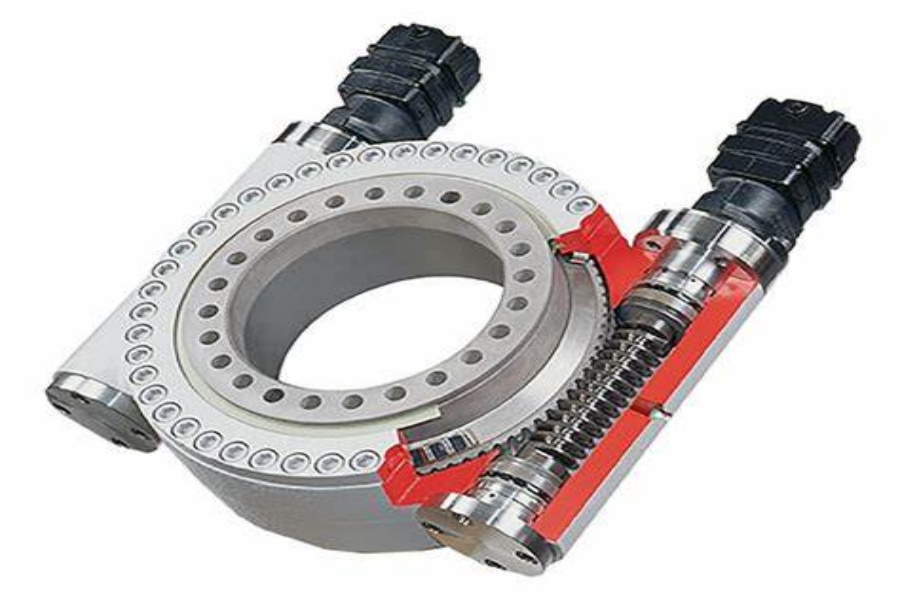
Redefining Precision with SP-l Slew Drive in Welding Positioners
In the competitive landscape of industrial welding, where milliseconds and microns separate profit from loss, welding positioners stand as critical enablers of efficiency. These systems expertly maneuver workpieces to expose seams for flawless welding, ensuring consistent quality and maximizing throughput. At the heart of these advanced machines lies the SP-l Slew Drive, a compact yet powerhouse rotational transmission unit that redefines how positioners tackle demanding movements. This article explores how the SP-l Slew Drive revolutionizes welding operations through its fusion of raw power, surgical precision, and adaptability across diverse industrial landscapes.
What is an SP-l Slew Drive?
The SP-l Slew Drive is a high-performance rotational mechanism engineered for precision motion control under extreme operational stresses. By integrating a heavy-duty slewing ring bearing with a multi-stage gear system—often employing harmonic or helical gears—this component excels in applications requiring smooth 360-degree rotation under monumental loads, such as shipyard gantries, mining excavators, or automated foundry systems. The "SP-l" designation typically identifies a specialized series renowned for innovations like adaptive thermal dissipation, intelligent load monitoring, or hybrid lubrication delivery. Unlike conventional slew drives, SP-l models frequently incorporate proprietary technologies such as noise-suppressed gear meshing or predictive maintenance sensors, establishing them as indispensable for industries where precision, durability, and operational continuity are paramount.
How SP-l Slew Drive Works in Welding Positioners
Envision a welding positioner as a tireless mechanical partner that rotates, angles, or flips massive components to optimize weld access. The SP-l Slew Drive acts as the operational core of this motion, synthesizing rotational force, precision control, and load management into a single integrated assembly. Constructed around a hardened slewing ring, the drive houses a motor, precision gear train, and mounting interfaces within a rugged, hermetically sealed enclosure. One ring anchors to the positioner’s stationary base, while the other connects to the rotating platform or tilting mechanism. When activated, the motor engages the gears to rotate the slewing ring with fluid precision, enabling exacting adjustments—whether delicately positioning a fragile semiconductor chassis or forcefully reorienting a 30-ton bridge segment mid-weld.
Key Features and Advantages of SP-l Slew Drive
The SP-l Slew Drive distinguishes itself through a marriage of modular sophistication and industrial resilience. Its pre-engineered architecture eliminates the need to source and integrate disparate components like reducers, motors, or encoders, slashing installation time and minimizing compatibility risks. A signature feature is its dynamic torque adaptation, which automatically modulates power output based on real-time load feedback—critical when welding irregularly shaped components like turbine blades or asymmetrical pressure vessels prone to sudden weight shifts.
The drive’s inherent positional locking, inherent in its harmonic gear design, guarantees loads remain immovably fixed once positioned. This proves indispensable when welding overhead or on vertical surfaces, where gravitational pull or vibration could otherwise induce hazardous movement. Unlike electromechanical systems vulnerable to signal lag, the SP-l Slew Drive maintains unwavering stability even during abrupt power fluctuations or emergency stops.
Space optimization emerges as another hallmark. By embedding the drive mechanism within the slewing ring’s profile, the SP-l Slew Drive compresses the positioner’s footprint without sacrificing capability—a transformative advantage for mobile welding units or congested production floors. Its variable load capacity empowers it to handle everything from delicate aerospace brackets to monstrous refinery components with equal finesse. Maintenance is streamlined through innovations like self-cleaning seal labyrinths and diamond-like carbon coatings that repel wear in abrasive environments like quarry equipment repair or cement plant maintenance.
Applications of SP-l Slew Drive in Welding Positioners
The SP-l Slew Drive dominates in two core functions within welding positioners: continuous rotation and multi-axis manipulation.
In rotational systems, the drive orchestrates seamless 360-degree movement of the worktable. For instance, when welding spherical nuclear reactor vessels, the SP-l Slew Drive enables variable-speed rotation, allowing welders to maintain arc consistency without interrupting workflow. This capability proves invaluable in robotic welding cells, where automated torches demand flawless, repeatable motion to deposit uniform seams across marathon production runs. Even at glacial speeds required for welding ultra-thin titanium sheets or brittle glass-metal hybrids, the drive’s motion remains imperceptibly smooth, eliminating defects like porosity or thermal distortion.
For multi-axis manipulation, the SP-l Slew Drive’s rugged precision takes command. Imagine a gamma-shaped positioner designed for locomotive undercarriages: the drive’s helical gear system allows one arm to pivot chassis components 180 degrees while a secondary axis fine-tunes their lateral orientation. This multi-plane agility lets welders attack horizontal, vertical, and inverted seams in a single fixturing. In renewable energy projects, where wind turbine nacelles demand circumferential welds, the drive’s ability to “park” at programmed angles ensures optimal torch positioning, slashing rework and turbocharging project velocity.
How SP-l Slew Drive Elevates Welding Positioner Performance
Integrating the SP-l Slew Drive unlocks quantum leaps across key performance indicators:
Sub-Micron Precision and Repeatability
Outfitted with anti-backlash gears and laser-etched encoders, the drive achieves positional accuracy measured in micrometers. In medical implant manufacturing, where welding microscopic titanium joints demands perfection, this precision prevents tissue-irritating imperfections. Repeatability—replicating positions across billions of cycles—is equally vital for consumer electronics, where microscopic welds define product longevity. The SP-l Slew Drive delivers metronomic consistency, even after lifetimes of relentless operation.
Titanic Load Management
Forged from maraging steel and fitted with four-point contact bearings, the drive shrugs off eccentric loads that would destroy conventional systems. In heavy machinery rebuilds, positioners must rotate colossal, unbalanced components like dragline buckets. The SP-l Slew Drive’s unflinching rigidity maintains alignment under extreme stress, preventing premature wear and stretching maintenance intervals.
Lightning-Fast Cycle Times
By enabling instantaneous transitions between weld positions, the drive vaporizes non-productive intervals. Consider petrochemical pipeline fabrication: positioners equipped with SP-l Slew Drives can rotate 50-foot pipe spools between passes in under 20 seconds, hacking total weld time by 40%. Configurable acceleration curves let operators tailor motion dynamics—leisurely for heat-sensitive bimetallic joints, aggressive for rugged manganese steel crushers.
Armored Reliability
The drive’s quad-seal barriers and vapor-deposited ceramic coatings defy welding spatter, grinding debris, and caustic coolants. In aluminum smelters, where positioners endure molten metal splatter and caustic fumes, this fortress-like protection ensures flawless performance amid infernal conditions.
Common Pitfalls to Avoid When Using SP-l Slew Drives
Even battle-hardened components demand disciplined handling:
Overstepping Dynamic Load Limits: Assuming static load ratings apply to rotating loads invites bearing brinelling. Always reference dynamic load charts for moving applications.
Neglecting Lubricant Compatibility: Using EP grease in high-speed applications risks thermal breakdown. Match lubricant types to operational RPM and temperature ranges.
Bypassing Vibration Monitoring: Unchecked harmonics from imbalanced loads can fracture mounting bolts. Implement wireless vibration sensors for real-time health checks.
Ignoring Contamination Protocols: While built to resist grime, allowing metal shavings to accumulate on seal surfaces invites premature failure. Institute routine blowdown procedures.
SP-l Slew Drive supplier
LYRA Drive is a professional slewing bearings ,slew drive and gears manufacturer provides customized slew bearing, drive and gears.For application-specific engineering solutions, contact LYRA to discuss technical specifications and implementation strategies.