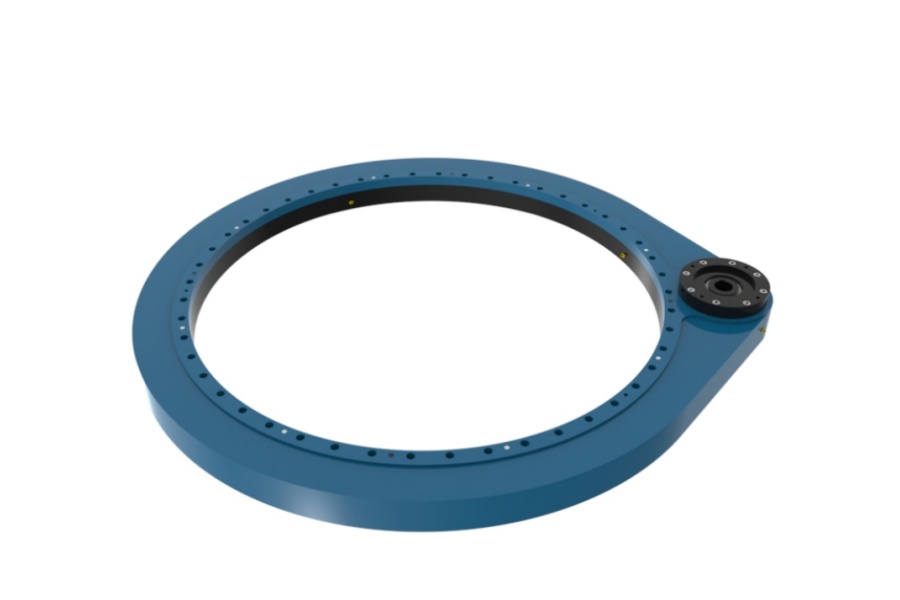
Silent Speed Revolution: How Spur Gear Slew Drives Crush Traditional Rotation Solutions
What is Spur Gear Slew Drive?
A spur gear slew drive operates on parallel-axis gear engagement principles. Its structure comprises three critical components: a slewing bearing with precision external gear ring serving as the rotational base, a hardened alloy steel spur pinion as the power input unit, and a high-rigidity cast aluminum housing integrating sealing and lubrication systems. When the motor drives the pinion, the linear gear-to-rack engagement rotates the load through 360 degrees continuously. Its fundamental advantages over worm gear drives include zero axial thrust and over 30% higher efficiency.
Spur Gear Slew Drive Five Core Advantages Redefining Competition
Ultimate Energy Efficiency
Straight tooth profiles minimize sliding friction losses below 5%, achieving 95-98% transmission efficiency. Real-world data from an international beverage giant’s filling line shows annual electricity savings equivalent to 120 tons of carbon emissions, cutting $180,000 in power costs.
Blazing Speed Capability
Standard units support 200-800 RPM input, with custom models breaking the 1,500 RPM barrier. Bosch Rexroth’s emergency-stop drive for sorting robots completes 500-degree rotations in 0.2 seconds – 5x faster than conventional solutions.
Cost Control Mastery
Spur gear manufacturing requires no special tooling, reducing batch production costs by 25%. Modular designs allow single-gear replacement at just 15% of assembly cost, unlike worm gear sets which require complete replacement.
Micron-Level Precision Control
Preload spring backlash elimination technology stabilizes positional deviation within ±0.03°. A Swiss precision instrument manufacturer achieved 0.001mm repeatability in wafer-handling robots using this technology.
Maintenance-Free Breakthrough
Sealed gear chambers filled with long-life grease operate maintenance-free for 5 years. Compared to monthly filter changes in hydraulic drives, maintenance costs plummet by 80%.
Spur Gear Slew Drive Three Technological Revolutions in High-Speed Drives
Dynamic Balance Innovation
Laser-assisted mass correction technology limits vibration amplitude to 0.03mm at 1,500 RPM. Bonfiglioli’s field data confirms 4,000-hour bearing life extension.
Thermal Management Revolution
Nano-ceramic gear coatings reduce friction coefficients by 50%, while micro-channel liquid cooling maintains temperature rise below 15°C in 180°C injection molding environments.
Impact Resistance Matrix
Carburized gears hardened to HRC62 combined with triple-contact slewing rings withstand 15x rated torque shocks. Port crane applications demonstrate emergency brake failure rates below 0.01%.
Spur Gear Slew Drive Noise Reduction Solutions
Acoustic Tooth Profile Optimization
Tip relief eliminates 90% of meshing impact noise, while crowned teeth compensate mounting deviations for 8dB overall reduction. SKF’s silent drives achieve office-compatible 62dB levels.
Ultra-Precision Manufacturing
ISO Grade 5 gears ensure pitch errors ≤0.005mm, with each precision grade reducing noise by 5dB. Sumitomo Heavy Industries’ medical CT drives reach 55dB whisper levels.
Sound Barrier System
Aerospace-grade polyurethane sound-absorbing foam combined with triple labyrinth seals attenuates noise transmission by 70%, complying with EU’s 85dB industrial noise mandate.
Spur Gear Slew Drive Cross-Industry Application Domination
In logistics automation, spur gear drives enable 500 RPM sorting robot turrets with ±0.1° positioning accuracy, boosting processing efficiency 200%. Food/pharmaceutical sterile filling platforms feature IP69K protection and 62dB quiet operation, cutting sanitation time by 40%. Stage equipment achieves 0.05° repeat accuracy in 3D lighting rigs, eliminating performance errors. Solar panel cleaning robots utilize 10-year maintenance-free designs, reducing O&M costs by 60%. Medical MRI tables achieve zero electromagnetic interference, enhancing image clarity by 30%.
Features of Spur Gear Slew Drive
Radical Compactness
15% shorter axial dimensions than helical gear drives, with flange mounting saving 50% space. Parker’s Ø200mm unit delivers 5kN·m torque.
Universal Power Interface
Accepts eight input methods including direct motor coupling, belt drives, and hydraulic motors, compatible with 90% of industrial power sources.
Intelligent Prognostics
Built-in vibration sensors and temperature chips predict gear wear 300 hours in advance, preventing million-dollar downtime.
Extreme Environment Conqueror
Withstands -40°C Arctic conditions using specialty low-temp greases, 80°C steel mills via ceramic thermal barriers, and coastal corrosion through 316L stainless steel housings certified by classification societies.
Nanoscale Precision Edition
Harmonic reducers combined with preloaded gears achieve ≤0.0005 radian backlash for semiconductor wafer handling.
Plug-and-Play Revolution
Pre-aligned mounting bases reduce integration time to 4 hours – 3x faster than conventional methods.
Spur Gear Slew Drive Price Factor Analysis
Core Cost Structure
Gear manufacturing constitutes 35% of total cost, with ISO6 precision gears commanding 50% premium over Grade 8. Slewing rings account for 30%, triple-contact designs costing 80% more than single-row. Heat treatment represents 15% (carburizing doubles quenching expenses). Sealing systems comprise 10% (multi-lip seals add 35%). Smart monitoring modules contribute 10% additional cost.
Procurement Anti-Fraud Guide
Material alert: Counterfeit products substitute 20CrMnTi alloy steel with 45# steel, reducing fatigue strength by 3x – demand carburization depth reports (≥0.8mm standard). Precision verification: Low-cost units falsify ISO ratings with 5x excess pitch errors – insist on third-party test reports. Bearing authentication: Non-standard bearings cause misalignment fractures – require INA/FAG certifications. Customization control: Special interfaces cost 200% more – economies begin at 30-unit batches.
Value Optimization Formula
(Torque Capacity ÷ Price) × Service Life ≥ 2.5
Case study: 5kN·m torque / $1,400 price / 20,000-hour life → (5÷1.4)×2=7.14 (exceeds benchmark)
Future Evolution: Intelligent Technology Leap
2025 heralds three revolutions: Digital twins achieve 99% failure prediction accuracy. Graphene composite gears reduce weight 40% while exceeding 3,000 RPM. Self-lubricating ceramic gears enable permanent maintenance-free operation. Under China’s Manufacturing 2025 strategy, domestic spur gear drives empower enterprises to build low-carbon competitive advantages at $0.02/kWh efficiency. Choosing high-speed silent solutions means commanding industrial leadership for the coming decade.
Supplier of Spur Gear Slew Drive
When your equipment faces extreme challenges and needs a powerful, precise "industrial joint," the double worm slew drive will be your reliable partner to break through bottlenecks and conquer the future. Explore its potential and unlock new heights of equipment performance.
Are you searching for the ultimate transmission solution to completely eliminate backlash and enhance load capacity and precision? Contact LYRADRIVE now for professional double worm slew drive selection advice and customized solutions!