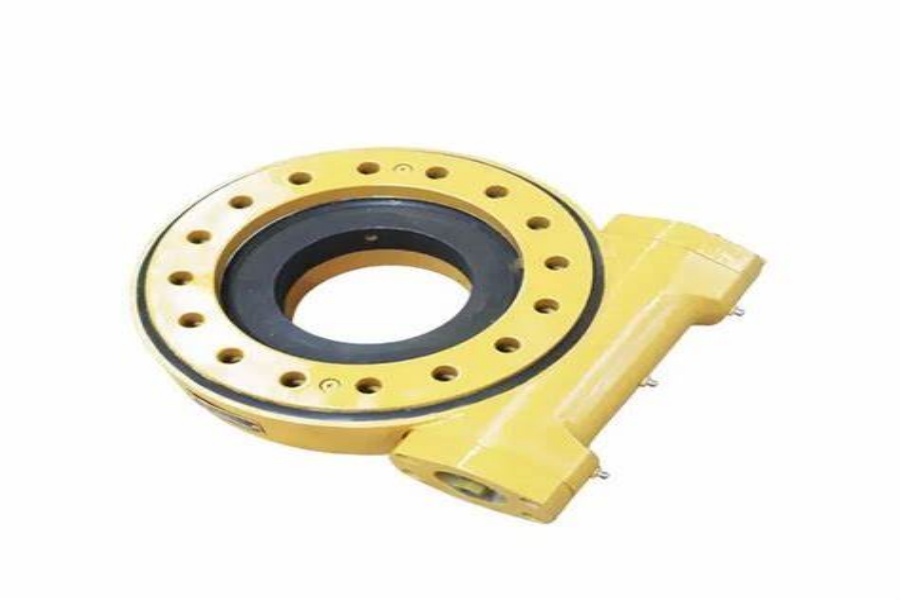
Revolutionizing Welding Precision with the SP-M Slew Drive
In the fast-evolving world of industrial welding, where precision and speed define operational success, welding positioners have become indispensable tools for positioning workpieces with unmatched accuracy. These systems ensure seams are optimally accessible, guaranteeing consistent weld quality and maximizing productivity. Central to their performance is the SP-M Slew Drive, a robust yet refined rotational transmission component that redefines how positioners manage complex movements. This article explores how the SP-M Slew Drive elevates welding operations through its innovative engineering, reliability, and adaptability across diverse industrial applications.
What is an SP-M Slew Drive?
The SP-M Slew Drive is a high-performance rotational mechanism designed to deliver precise, controlled motion in extreme working conditions. By integrating a heavy-duty slewing ring bearing with a multi-stage gear system—typically employing planetary or cycloidal gears—this component excels in applications requiring seamless 360-degree rotation under immense loads, such as construction cranes, solar tracking arrays, or automated assembly lines. The "SP-M" designation often signifies a specialized series known for advancements like adaptive load distribution, enhanced thermal resistance, or intelligent lubrication systems. Unlike standard slew drives, SP-M models incorporate proprietary technologies such as vibration-dampening gear profiles or real-time diagnostic sensors, making them essential for industries where uptime, precision, and safety are critical.
How the SP-M Slew Drive Works in Welding Positioners
Imagine a welding positioner as a dynamic assistant that rotates, tilts, or flips heavy components to expose seams for optimal welding access. The SP-M Slew Drive serves as the mechanical backbone of this motion, merging rotational power, precision control, and load management into a single integrated unit. Built around a hardened slewing ring, the drive houses a motor, multi-stage gearbox, and mounting interfaces within a compact, sealed enclosure. One ring attaches to the positioner’s stationary base, while the other connects to the rotating platform or tilting arm. When activated, the motor drives the gears to rotate the slewing ring smoothly, enabling precise adjustments—whether aligning a delicate aerospace component with micron-level accuracy or repositioning a multi-ton ship hull segment mid-weld.
Key Features and Advantages of the SP-M Slew Drive
The SP-M Slew Drive stands out through a combination of modular versatility and industrial-grade durability. Its pre-assembled design eliminates the need to source and align separate components such as motors, reducers, or bearings, drastically reducing installation time and potential errors. A defining feature is its adaptive torque control, which dynamically adjusts power output based on real-time load conditions—crucial for welding irregularly shaped or unbalanced workpieces prone to sudden shifts.
The drive’s self-locking mechanism, inherent in its cycloidal gear design, ensures loads remain securely fixed once positioned. This is vital when welding on vertical or overhead surfaces, where gravitational forces could otherwise cause hazardous movement. Unlike hydraulic systems susceptible to leaks, the SP-M Slew Drive maintains positional stability even during power interruptions or emergency shutdowns.
Space efficiency is another standout trait. By embedding the drive within the slewing ring’s structure, the SP-M minimizes the positioner’s footprint without sacrificing power—a critical advantage for mobile welding units or facilities with limited floor space. Its high dynamic load capacity allows it to handle both lightweight precision instruments and massive structural components with ease. Maintenance is simplified through features like self-lubricating bushings and corrosion-resistant coatings that thrive in harsh environments such as offshore platforms or chemical plants.
Applications of the SP-M Slew Drive in Welding Positioners
The SP-M Slew Drive excels in two primary roles within welding positioners: continuous rotation and multi-axis positioning.
In rotational systems, the drive powers the seamless 360-degree movement of the worktable. For example, when welding cylindrical storage tanks, the SP-M enables variable-speed rotation, allowing welders to maintain a steady arc without stopping to reposition. This capability is invaluable in automated welding cells, where robotic arms depend on flawless, repeatable motion to deposit uniform seams across high-volume production runs. Even at ultra-low speeds required for welding thin aluminum sheets or brittle composites, the drive’s motion remains smooth, preventing defects like warping or incomplete fusion.
For multi-axis positioning, the SP-M’s rugged construction and precision take center stage. Consider a T-shaped positioner designed for railway bogies: the drive’s planetary gear system allows one arm to tilt the bogie 90 degrees while a secondary axis adjusts its lateral angle. This multi-directional flexibility lets welders tackle horizontal, vertical, and overhead seams in a single setup. In wind turbine manufacturing, where tower sections require circumferential welds, the drive’s ability to lock positions at precise angles ensures optimal torch access, reducing rework and accelerating production timelines.
How the SP-M Slew Drive Enhances Welding Positioner Performance
Integrating the SP-M Slew Drive delivers measurable improvements across key performance metrics:
Micron-Level Precision and Consistency
Equipped with zero-backlash gears and high-resolution encoders, the drive achieves positional accuracy measured in micrometers. In semiconductor manufacturing, where welding microscopic connectors demands perfection, this precision prevents electrical failures. Repeatability—replicating positions across thousands of cycles—is equally vital for automotive assembly lines, where consistency ensures part interchangeability. The SP-M delivers unwavering repeatability, even after years of continuous use.
Exceptional Load Handling
Constructed from hardened alloy steel and fitted with tapered roller bearings, the drive withstands off-center loads without flexing. In mining equipment repair, positioners must rotate colossal, unevenly weighted crusher components. The SP-M’s rigidity maintains alignment under stress, preventing premature wear and extending service life.
Rapid Cycle Times
By enabling swift transitions between weld positions, the drive slashes non-productive downtime. For instance, in agricultural machinery production, positioners equipped with SP-M Slew Drives can flip tractor buckets between passes in seconds, reducing total assembly time by 25%. Adjustable speed settings allow operators to tailor rotation rates—slower for heat-sensitive titanium, faster for rugged steel castings.
Unmatched Reliability
The drive’s multi-layered seals and hardened surface coatings resist welding spatter, abrasive dust, and humidity. In steel mills, where positioners endure extreme heat and particulate exposure, this protection ensures reliable performance in punishing conditions.
Common Pitfalls to Avoid When Using SP-M Slew Drives
Even rugged components require mindful operation:
Exceeding Load Limits: Overloading the drive beyond its rated capacity risks gear damage. Always verify load charts for dynamic and static conditions.
Using Incompatible Lubricants: Substituting incorrect greases can degrade performance. Follow manufacturer guidelines for lubricant type and intervals.
Poor Installation Alignment: Misaligned mounts strain components. Use laser alignment tools during setup to ensure perfect coaxiality.
Ignoring Environmental Hazards: While built for toughness, prolonged exposure to corrosive chemicals without protective measures can compromise seals.
SP-M Slew Drive supplier
LYRA Drive is a professional slewing bearings ,slew drive and gears manufacturer provides customized slew bearing, drive and gears.For application-specific engineering solutions, contact LYRA to discuss technical specifications and implementation strategies.