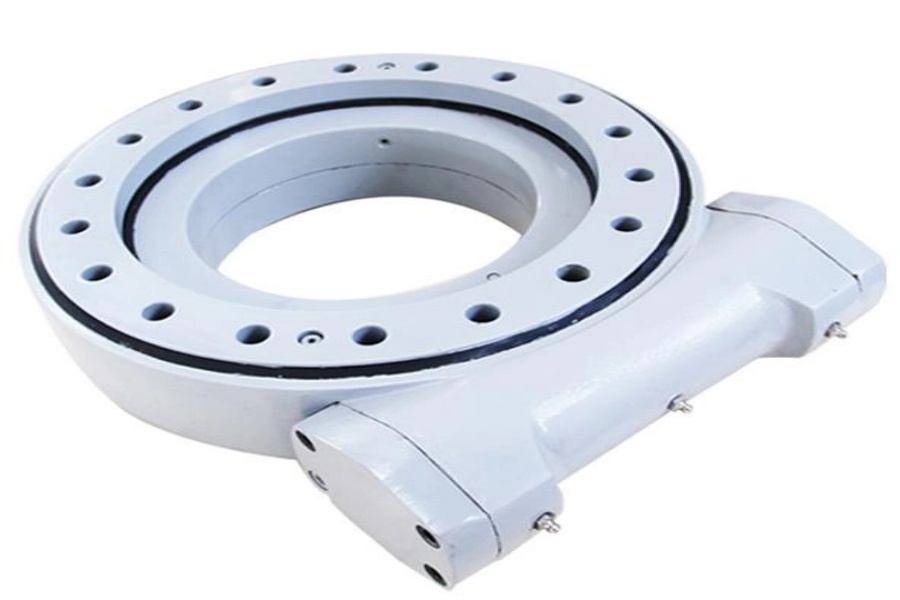
SE Slew Drives Powering Next-Generation Rotational Precision
In the rapidly advancing world of industrial automation and heavy equipment, SE Slew Drives have established themselves as pivotal components enabling precise rotational control across diverse applications. These sophisticated systems facilitate the movement of everything from solar arrays tracking the sun’s path to construction cranes hoisting massive loads, combining mechanical durability with intelligent operation. As industries increasingly demand efficiency, reliability, and adaptability, SE Slew Drives are emerging as critical solutions that bridge the gap between raw power and refined motion control in challenging operational environments.
What Is an SE Slew Drive
An SE Slew Drive is an integrated rotational mechanism that combines a high-performance slewing bearing with a precision gear system, engineered to deliver controlled 360-degree movement under substantial axial, radial, and moment loads. This system typically features a helical or planetary gear arrangement paired with a robust slewing ring, constructed from advanced alloys and composite materials treated for enhanced wear resistance and thermal stability. The design incorporates multi-layered sealing technologies to protect against environmental contaminants such as dust, moisture, and corrosive agents, alongside optimized lubrication channels that ensure consistent performance in both high-speed and high-torque scenarios.
The transformative impact of SE Slew Drives stems from their ability to harmonize power with precision. In renewable energy systems, these drives adjust wind turbine nacelles to optimal angles, maximizing energy capture while withstanding gale-force winds and saltwater exposure. For construction machinery, they enable tower cranes to position multi-ton building materials with millimeter accuracy, even in urban environments with spatial constraints. Their modular architecture allows customization for specific load capacities and rotational speeds, while integrated safety features like automatic braking systems prevent unintended movement during power disruptions, ensuring operational safety in critical applications such as offshore oil rigs or aerospace launch platforms.
Global Innovations in SE Slew Drive Technology
Technological Leadership in Established Markets
Countries with robust engineering ecosystems, including Germany, Japan, and the United States, continue to pioneer advancements in SE Slew Drive capabilities. German manufacturers employ laser-etched gear teeth with nanometer-level precision, reducing friction losses by 30% in high-speed industrial robots. Japanese engineers have developed asymmetric bearing raceways that redistribute stress concentrations during dynamic load shifts, extending component lifespan in mining excavators. American innovators utilize additive manufacturing to create lightweight, lattice-structured gears that maintain strength while reducing mass for aerospace applications.
The renewable energy sector benefits from SE Slew Drives equipped with self-healing polymer seals that repair minor abrasions caused by sandstorms in desert solar farms. The maritime industry leverages drives constructed from hydrophobic alloys that resist biofouling and corrosion in underwater robotic systems used for offshore maintenance. Robotics applications utilize variants with embedded strain sensors that provide real-time feedback on load distribution, enabling collaborative robots to handle fragile objects in automated assembly lines with unparalleled accuracy.
Emerging Markets Accelerating Technological Adoption
Manufacturers in industrializing regions are rapidly closing the technology gap through strategic investments in automation and digital tools. Chinese producers now implement AI-driven metallurgical analysis to optimize alloy compositions for local climate conditions, achieving performance parity with global competitors. Indian engineers have pioneered bio-inspired lubrication systems using plant-based oils that outperform traditional greases in high-temperature foundry applications. Brazilian firms employ blockchain-based supply chains to ensure material traceability for drives used in Amazonian hydroelectric projects, enhancing quality control.
Persistent challenges include mastering multi-axis load simulation and fatigue life prediction. European manufacturers utilize digital twin technology to simulate decade-long wear patterns in weeks, whereas emerging markets often depend on physical prototyping, extending development timelines. Limited access to ultra-high-vacuum steel treatment facilities in some regions affects the durability of drives used in extreme environments like Arctic mining operations.
Overcoming Technical Barriers in SE Slew Drive Applications
The divide between industry leaders and developing manufacturers centers on three pillars: material innovation, manufacturing accuracy, and smart system integration. Premium SE Slew Drives incorporate nanocomposite coatings that reduce surface wear by 50% in high-cycle packaging machinery, while cost-sensitive markets often use conventional coatings prone to rapid degradation in similar applications.
Collaborative initiatives are driving progress. Academic partnerships are developing 4D-printed shape-memory alloys that adapt to thermal expansion in desert solar trackers, maintaining gear alignment under temperature fluctuations. Another innovation involves edge AI processors embedded within drive housings, analyzing vibration data to predict bearing failures months in advance. Workforce development programs using augmented reality training modules have reduced installation errors by 45% in complex installations like bridge-building equipment.
The Future of SE Slew Drives Intelligence Meets Sustainability
Next-generation SE Slew Drives will prioritize energy regeneration, self-optimization, and eco-conscious design. Prototype kinetic energy recovery systems now in testing convert rotational inertia into stored power for onboard electronics, reducing external energy demands. Material scientists are experimenting with mycelium-based composites that offer 80% of steel’s strength while being fully biodegradable, addressing end-of-life environmental concerns.
In smart industrial networks, these drives will evolve into autonomous decision-makers. Imagine smart cities where SE Slew Drives in traffic management systems adjust surveillance camera angles based on real-time congestion data, optimizing traffic flow autonomously. Autonomous agricultural machinery could utilize drives with soil density sensors to automatically adapt tillage depth, improving crop yields while conserving energy.
Strategic Implementation Guidelines
Precision Installation Protocols:Utilize laser alignment systems to ensure gear meshing tolerances within 0.03mm during assembly, critical for achieving rated performance in precision medical imaging equipment.
Environment-Tailored Material Selection:Specify titanium nitride coatings for drives in coastal crane applications and graphite-embedded seals for high-temperature industrial furnaces.
Predictive Maintenance Systems:Implement acoustic monitoring networks that detect sub-surface cracks through ultrasonic wave analysis, enabling preemptive maintenance in wind turbine installations.
Circular Economy Integration:Design drives with modular components that allow individual gear replacement, minimizing waste during overhauls and supporting sustainability initiatives.
SE Slew Drives supplier
SE Slew Drives exemplify the fusion of mechanical excellence and technological innovation, driving progress across industries from renewable energy to advanced robotics. As global priorities shift toward sustainability and intelligent automation, these components are transitioning from passive mechanical parts to active, adaptive systems. While established markets continue to lead with breakthroughs in advanced materials and digital integration, emerging economies demonstrate that strategic investments in smart manufacturing and collaborative R&D can narrow technological gaps. The future promises SE Slew Drives that not only deliver unmatched performance but also contribute to a more efficient and sustainable industrial ecosystem. For industry leaders and engineers, embracing innovation while adhering to eco-conscious principles will be essential in shaping the next era of technological advancement.
LYRA Drive is a professional slewing bearings ,slew drive and gears manufacturer provides customized slew bearing, drive and gears.For application-specific engineering solutions, contact LYRA to discuss technical specifications and implementation strategies