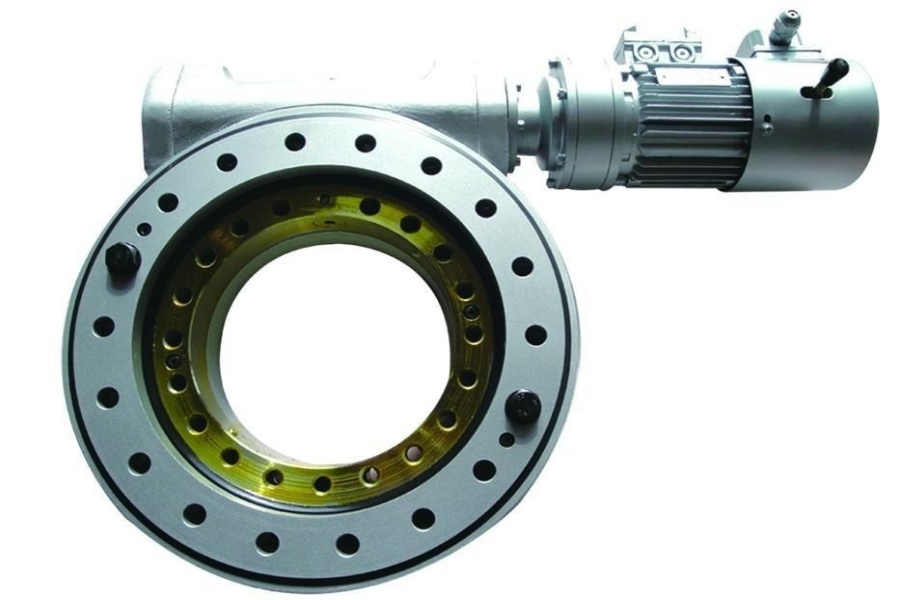
Redefining Heavy-Duty Welding with the SP-H Slew Drive
In the relentless world of industrial welding, where precision meets brute strength, welding positioners have emerged as critical tools for manipulating massive workpieces with pinpoint accuracy. These systems ensure seams are perfectly positioned, guaranteeing flawless welds and maximizing productivity. At the core of these rugged machines lies the SP-H Slew Drive, a powerhouse rotational transmission unit that reimagines how positioners tackle the most demanding welding tasks. This article dives into how the SP-H Slew Drive transforms welding operations through its unmatched durability, precision, and adaptability in extreme environments.
What is an SP-H Slew Drive?
The SP-H Slew Drive is a heavy-duty rotational mechanism engineered to deliver precise, controlled motion under the most punishing conditions. By integrating a reinforced slewing ring bearing with a multi-stage gear system—often utilizing planetary or hypoid gears—this component thrives in applications requiring seamless 360-degree rotation under colossal loads, such as mining excavators, offshore oil rigs, or industrial forging presses. The "SP-H" designation typically identifies a specialized series renowned for innovations like extreme-load adaptability, shock-resistant gearing, or smart thermal management. Unlike conventional slew drives, SP-H models incorporate proprietary technologies such as impact-dampening gear teeth or predictive wear sensors, making them indispensable for industries where downtime is not an option and precision cannot be compromised.
How the SP-H Slew Drive Works in Welding Positioners
Picture a welding positioner as a mechanical titan that rotates, tilts, or flips multi-ton components to expose seams for welding. The SP-H Slew Drive serves as the operational heart of this motion, merging raw rotational force, micro-level control, and load stabilization into a single rugged assembly. Built around a hardened slewing ring, the drive encapsulates a high-torque motor, multi-stage gear reducer, and reinforced mounting flanges within a compact, hermetically sealed housing. One ring bolts to the positioner’s stationary base, while the other connects to the rotating platform or tilting arm. When activated, the motor drives the gears to rotate the slewing ring with unerring smoothness, enabling precise adjustments—whether delicately aligning a nuclear reactor component or violently repositioning a 50-ton construction crane boom mid-weld.
Key Features and Advantages of the SP-H Slew Drive
The SP-H Slew Drive distinguishes itself through a blend of industrial fortitude and adaptive intelligence. Its pre-engineered, modular design eradicates the need to source and assemble disparate components like gearboxes or bearings, slashing installation time and eliminating alignment headaches. A standout feature is its adaptive load balancing, which automatically redistributes torque based on real-time weight shifts—critical when welding asymmetrical behemoths like wind turbine hubs or unevenly weighted ship propellers.
The drive’s fail-safe self-locking mechanism, inherent in its hypoid gear geometry, ensures loads remain rock-steady once positioned. This is vital when welding on vertical cliffs of steel or inverted surfaces, where gravitational pull or vibration could spell disaster. Unlike chain-driven systems prone to slippage, the SP-H maintains unshakable stability even during power failures or abrupt emergency stops.
Space efficiency is another hallmark. By nesting the drive within the slewing ring’s profile, the SP-H trims the positioner’s footprint without sacrificing muscle—a game-changer for mobile repair rigs or cramped fabrication bays. Its asymmetric load rating allows it to juggle featherweight aerospace brackets and gargantuan pressure vessels with equal finesse. Maintenance is streamlined through self-cleaning seal labyrinths and tungsten-carbide coatings that laugh off abrasion in environments like quarry conveyor repairs or cement mixer overhauls.
Applications of the SP-H Slew Drive in Welding Positioners
The SP-H Slew Drive dominates in two critical roles within welding positioners: high-stakes rotation and extreme-angle positioning.
In rotational systems, the drive powers the relentless 360-degree movement of the worktable. For instance, when welding spherical LNG storage tanks, the SP-H enables variable-speed rotation, letting welders maintain arc consistency without breaking stride. This proves invaluable in automated cells, where robotic welders demand flawless, repeatable motion to lay down mile-long seams on oil pipelines. Even at snail-paced speeds required for welding brittle titanium-aluminum hybrids, the drive’s motion remains tremor-free, preventing defects like hot cracking or porosity.
For extreme-angle positioning, the SP-H’s brute strength and precision shine. Imagine a gamma-shaped positioner designed for locomotive underframes: the drive’s planetary gear system allows one arm to tilt a 30-ton chassis 120 degrees while a secondary axis fine-tunes its roll angle. This multi-plane agility lets welders attack horizontal, vertical, and inverted seams in a single clamping. In offshore wind farm construction, where turbine nacelles demand overhead welds, the drive’s ability to “freeze” at exact angles ensures optimal torch access, slashing rework and beating project deadlines.
How the SP-H Slew Drive Elevates Welding Positioner Performance
Integrating the SP-H Slew Drive unlocks transformative gains across every performance metric:
Sub-Millimeter Precision and Military-Grade Repeatability
Armed with anti-backlash gears and laser-calibrated encoders, the drive achieves positional accuracy rivaling CNC machines. In aerospace manufacturing, where turbine disk welds demand perfection, this precision prevents imbalance-induced failures. Repeatability—hitting the same coordinates across 10,000 cycles—is equally vital for automotive chassis production, where consistency ensures crash-test integrity. The SP-H delivers robotic repeatability, even after decades of abuse.
Herculean Load Capacity
Forged from maraging steel and fitted with four-point contact bearings, the drive shrugs off off-center loads that would snap lesser systems. In mining shovel rebuilds, positioners must rotate 40-ton dipper arms riddled with uneven wear. The SP-H’s unyielding rigidity maintains alignment under torture, preventing gear tooth spalling and stretching service intervals.
Blitzkrieg Speed and Adaptability
By enabling warp-speed transitions between weld positions, the drive annihilates downtime. Take shipyard operations: positioners equipped with SP-H Slew Drives can rotate hull sections between passes in under a minute, hacking total project time by 40%. Custom acceleration profiles let operators match motion to material needs—gentle for crack-prone cast iron, aggressive for armor-grade steel.
Apocalypse-Ready Reliability
The drive’s triple-redundant seals and plasma-arc-sprayed coatings repel welding spatter, grinding grit, and salt spray. In aluminum smelters, where positioners endure molten metal rain and caustic fumes, this armor ensures flawless performance in hellish conditions.
Common Pitfalls to Avoid When Using SP-H Slew Drives
Even indestructible gear demands respect:
Ignoring Dynamic Load Limits: Assuming static ratings apply to rotating loads invites bearing collapse. Always consult dynamic load charts for moving masses.
Mixing Grease Types: Dumping incompatible lubricants into gears creates sludge. Stick to manufacturer-specified high-pressure greases.
Skipping Vibration Checks: Unbalanced loads can shake mounts loose. Deploy wireless vibration sensors for real-time health monitoring.
Disregarding Contamination: While built to eat dirt, letting metal shavings cake on seals invites premature failure. Institute daily blowdown routines.
SP-H Slew Drive supplier
LYRA Drive is a professional slewing bearings ,slew drive and gears manufacturer provides customized slew bearing, drive and gears.For application-specific engineering solutions, contact LYRA to discuss technical specifications and implementation strategies.