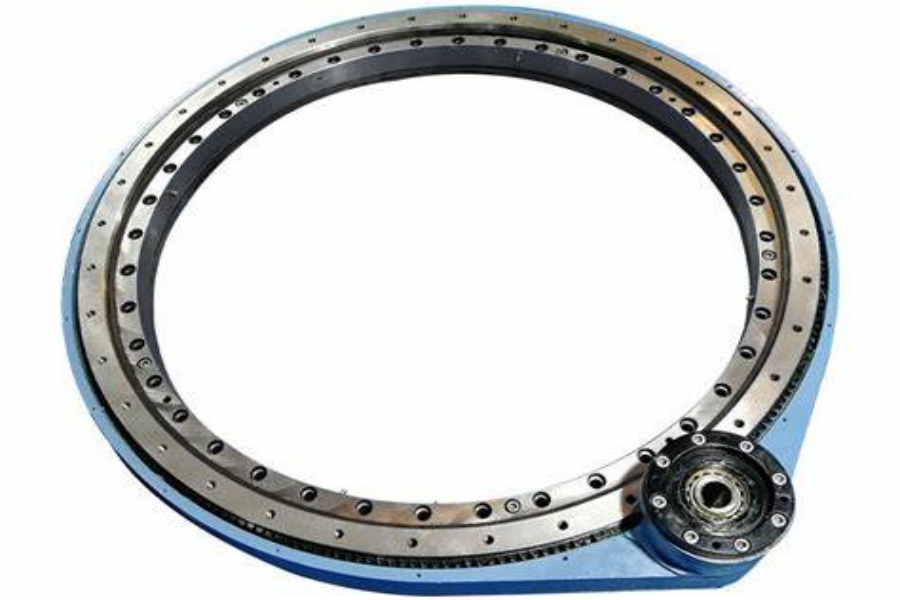
Flanged Ball Slewing Bearings Enabling Precision in Compact Rotation Systems
In the world of precision machinery and space-constrained engineering applications, flanged ball slewing bearings have emerged as critical components that combine rotational accuracy with structural efficiency. These specialized bearings facilitate smooth 360-degree movement in equipment ranging from robotic arms in automated factories to medical imaging devices, delivering reliable performance where traditional bearing solutions would be impractical. As industries increasingly prioritize compact designs without sacrificing load capacity or durability, flanged ball slewing bearings are proving indispensable in bridging the gap between mechanical complexity and operational simplicity.
What Is a Flanged Ball Slewing Bearing
A flanged ball slewing bearing is a rotational bearing system characterized by an integrated mounting flange on one or both rings, designed to handle combined axial, radial, and moment loads while providing secure attachment points for adjacent machine components. The bearing features a single or double row of precision-ground ball elements housed between hardened steel rings, with the flange serving as both a structural interface and a seal protection barrier. The flange’s bolt holes enable direct mounting to machinery frames, eliminating the need for additional housings and reducing overall system weight. Advanced sealing systems integrated into the flange geometry protect against contaminants like dust, moisture, and metal shavings, while specialized lubrication channels ensure consistent performance in applications from -40°C Arctic environments to 120°C industrial ovens.
The fundamental importance of flanged ball slewing bearings lies in their dual role as load-bearing components and structural connectors. In robotic welding cells, these bearings allow robotic arms to rotate smoothly while supporting the weight of welding torches and cabling. Solar tracker systems utilize flanged variants to securely mount photovoltaic panels to support structures while enabling precise sun-following rotation. Their compact profile makes them ideal for MRI machine gantries, where non-magnetic stainless steel versions provide artifact-free imaging while withstanding constant sterilization cycles. The flange design also simplifies maintenance by allowing bearing replacement without disassembling entire machine frames, a critical advantage in production environments minimizing downtime.
Global Innovations in Flanged Ball Slewing Bearing Technology
Engineering Breakthroughs in Traditional Manufacturing Hubs
Countries with established expertise in precision engineering, including Germany, Japan, and Switzerland, continue to lead advancements in flanged ball slewing bearing technology. German manufacturers employ laser-hardened raceways to achieve surface roughness below 0.1 microns, reducing friction torque by 35% in high-speed packaging machinery. Japanese engineers have developed hybrid ceramic flange bearings combining steel rings with silicon nitride balls, cutting weight by 40% while maintaining load capacity in aerospace satellite positioning systems. Swiss producers utilize vacuum-degassed steel alloys to create MRI-compatible bearings that withstand 10,000+ sterilization cycles without corrosion.
The renewable energy sector benefits from flanged bearings with integrated cable pass-throughs in wind turbine pitch systems, allowing uninterrupted power transmission during rotation. The robotics industry adopts variants featuring embedded strain gauges that provide real-time load feedback for collaborative robots handling fragile glass panels. Medical equipment manufacturers leverage radiation-resistant polymer seals in CT scanner bearings exposed to constant X-ray bombardment.
Emerging Markets Advancing Through Technological Adoption
Manufacturers in industrializing regions are closing the technology gap through strategic investments in automation and quality control. Chinese firms implement AI-powered vision systems to inspect flange flatness within 2-micron tolerances during mass production. Indian engineers have pioneered bio-degradable grease formulations that maintain lubrication efficiency in monsoon-prone regions while meeting environmental regulations. Brazilian companies employ blockchain-tracked material sourcing to ensure ethical mineral extraction for bearings used in European medical device exports.
Persistent challenges include mastering micro-crack detection in hardened flanges and optimizing dynamic load distribution algorithms. European manufacturers use synchrotron radiation imaging to detect subsurface defects invisible to conventional X-rays, while developing markets often rely on sample destructive testing that increases material costs. Limited access to high-purity bearing-grade steel in some regions compromises bearing longevity in semiconductor wafer handling robots requiring ultra-clean environments.
Overcoming Technical Challenges in Flanged Bearing Applications
The performance gap between industry leaders and emerging manufacturers centers on three critical factors: material purity, manufacturing consistency, and smart monitoring integration. Premium flanged bearings incorporate diamond-like carbon coatings that reduce adhesive wear by 60% in food processing machinery exposed to acidic cleaning agents. In contrast, conventional coatings in price-sensitive markets degrade rapidly under similar conditions, requiring quarterly replacements in bottling plant rotary tables.
Collaborative R&D initiatives are driving progress through innovations like 3D-printed flange adapters with stress-optimized lattice structures for earthquake-resistant industrial mixers. Another breakthrough involves triboelectric nanosensors embedded in flange seals that harvest energy from bearing rotation to power wireless condition monitoring systems. Workforce development programs using augmented reality installation guides have reduced bearing replacement times by 50% in offshore wind turbine maintenance operations.
The Future of Flanged Ball Slewing Bearings Smart and Sustainable Solutions
Next-generation flanged bearings will prioritize energy-neutral operation, self-healing materials, and circular lifecycle management. Prototype piezoelectric flange bearings currently in testing convert mechanical vibration from rotating machinery into stored energy for IoT sensors. Material scientists are experimenting with mycelium-based flange composites that provide 70% of steel’s strength while being fully compostable at end-of-life.
In smart manufacturing ecosystems, these bearings will evolve into intelligent system nodes. Imagine pharmaceutical plants where flange bearing sensors detect microscopic vibration changes predictive of conveyor belt failures. Agricultural drones could utilize bearings with soil compaction sensors to automatically adjust seed planting depth based on real-time terrain data.
Strategic Implementation Best Practices
Precision Mounting Protocols:Use laser-aligned torque wrenches to ensure uniform flange bolt tension within 2% variance, critical for maintaining bearing concentricity in high-speed CNC indexing tables.
Environment-Specific Material Selection:Specify titanium diboride-coated flanges for saltwater aquaculture equipment and PEEK polymer seals for bearings in chemical reactor agitators.
Predictive Maintenance Integration:Deploy acoustic emission arrays that detect early-stage raceway pitting through ultrasonic frequency analysis during scheduled production pauses.
Circular Design Principles:Implement flange bearings with modular component architecture allowing individual raceway replacement, reducing material waste by 80% during refurbishment.
Flanged ball slewing bearings supplier
Flanged ball slewing bearings exemplify the marriage of mechanical ingenuity and practical design, enabling technological leaps across industries from precision medicine to green energy. As global manufacturing trends emphasize sustainability and smart automation, these components are transitioning from passive rotation enablers to active system participants. While established markets continue to innovate with atomically engineered materials and digital twins, emerging economies prove that AI-enhanced production and collaborative research can democratize access to cutting-edge bearing technology. The future promises flanged bearings that not only support machinery but also generate operational insights, recover energy, and return safely to the ecosystem. For industry leaders, embracing this dual focus on peak performance and planetary stewardship will define success in the new era of intelligent manufacturing.
LYRA Drive is a professional slewing bearings ,slew drive and gears manufacturer provides customized slew bearing, drive and gears.For application-specific engineering solutions, contact LYRA to discuss technical specifications and implementation strategies.