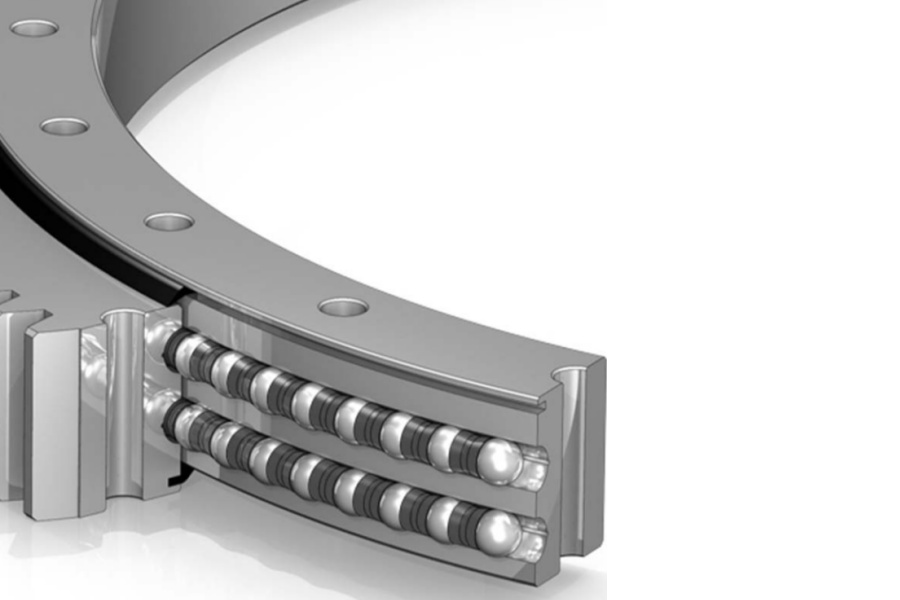
Heavy Load Slewing Bearings: The Unseen Giants Powering Industry's Mightiest Moves
What is a Heavy Load Slewing Bearing? The Backbone of Rotation Under Extreme Stress
A heavy load slewing bearing is a specialized type of large-diameter bearing explicitly designed to handle simultaneously massive axial loads (vertical forces), radial loads (horizontal forces), and significant tilting moments (forces trying to tip the structure over). Think of it as the industrial-strength turntable for giants. Unlike smaller bearings, these behemoths are characterized by:
Enormous Size and Capacity: Diameters can range from one meter to over ten meters, with load capacities reaching thousands of tonnes. They are built to withstand forces that would obliterate conventional bearings.
Integrated Functionality: Often incorporating gear teeth (internal or external) directly onto the bearing races, along with robust sealing systems and lubrication channels, creating a compact, multi-functional assembly.
Precision Under Pressure: Engineered to provide smooth, controlled rotation with minimal friction and high positional accuracy, even when supporting colossal weights and resisting massive overturning forces.
Extreme Durability: Manufactured from high-grade alloy steels and subjected to advanced heat treatments (like deep carburizing or induction hardening), they offer exceptional resistance to wear, fatigue, and impact over decades of demanding service.
High Customization: Virtually every heavy-duty slewing bearing is a custom-engineered solution, tailored to the specific load profiles, space constraints, environmental conditions, and performance requirements of the host machine.
At their core, they consist of an inner ring, an outer ring, rolling elements (balls or rollers), and a cage or spacer system. The raceways are precision-ground and hardened to provide the ultimate wear surface.
Mining Excavator Swing Bearing Replacement: A Critical Operation Demanding Expertise
The swing bearing is the literal pivot point of a giant mining excavator or shovel. It sits between the machine’s upper structure (house) and the undercarriage, enabling 360-degree rotation while supporting the immense weight of the house, boom, stick, bucket, and the dynamic loads generated during digging and swinging.
Replacing a mining excavator swing bearing is a major, high-stakes undertaking:
Costly Downtime: Excavators are productivity powerhouses. Every hour offline represents significant lost revenue. Replacement projects can take days or even weeks.
Sheer Scale and Weight: These bearings are incredibly large and heavy, often requiring specialized heavy-lift cranes and transport equipment just to handle them.
Complex Disassembly/Reassembly: Gaining access to the bearing involves significant disassembly of the excavator's upper works. Precise alignment during reassembly is critical to ensure smooth operation and prevent premature failure.
Technical Precision: Installation demands meticulous attention to detail – surface preparation, bolt pre-tensioning to exact specifications, proper alignment of gear teeth, and correct lubrication. Errors can lead to catastrophic failure.
Safety Paramount: The process involves heavy lifting, working at heights, and complex procedures in often challenging environments, requiring rigorous safety protocols and highly trained personnel.
Choosing a high-quality replacement bearing and partnering with experienced service providers is non-negotiable for minimizing downtime and ensuring the excavator's long-term operational reliability.
Heavy Load Slewing Bearing Manufacturers: Masters of Metal and Precision
Designing and manufacturing these colossal, mission-critical components is a domain reserved for specialized industrial powerhouses. Leading heavy load slewing bearing manufacturers distinguish themselves through:
Advanced Engineering Capabilities: Expertise in finite element analysis (FEA) to simulate complex load scenarios and optimize designs for maximum strength and longevity.
State-of-the-Art Manufacturing: Possessing massive CNC machining centers, sophisticated heat treatment facilities (like large carburizing furnaces and press quenching lines), and precision grinding equipment capable of handling giant components with micron-level accuracy.
Material Science Prowess: Deep knowledge of metallurgy and access to high-purity, high-strength alloy steels essential for extreme durability.
Rigorous Quality Control: Implementing stringent testing protocols throughout production, including non-destructive testing (NDT), dimensional inspection, and load testing, often backed by international certifications (ISO, DNV-GL, ABS, etc.).
Global Support & Customization: Offering comprehensive technical support, custom design services, and often global logistics for delivery and sometimes installation support. Reputable names include Thyssenkrupp Rothe Erde, Schaeffler (INA/FAG), The Timken Company, SKF, and leading specialized manufacturers like ZWZ, Luoyang Xinqianglian Slewing Bearing Co., Ltd (XQL), and Kaydon (acquired by SKF).
Proven Track Record: Demonstrated success in supplying bearings for the most demanding applications worldwide.
Selecting the right manufacturer is crucial, balancing technical capability, quality, reliability, lead times, and cost-effectiveness for the specific application.
Port Crane Slewing Ring: Where Precision Meets Unrelenting Power
At the heart of every modern container crane – be it a Ship-to-Shore (STS) gantry crane reaching across a vessel or a Rubber-Tyred Gantry (RTG) crane stacking containers in the yard – lies a massive slewing ring bearing. This bearing is fundamental to the crane's operation:
Supporting the Superstructure: It carries the entire weight of the crane's rotating upper structure, including the boom, trolley, hoist machinery, operator's cab, and the lifted container itself.
Enabling Rotation: It allows the crane to slew smoothly and precisely, positioning the spreader accurately over containers on a ship or stacks in the yard.
Resisting Dynamic Forces: It withstands not just static weight but also dynamic loads from lifting, lowering, trolley travel, wind loads, and even ship impact during berthing.
Handling Massive Moments: The long boom creates significant overturning moments, which the bearing's design must effectively transfer into the crane's portal frame or undercarriage.
Demanding Environment: Exposure to salt spray, dust, vibration, and continuous operation requires exceptional sealing and corrosion resistance.
Port crane slewing rings are typically engineered as single or double row ball bearings (like four-point contact designs) for high load capacity and smooth rotation, or crossed roller bearings for compactness and high moment capacity. Reliability is paramount, as crane downtime bottlenecks port operations globally.
The Vast Realm of Heavy Load Slewing Bearing Applications
These engineering powerhouses are indispensable across a multitude of industries where massive structures need to rotate reliably:
Mining: Giant excavators, electric shovels, stackers, reclaimers, bucket wheel excavators, and draglines.
Construction: Tower cranes, large mobile cranes, crawler cranes, piling rigs, and tunnel boring machines (TBMs).
Material Handling & Logistics: Port cranes (STS, RTG, MHC), rail-mounted gantry cranes, bulk handling cranes, and heavy-duty forklifts.
Wind Energy: Yaw systems (rotating the nacelle to face the wind) and pitch systems (adjusting blade angle) on wind turbines.
Industrial Processing: Large ladle turrets in steelmaking, rotary kilns in cement and minerals processing, mixers, and reactors.
Defense & Aerospace: Radar antennas, missile launchers, telescope mounts, and rocket launch platform positioning.
Marine & Offshore: Deck cranes on vessels, offshore pedestal cranes, pipelaying equipment, and cable-laying machinery.
Renewable Energy: Solar tracking systems for large-scale photovoltaic plants.
Defining the Powerhouse: Key Characteristics of Heavy Load Slewing Bearings
Surviving and thriving under extreme conditions demands exceptional attributes:
Colossal Load Capacity: The defining feature – engineered to withstand combined axial, radial, and moment loads reaching thousands of tonnes.
Exceptional Rigidity: Minimal deformation under load is critical to maintain smooth operation, precise positioning, and prevent binding or uneven wear.
Unmatched Durability & Long Life: Manufactured from high-grade alloy steels (e.g., 42CrMo4, 50Mn) with hardened raceways (via carburizing, induction hardening) for superior resistance to wear, pitting, and fatigue, often targeting multi-decade service life.
Smooth, Controlled Rotation: Optimized raceway geometry, precision manufacturing, and effective lubrication ensure low friction rotation even under maximum load, minimizing energy consumption.
Robust Sealing & Protection: Multi-layered sealing systems (labyrinth seals, rubber seals) prevent ingress of contaminants (dust, water, grit) and egress of lubricant, crucial for operation in harsh environments.
Integrated Design: Incorporation of gear teeth for direct drive and mounting holes for simplified assembly onto the host structure.
Advanced Monitoring (Increasingly Common): Integration points for sensors (vibration, temperature) enabling condition monitoring and predictive maintenance strategies.
Decoding the Investment: Factors Influencing Heavy Load Slewing Bearing Price
The price tag for these industrial giants is substantial and varies significantly, driven by a complex interplay of factors:
Size and Weight: Fundamentally, larger diameter and heavier bearings consume vastly more raw material and machining time, exponentially increasing cost.
Bearing Type and Complexity: A simple single-row ball bearing costs far less than a sophisticated double-row ball, crossed roller, or triple-row roller bearing design. Integrated gear teeth add significant machining complexity and cost.
Material Specifications: The grade, quality, and specific alloy of steel required significantly impact price. Higher purity, higher strength, and specialized alloys for extreme environments cost more.
Load and Performance Requirements: Bearings designed for higher static/dynamic load ratings, higher moment capacities, longer design life (e.g., 20+ years for wind), or higher rotational precision demand more robust designs, better materials, and tighter manufacturing tolerances, increasing cost.
Manufacturing Precision & Heat Treatment: Achieving the required micron-level tolerances and performing deep, controlled heat treatments (like carburizing large diameters) require advanced, expensive machinery and skilled labor, contributing heavily to cost.
Special Features & Certifications: Requirements for special seals (extreme temps/corrosion resistance), integrated sensors, specific surface coatings, or adherence to stringent industry certifications (e.g., DNV-GL for marine, CE, nuclear standards) add cost.
Customization Level: Fully bespoke bearings designed from scratch for a unique application are significantly more expensive than modified standard designs or catalogue items.
Quantity: Economies of scale apply; ordering multiple identical bearings reduces the unit cost compared to a single custom piece.
Manufacturer Brand & Reputation: Premium manufacturers with established reputations for quality and reliability often command higher prices.
Logistics: Transporting, handling, and insuring extremely large, heavy components globally adds considerable cost.
Supplier of Slew drive
LYRADRIVE is a professional slewing bearings ,slew drive and gears manufacturer provides customized slew bearing, drive and gears.For application-specific engineering solutions, contact LYRA to discuss technical specifications and implementation strategies.