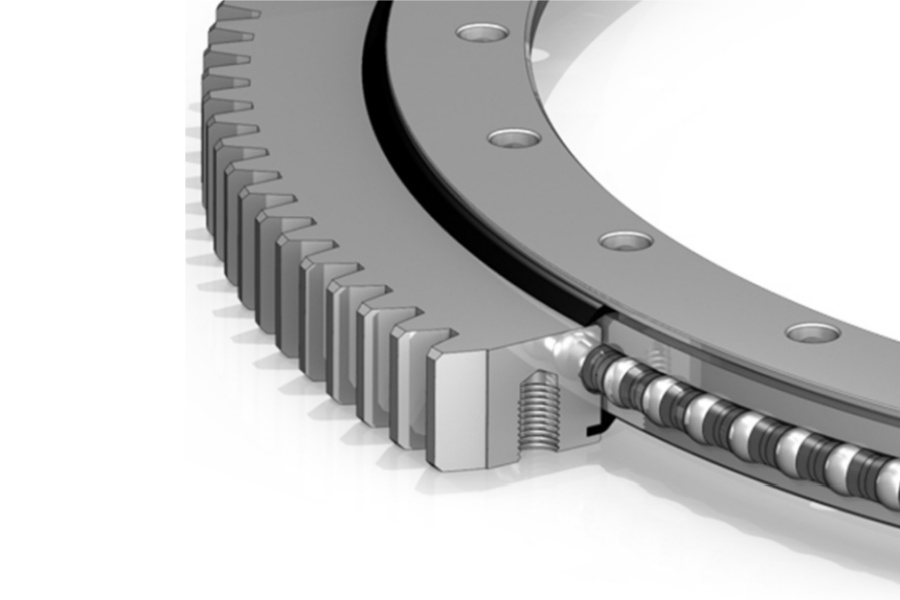
The Essential Powerhouse: Your Ultimate Guide to Single Row Slewing Ring Ball Bearings
What is Single Row Slewing Ring Ball Bearing?
A single row slewing ring ball bearing is a large-diameter, thin-section bearing specifically designed to handle combined loads (axial, radial, and tilting moments) while facilitating rotation between two structures, typically a stationary base and a rotating platform. Its defining characteristic is a single circular raceway containing a single complement of balls. These balls are usually spaced and guided by a sturdy cage or separator. The bearing consists of two rings – an inner ring and an outer ring – one of which typically features gear teeth (internal or external) integrated onto its circumference, allowing it to be driven by a pinion for controlled rotation. Seals are incorporated on both sides to protect the critical raceways and rolling elements from contamination and retain lubrication. Their relatively simple construction compared to multi-row bearings translates directly to advantages in compactness, weight savings, and cost-effectiveness.
The Mighty Minis: Small Slewing Ring Bearings
While slewing rings often conjure images of massive cranes, their smaller counterparts are equally vital and pervasive. Small slewing ring bearings adhere to the same fundamental single-row ball bearing principles but are optimized for applications with tighter space constraints and lower load requirements. They typically range from just a few inches to several feet in diameter. Their compactness makes them ideal for integration into robotics arms, medical imaging equipment (like CT scanner gantries), precision turntables, light-duty material handling equipment, surveillance cameras, solar tracker mechanisms, and even high-end consumer products like revolving restaurants or stages. Despite their size, small slewing rings must still be precision-engineered to deliver smooth motion, minimal friction, and adequate load capacity for their specific application. Material selection, heat treatment, and machining accuracy remain paramount to ensure performance and longevity, even in miniature form factors.
Silencing the Grind: Troubleshooting Slewing Ring Noise
Unexpected noise emanating from a slewing ring – grinding, clicking, rumbling, or squealing – is a clear warning sign demanding immediate attention. Diagnosing the source is critical for preventing catastrophic failure. Here are common culprits behind slewing ring noise:
Insufficient or Degraded Lubrication: The most frequent cause. Lack of grease leads to metal-to-metal contact, causing grinding or rumbling sounds. Contaminated grease (with dirt, water, or metal particles) acts as an abrasive. Solution: Follow the manufacturer's strict lubrication schedule using the specified grease type and quantity. Purge old grease effectively during relubrication.
Contamination Ingress: Dirt, dust, water, or abrasive particles breaching damaged or ineffective seals grind against raceways and balls, creating scratching or grinding noises. Solution: Inspect seals regularly for damage. Replace damaged seals immediately. Ensure the sealing system is appropriate for the operating environment (consider enhanced seals for harsh conditions).
Raceway or Ball Damage: Indentations (brinelling) from shock loads, spalling (fatigue pitting), or corrosion on the raceways or balls cause clicking, popping, or rumbling as the damaged areas pass under load. Solution: Requires bearing inspection. Minor damage might be monitored with increased lubrication vigilance, but significant damage usually necessitates bearing replacement.
Cage Failure: A damaged, cracked, or deformed cage can cause balls to skid, rub abnormally, or even jam, leading to clicking, scraping, or irregular rumbling sounds. Solution: Requires bearing disassembly and inspection. Cage damage typically mandates bearing repair or replacement.
Improper Mounting: Inaccurate mounting surfaces (lacking flatness or parallelism), insufficient or uneven bolt preload, or distortion during installation create internal stress points, leading to uneven loading and noise (often a groaning or rumbling). Solution: Strictly adhere to the manufacturer's mounting instructions regarding surface preparation, bolt tightening sequence, and torque values. Use precision mounting tools.
Misalignment: Significant misalignment between the inner and outer ring mounting surfaces forces the balls to run unevenly in the raceway, causing binding and groaning noises. Solution: Verify alignment during installation and periodically thereafter. Shimming may be required.
Loose Components: Loose mounting bolts or internal bearing components (though less common in sealed units) can cause rattling or knocking sounds. Solution: Check bolt torque according to specifications. Internal looseness usually indicates significant wear or damage requiring bearing attention.
Prompt diagnosis and corrective action based on the noise characteristics and operational history are essential for minimizing downtime and costly repairs.
The Slewing Ring Showdown: Single Row vs. Double Row
Choosing between single row and double row slewing bearings hinges on the specific demands of the application. Here's a detailed comparison:
Single Row Ball Bearings:
Structure: Single set of balls running in one raceway groove per ring.
Load Capacity: Good for moderate combined loads (axial, radial, moment). Higher load capacity than single-row 4-point contact for pure moment loads, but generally lower than double-row designs overall.
Compactness & Weight: Superior. Thinnest cross-section and lightest weight option.
Stiffness: Moderate stiffness under moment loads.
Cost: Generally the most economical slewing bearing type.
Friction & Power Consumption: Lower starting and running torque due to fewer balls and simpler geometry.
Ideal For: Applications where space and weight are premium, loads are moderate, and cost sensitivity is high (e.g., light cranes, smaller excavators, wind turbine pitch/yaw in some designs, material handling turntables, solar trackers, medical equipment, robotics).
Double Row Ball Bearings:
Structure: Two independent sets of balls running in two separate raceway grooves per ring. Requires significantly wider rings.
Load Capacity: Significantly higher capacity for all load types (axial, radial, moment) compared to single row ball bearings. Excellent for high moment loads.
Compactness & Weight: Larger cross-section and heavier than single row designs.
Stiffness: High stiffness, particularly under moment loads, due to the wider spaced ball rows acting as a larger moment arm.
Cost: Higher cost due to more complex manufacturing, increased material, and larger size.
Friction & Power Consumption: Higher starting and running torque compared to single row due to more balls and increased contact.
Ideal For: Applications demanding very high load capacity and stiffness, where space/weight constraints are less critical (e.g., heavy-duty cranes, large excavators, stacker-reclaimers, tunnel boring machines, offshore equipment, large radar platforms).
The choice is rarely just about peak load; factors like required stiffness, available envelope, weight budget, power availability, and cost play decisive roles. Single row ball bearings excel where efficiency, compactness, and value are paramount within their load range.
Unpacking the Advantages: Key Features of Single Row Slewing Ring Ball Bearings
The enduring popularity of single row ball slewing rings stems from a compelling set of inherent features:
Compact Design & Low Weight: Their single raceway configuration results in the slimmest possible cross-section among slewing bearing types. This minimizes the space required within the machine structure and significantly reduces overall system weight, crucial for mobile equipment and weight-sensitive applications.
Cost-Effectiveness: Simpler geometry with fewer components (one ball set, one cage) translates to lower manufacturing complexity and material costs compared to double-row or cross-roller designs. This makes them the most economical entry point into slewing bearing technology without sacrificing core functionality.
Low Friction & High Efficiency: The ball/raceway contact inherently generates lower starting and running torque than roller equivalents. Fewer rolling elements further reduce friction. This translates directly to lower power consumption for rotation, reduced heat generation, and potentially smaller drive motors and gearboxes.
High Rotational Speed Capability: Due to the lower friction and centrifugal forces acting on the balls (compared to rollers), single row ball bearings can generally achieve higher rotational speeds than roller-type slewing bearings, beneficial for applications like indexing tables or certain automation processes.
Smooth & Quiet Operation: When properly lubricated and maintained, the ball/raceway interaction provides exceptionally smooth and quiet rotation, essential for precision machinery, medical imaging, and noise-sensitive environments.
Moderate Load Capacity in All Directions: Competently handles combined axial, radial, and moment loads simultaneously, making them versatile for a wide range of applications where multi-directional forces are present, albeit within their defined capacity limits.
Integrated Gearing: Seamless incorporation of gear teeth (straight or helical) onto one ring (inner or outer) is standard, providing a direct and robust means of power transmission via a pinion for controlled slewing motion.
Integrated Sealing: Standard inclusion of effective sealing solutions (usually rubber or polyurethane) on both sides protects the internal components from environmental contaminants like dust, dirt, and moisture, while retaining vital lubricant.
Versatility: Available in a vast range of standard sizes and easily customizable (materials, seals, gear details, mounting holes, lubrication systems) to meet specific application requirements.
Where They Shine: Diverse Applications of Single Row Slewing Ring Ball Bearings
The unique blend of compactness, efficiency, and moderate load capacity makes single row ball slewing rings ubiquitous across numerous sectors:
Material Handling & Construction: Light and medium-duty crane jibs, excavator attachments (e.g., tiltrotators), manlift platforms, forklift rotators, conveyor turntables, palletizers, automated guided vehicles (AGVs).
Renewable Energy: Solar tracker systems (azimuth and elevation axes), smaller wind turbine pitch and yaw control systems (especially in earlier designs and smaller turbines).
Industrial Automation & Robotics: Robotic welding arms, assembly line positioners, indexing tables, packaging machinery turntables, palletizing/depalletizing robots.
Medical & Imaging Equipment: CT scanner gantries, MRI patient tables (rotation), radiation therapy linac rotators, surgical robot joints.
Defense & Aerospace: Radar and antenna positioning systems (smaller units), turret systems for light vehicles, missile launcher positioning, ground support equipment.
Agriculture: Combine harvester headers, sprayer booms, fertilizer spreader turntables.
Recreation & Infrastructure: Ferris wheels (car connections), revolving restaurant platforms, stage turntables, light-duty bridge inspection cams.
Mining & Process Industry: Light-duty stackers/reclaimers components, valve actuators, mixer bases.
Their ability to provide reliable rotation in constrained spaces while handling combined loads ensures their continued dominance in countless motion control systems.
Decoding the Price Tag: Factors Influencing Single Row Slewing Ring Cost
The cost of a single row slewing ring ball bearing is not a simple fixed number; it's influenced by a complex interplay of factors:
Bearing Size & Dimensions: Larger diameter bearings inherently require more raw material and involve more complex, time-consuming machining processes, significantly increasing cost. Ring thickness (cross-section height) also impacts material volume.
Material Specifications: Standard bearings typically use high-quality through-hardened alloy steel (like 42CrMo). However, bearings requiring enhanced toughness, corrosion resistance, or performance in extreme temperatures might use case-hardened steels (like 50Mn/42CrMo) or special alloys (like stainless steel), which are more expensive.
Heat Treatment Process: The specific heat treatment (through-hardening vs. case-hardening) and required depth/quality of hardness significantly impact cost. Case hardening is generally a more complex and expensive process than through-hardening.
Precision Grade: Standard slewing rings have defined tolerances (often ABEC 1 or similar). Applications demanding higher precision (e.g., medical imaging, high-speed automation) require tighter tolerances for raceway geometry, surface finish, and runout, demanding more meticulous manufacturing and inspection, thus increasing cost.
Gear Specifications: The presence, type (straight vs. helical), size (module), accuracy, and heat treatment of the integrated gear teeth add substantial cost. Helical gears are more complex to manufacture than straight-cut gears. High-precision or hardened gears cost significantly more.
Seal Type & Quality: Standard lip seals are common. Applications in harsh environments (dusty, wet, corrosive) may require advanced sealing solutions (multi-labyrinth, special elastomers, V-ring seals), which are more expensive. Redundant sealing adds cost.
Mounting Hole Configuration: Standard hole patterns are economical. Non-standard hole patterns, counterbores, tapped holes, or special flange designs require additional machining steps, increasing cost.
Lubrication System: While basic grease fittings are standard, bearings requiring centralized lubrication ports, internal grease channels, or specific fitting types will cost more.
Customization Level: Any deviation from standard catalog dimensions or features constitutes customization, driving up engineering, setup, and production costs. Prototypes are especially expensive.
Quantity: Economies of scale apply. Ordering larger quantities typically reduces the unit cost significantly compared to one-off or small-batch production.
Surface Treatments/Protection: Standard bearings often have a basic phosphate or oil coating. Special corrosion protection like zinc plating, painting, or specialized coatings add cost.
Supplier & Brand Reputation: Premium manufacturers with established reputations for quality, reliability, and engineering support often command higher prices than lesser-known or generic suppliers. Certifications (ISO, etc.) also factor in.
Raw Material Market Fluctuations: The cost of steel alloys is subject to global market dynamics, directly impacting bearing pricing.
Understanding these factors allows buyers to make informed decisions, balancing performance requirements with budget constraints.
Partnering for Performance: Sourcing Quality Single Row Slewing Rings
Selecting the right supplier for single row slewing ring ball bearings is as critical as selecting the bearing itself. A reliable partner ensures not just product delivery, but engineering support, quality assurance, and long-term reliability. Key considerations include:
Engineering Expertise: Look for suppliers with deep application knowledge who can assist with selection, load calculations, and integration advice, not just catalog sales.
Manufacturing Capability & Quality Control: Ensure the supplier has robust manufacturing processes, stringent quality control (including material certification, dimensional checks, non-destructive testing), and relevant certifications (ISO 9001).
Product Range & Customization: A broad standard range provides options, while strong customization capabilities (materials, seals, gears, mounting) are essential for non-standard applications.
Technical Support: Pre-sales consultation and post-sales troubleshooting support are invaluable. Responsive technical teams save time and prevent costly errors.
Reliability & Proven Track Record: Seek suppliers with a reputation for delivering durable, high-performance bearings backed by positive customer testimonials and industry presence.
Global Support & Logistics: For international operations or complex projects, consider the supplier's distribution network, lead times, and logistical efficiency.
Supplier of single row slewing ring ball bearings
For organizations seeking a trusted partner for high-performance single row slewing ring ball bearings, LYRADRIVE stands out as a premier solution provider. We go beyond simply supplying components; we deliver engineered motion solutions tailored to your specific challenges. Leveraging cutting-edge design software, precision manufacturing, and rigorous quality systems, LYRADRIVE bearings are built for durability, efficiency, and reliability in the most demanding environments. Our extensive standard range offers readily available solutions, while our dedicated engineering team excels at developing custom bearings to meet unique application requirements, whether it's extreme corrosion resistance, specialized sealing, non-standard gearing, or complex mounting configurations. We pride ourselves on providing exceptional technical support throughout the entire project lifecycle – from initial concept and selection assistance to installation guidance and ongoing maintenance optimization. Partnering with LYRADRIVE means gaining access to superior slewing technology, expert engineering collaboration, and a commitment to ensuring your rotational systems perform flawlessly, maximizing uptime and productivity. Contact LYRADRIVE today to discuss your application and experience the difference engineered quality makes.
Single row slewing ring ball bearings remain the cornerstone of efficient rotational motion across countless industries. Their optimal balance of compact design, cost-effectiveness, smooth operation, and reliable load handling ensures their continued dominance. Understanding their principles, capabilities, limitations, and the factors influencing their selection and cost empowers engineers to make optimal design choices. When performance and reliability are paramount, partnering with an experienced supplier like LYRADRIVE provides the engineering expertise and quality assurance needed to keep critical equipment rotating smoothly for the long haul.