools for flatness checks and hydraulic tensioners for bolt load control.
Special Requirements for Crane Applications
Slewing bearings for cranes must meet three stringent demands:
Tower Cranes: Focus on wind load overturning resistance (1.5 kN/m² wind pressure conditions).
Mobile Cranes: Emphasize shock load resistance (dynamic load factor 1.5 during sudden lifting).
Port Cranes: Require salt spray corrosion resistance (C5-M grade protection).
High-end products use dual-row unequal-diameter ball + crossed roller hybrid designs, boosting moment capacity by 30%.
Key Design Parameters Explained
High-performance slewing bearing design balances six parameters:
Raceway Profile: Four-point contact ball type (cost-effective) vs. crossed roller type (high rigidity).
Gear Ring Design: Module 4-20mm, accuracy DIN 6-9 grade, carburized case depth ≥2mm.
Material Selection: Base material 42CrMo/50Mn, raceway surface hardness HRC58±2.
Safety Factors: Static ≥1.5, dynamic fatigue life ≥30,000 hours.
Sealing Structure: Triple lip seals + polyurethane protective covers.
Lubrication Solution: Lithium-based grease + central lubrication system channels.
In-Depth Price Factor Analysis
Size & Load Capacity: 1m diameter increase raises cost 60% (material + heat treatment surge).
Material Grade: 42CrMo alloy steel costs 80% more than Q235; vacuum degassed steel adds 15%.
Gear Processing: Ground teeth (DIN 6 grade) cost 30% more than milled teeth (DIN 9 grade).
Heat Treatment: Deep carburizing & quenching (2.5mm depth) costs 40% more than medium-frequency hardening.
Protection: IP66 sealing + specialty coatings (e.g., Dacromet) increases cost by 25%.
Batch Effect: Orders >1,000 units reduce unit price by 18%-22%.
Recommended Professional Manufacturer
LYRA Drive provides full-scenario solutions:
Product Range: Diameter 0.2m-5m, static load 10kN-100,000kN
Core Advantages:
DIN 6 grade gear accuracy (ground teeth)
Base materials 50Mn/42CrMo (imported vacuum degassed steel)
Certified dynamic lifespan (ISO 281 standard)
FEA load simulation for optimized design
OEM supplier for industry leaders like Sany Heavy Industry and Goldwind, offering lifetime technical support.
Supplier of Slew drive
LYRA Drive is a professional slewing bearings ,slew drive and gears manufacturer provides customized slew bearing, drive and gears.For application-specific engineering solutions, contact LYRA to discuss technical specifications and implementation strategies.