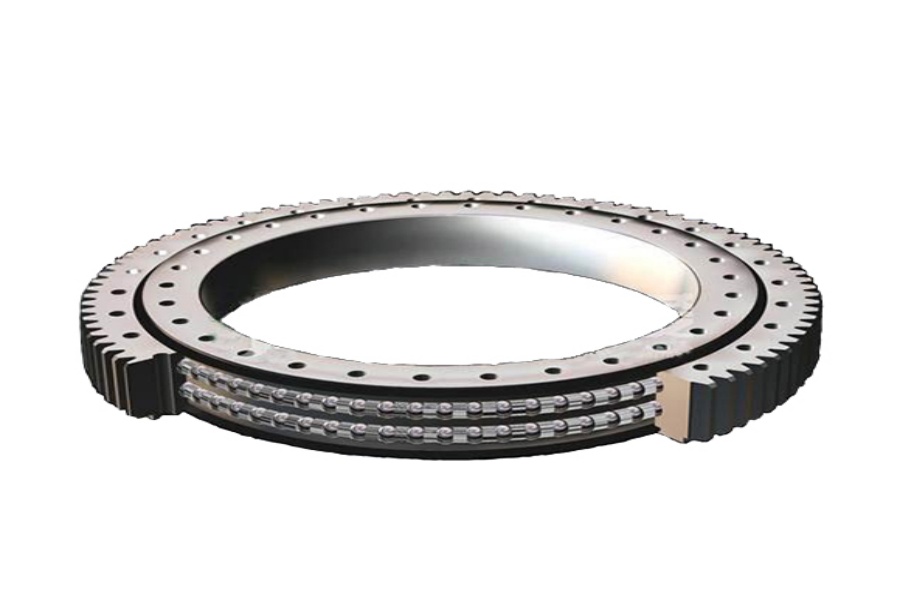
SP-H Slew Drives Elevating Performance in Extreme-Duty Applications
In the demanding world of heavy industry and precision engineering, SP-H Slew Drives have emerged as mission-critical components enabling robust rotational control under the most challenging operational conditions. These advanced systems power everything from mega-scale mining excavators to offshore wind turbine positioning mechanisms, combining unparalleled strength with micron-level accuracy. As industries push the boundaries of load capacity and environmental resilience, SP-H Slew Drives are redefining engineering standards through innovative material science and intelligent system integration.
What Is an SP-H Slew Drive
An SP-H Slew Drive is a heavy-duty rotational mechanism integrating a reinforced slewing bearing with a precision gear system engineered to handle extreme axial, radial, and moment loads exceeding 15,000 metric tons. The system employs a hardened helical or planetary gear arrangement paired with a multi-row roller slewing ring fabricated from ultra-high-strength alloys and nano-composites treated for maximum impact resistance and thermal endurance. Advanced multi-labyrinth sealing systems shield internal components from abrasive particulates, high-pressure water ingress, and chemical corrosion, while adaptive lubrication networks maintain peak performance in applications ranging from deep-sea drilling rigs to desert mining operations.
The transformative nature of SP-H Slew Drives lies in their ability to deliver sub-arcminute precision under catastrophic load conditions. In open-pit mining operations, these drives enable 360-degree rotation of 800-ton excavator booms while maintaining positional stability on uneven terrain. Offshore crane systems utilize SP-H drives to position subsea modules weighing 2,000 tons with centimeter accuracy despite ocean currents and wave action. Their fail-safe architecture incorporates redundant braking systems and real-time load monitoring, ensuring operational continuity in critical infrastructure projects like nuclear reactor construction and space launch platform assembly.
Global Innovations in SP-H Slew Drive Technology
Cutting-Edge Developments in Engineering Powerhouses
Countries with deep industrial expertise, including Germany, Japan, and Norway, continue to pioneer SP-H Slew Drive advancements. German manufacturers deploy plasma-transferred arc welding to create gear teeth with diamond-like surface hardness, reducing wear rates by 40% in high-abrasion mining environments. Japanese engineers have perfected hydrostatic bearing configurations that eliminate metal-to-metal contact in ultra-heavy loads, extending service life to 150,000 hours in port megacranes. Norwegian innovators utilize sub-zero tempering processes to enhance fracture resistance in alloys used for Arctic offshore wind farm installations.
The energy sector benefits from SP-H drives with self-cooling gearboxes that maintain operational integrity in geothermal plants exposed to 300°C steam. The aerospace industry employs titanium-matrix composite variants weighing 50% less than steel while handling 10,000 Nm torque in rocket launch turntables. Advanced robotics applications leverage drives with embedded fiber-optic strain sensors, enabling real-time deflection compensation in 100-ton automated forging presses.
Emerging Markets Closing the Technology Divide
Manufacturers in industrializing nations are adopting hybrid strategies to compete globally. Chinese producers implement quantum computing-optimized heat treatment protocols achieving material properties matching premium European grades. Indian engineers have developed cactus-inspired lubrication systems using natural waxes that outperform synthetics in dusty quarry environments, reducing maintenance intervals by 60%. Brazilian firms employ AI-powered corrosion prediction models to extend drive lifespan in Amazonian hydroelectric projects plagued by constant humidity.
Persistent challenges include mastering multi-physics load modeling and ensuring nanoscale material consistency. European manufacturers use neutron diffraction imaging to map residual stresses in 10-meter diameter bearings, while developing markets often rely on destructive testing methods that increase scrap rates. Limited access to cryogenic forging facilities hinders production of drives for liquefied natural gas tanker applications requiring -162°C operational capability.
Overcoming Technical Barriers in SP-H Slew Drive Implementation
The performance gap between industry leaders and emerging manufacturers hinges on three pillars: alloy innovation, manufacturing tolerances, and predictive analytics integration. Premium SP-H drives incorporate carbon nanotube-reinforced raceways showing 70% lower wear rates in 24/7 ore processing plants, while conventional steel variants in developing markets require quarterly rebuilds under similar loads.
Global R&D consortia are driving breakthroughs through projects like 4D-printed metamaterials that alter stiffness profiles in response to load direction, revolutionizing drives for earthquake-prone regions. Another innovation involves edge AI prognostic systems that analyze lubricant dielectric properties to predict gear pitting 12 months before failure. Workforce upskilling initiatives using mixed reality maintenance simulators have reduced crane drive replacement times from 72 hours to 18 hours in offshore installations.
The Future of SP-H Slew Drives Smart Adaptive and Sustainable
Next-generation SP-H drives will prioritize zero-maintenance operation, energy-positive systems, and closed-loop material cycles. Prototype piezoelectric friction harvesters now convert gear mesh vibrations into usable power, achieving 15% net energy reduction in continuous mining operations. Material breakthroughs include mycelium-reinforced biocomposites matching 60% of steel's strength while enabling full biodegradation of decommissioned drives.
In smart infrastructure networks, these drives will function as autonomous system nodes. Envision Arctic shipping hubs where SP-H drives auto-adjust cargo crane speeds based on real-time ice thickness data transmitted from satellites. Smart mining systems could utilize drives with ore density sensors to dynamically optimize excavation torque, reducing energy waste while preventing equipment overload.
Strategic Implementation Best Practices
Ultra-Precision Alignment:Employ neutron beam alignment verification for drives exceeding 8-meter diameters in nuclear reactor applications requiring 0.001° rotational accuracy.
Extreme-Environment Material Specification:Select boron-carbide ceramic coatings for drives in molten metal handling systems and superhydrophobic seals for subsea installations below 3,000-meter depths.
Cognitive Maintenance Systems:Deploy muon tomography scanners to non-invasively map internal component wear in mission-critical drives without disassembly.
Circular Lifecycle Management:Implement block chain-tracked component passports enabling 95% material recovery rates during drive refurbishment cycles.
SP-H Slew Drives supplier
SP-H Slew Drives represent the apex of mechanical engineering merged with digital intelligence, enabling feats of precision lifting and rotation previously deemed impossible. As global industries confront escalating demands for mega-scale projects and environmental responsibility, these components are evolving from brute-force mechanisms into sentient system orchestrators. While technological pioneers continue pushing boundaries with atomic-scale material innovations, emerging markets prove that AI-enhanced manufacturing and collaborative R&D can democratize access to cutting-edge capabilities. The future promises SP-H drives that not only withstand unprecedented forces but actively contribute to planetary-scale sustainability efforts. For industry leaders, embracing this dual mandate of extreme performance and ecological stewardship will define success in the new era of heavy engineering.
LYRA Drive is a professional slewing bearings ,slew drive and gears manufacturer provides customized slew bearing, drive and gears.For application-specific engineering solutions, contact LYRA to discuss technical specifications and implementation strategies.