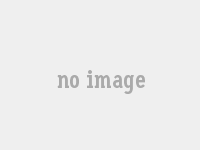
How to Choose the Safety Factor for Slewing Drives Under Different Working Conditions?
What is a Slewing Drive?
A slewing drive(slew drive) is a versatile mechanical device designed to manage rotational motion while simultaneously supporting axial, radial, and tilting moment loads. It combines a slewing ring bearing and a drive mechanism into a single unit, providing efficient, reliable rotational capabilities. Slewing drives are widely used in various industries, including renewable energy, construction, transportation, and robotics.
In the design and manufacture of slewing drives by Lyra Drive, selecting the appropriate safety factor for gear torque transmission under various working conditions is a complex yet critical aspect of design. The safety factor directly impacts the reliability and durability of the gear transmission system. Drawing from years of design and manufacturing experience, Lyra Drive engineers have summarized the following guidelines for determining safety factors under different conditions:
Normal Working Conditions in Gear Transmission
In normal operation, the gear transmission system typically experiences three main conditions: starting, constant speed, and braking. Each of these has unique requirements for safety factor selection.
1. Starting Conditions
During startup, the motor generates its maximum torque, causing the gear system to experience significant impact loads. This makes startup one of the most demanding phases for gear systems.
Recommended Safety Factor:
A higher safety factor of 1.25 to 1.50 is recommended.
This ensures the gears can withstand the sudden surge in torque during startup without overloading, thereby preventing damage.Considerations:
The type of motor and its startup characteristics.
The frequency of startups in the system’s operational cycle.
Whether additional measures, such as soft-start mechanisms, are employed.
2. Constant Speed Conditions
When operating at constant speed, the load on the gear system is relatively stable. However, long-term wear and fatigue must still be accounted for to ensure the system's reliability over its intended service life.
Recommended Safety Factor:
A moderate safety factor of 1.0 to 1.25 is suitable.
The exact value depends on the design's desired longevity and reliability requirements.Considerations:
The duration and intensity of continuous operation.
The material and fatigue resistance of the gear.
The operating environment, including temperature and contamination levels.
3. Braking Conditions
Braking introduces significant impact loads on the gear system, often comparable to or slightly lower than startup conditions. Additionally, abnormal scenarios like motor short-circuits or emergency stops can exert extreme loads on the system.
Recommended Safety Factor:
The highest safety factor is necessary, typically ranging from 1.5 to 2.0 or higher.
This ensures that the gear system remains safe and reliable even under extreme braking scenarios.Considerations:
The nature and frequency of braking events.
The potential for extreme braking forces in emergency situations.
Adequacy of braking system design to minimize sudden loads.
Factors Affecting Safety Factor Selection
Several factors influence the selection of safety factors in slewing drives. These factors can help optimize safety margins while ensuring cost-effectiveness and efficiency.
1. Material Strength
The stronger the material, the higher the load-bearing capacity of the gears. Using high-strength materials allows the safety factor to be reduced without compromising reliability.
Examples:
Heat-treated steel for enhanced wear resistance.
Advanced alloys with high tensile strength.
Impact:
Higher material strength reduces the risk of fatigue and deformation, enabling a lower safety factor while maintaining system integrity.
2. Manufacturing Precision
Higher manufacturing precision improves gear meshing accuracy, reducing wear and fatigue damage during operation.
Key Aspects:
Precision grinding and finishing of gear teeth.
Ensuring tight tolerances during manufacturing.
Impact:
Enhanced precision minimizes the likelihood of misalignment and uneven load distribution, allowing for a reduction in the safety factor.
3. Lubrication Quality
Effective lubrication significantly reduces gear friction and wear, improves transmission efficiency, and extends service life.
Recommended Practices:
Use high-quality lubricants suited for specific operating conditions.
Ensure proper lubrication intervals and maintenance schedules.
Impact:
Good lubrication conditions allow for a lower safety factor by reducing operational stresses on the gear system.
4. Design Life and Reliability Requirements
For applications requiring long design life or higher reliability, a higher safety factor should be chosen to ensure consistent performance over time.
Examples:
Systems with critical safety roles, such as cranes or wind turbines.
Applications with minimal maintenance access or extreme environmental conditions.
Impact:
Higher safety factors in these scenarios provide a buffer against unforeseen loads or prolonged wear, enhancing overall reliability.
5. Maintenance and Inspection
Regular maintenance and inspection of the gear system are essential to extend its service life and ensure safe operation.
Best Practices:
Periodic checks for wear, misalignment, and lubrication levels.
Replacement of worn components before they fail.
Impact:
A well-maintained system can operate safely with a lower safety factor, as potential issues are addressed proactively.
Conclusion
Selecting the appropriate safety factor for slewing drives under different working conditions is a nuanced process that balances reliability, cost, and operational efficiency. Startup, constant speed, and braking conditions each require tailored safety factors based on the unique stresses they impose on the gear system. Additionally, factors such as material strength, manufacturing precision, lubrication quality, design life, and maintenance practices play critical roles in optimizing safety factor selection.
By adhering to these principles, designers and manufacturers like Lyra Drive ensure that slewing drives deliver consistent, safe, and durable performance across diverse applications.