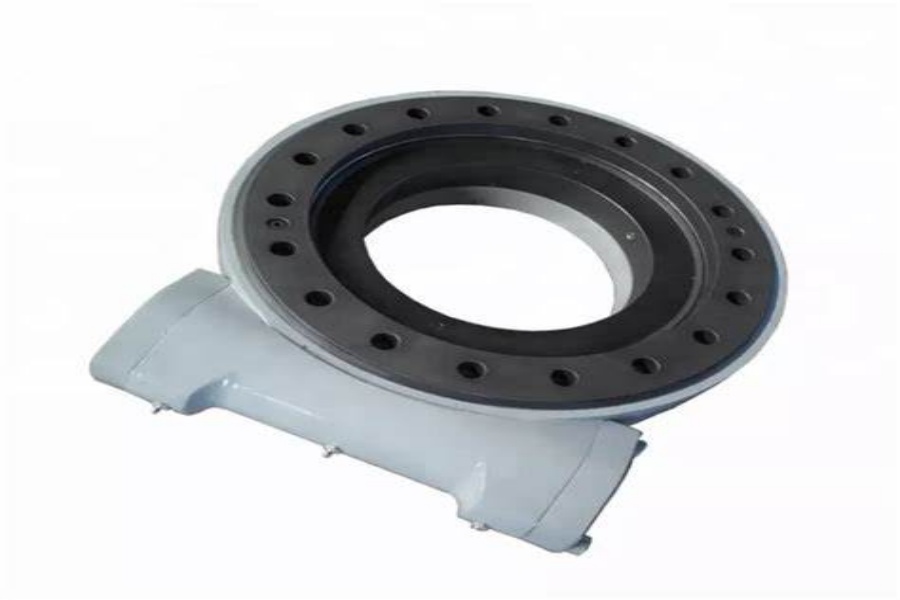
SP-I Slew Drives The Next Frontier in Precision Rotation Technology
In the competitive world of industrial automation and renewable energy systems, SP-I Slew Drives have emerged as transformative components enabling unparalleled rotational control in demanding environments. These advanced systems power critical applications from solar tracker arrays optimizing energy harvest to construction cranes lifting massive loads with surgical precision. As industries increasingly prioritize efficiency, durability, and smart functionality, SP-I Slew Drives are redefining performance standards by merging mechanical strength with intelligent control systems to meet the complex demands of modern engineering.
What Is an SP-I Slew Drive
An SP-I Slew Drive is an integrated rotational mechanism combining a high-capacity slewing bearing with a precision-engineered gear system designed to deliver controlled 360-degree movement under extreme axial, radial, and moment loads. The system features a helical or planetary gear arrangement paired with a hardened slewing ring constructed from advanced alloys and composite materials treated for maximum wear resistance and thermal stability. Multi-stage sealing technologies protect against environmental contaminants such as abrasive dust, moisture, and corrosive chemicals, while optimized lubrication channels ensure consistent performance in both high-speed and high-torque scenarios across industries including renewable energy, construction, and marine operations.
The significance of SP-I Slew Drives lies in their unique ability to balance raw power with micrometer-level precision. In solar energy installations, these drives adjust photovoltaic panels to track the sun’s path with sub-degree accuracy, boosting energy output by up to 35% compared to fixed systems. For port cranes handling multi-ton shipping containers, SP-I drives enable precise positioning even during high winds or uneven load distribution. Their modular architecture allows customization for specific operational requirements, while integrated safety mechanisms such as automatic load locking ensure stability during power interruptions, making them indispensable in high-risk applications like offshore drilling platforms and aerospace launch systems.
Global Innovations in SP-I Slew Drive Technology
Breakthroughs in Technologically Advanced Regions
Countries with established engineering prowess, such as Germany, Japan, and Sweden, continue to pioneer advancements in SP-I Slew Drive capabilities. German manufacturers utilize laser-aided surface hardening to create gear teeth with sub-micron precision, reducing friction losses by 30% in high-speed robotic assembly lines. Japanese engineers have developed asymmetric bearing raceways that dynamically redistribute stress during sudden load changes, extending component lifespan in mining equipment subjected to constant shock loads. Swedish innovators employ additive manufacturing to produce lightweight gear structures with internal cooling channels, enhancing thermal management for solar trackers operating in desert climates.
The renewable energy sector benefits from SP-I Slew Drives equipped with self-regenerating polymer seals that repair minor surface damage caused by sandstorms in arid regions. The maritime industry adopts drives made from saltwater-resistant alloys that prevent biofouling and corrosion in underwater inspection robots maintaining offshore wind farms. Robotics applications leverage variants with integrated torque sensors, enabling collaborative robots to handle fragile electronics with precision during high-speed manufacturing processes.
Emerging Markets Accelerating Technological Progress
Manufacturers in industrializing regions are rapidly adopting smart technologies to enhance production quality. Chinese producers implement AI-powered defect detection systems that identify microscopic imperfections in gear teeth during machining, achieving global performance benchmarks. Indian engineers have innovated plant-oil-based lubricants that outperform synthetic greases in high-temperature steel mill applications, reducing maintenance intervals by 40%. Brazilian firms utilize blockchain-tracked material sourcing to ensure compliance with international standards for drives used in large-scale hydroelectric projects.
Challenges remain in areas such as multi-axis fatigue simulation and material consistency control. European manufacturers employ digital twin technology to simulate 20-year wear patterns in months, while emerging markets often rely on iterative physical testing, prolonging development cycles. Limited access to ultra-high-grade steel forging facilities in certain regions impacts the reliability of drives deployed in extreme environments like Arctic logistics hubs.
Overcoming Technical Challenges in SP-I Slew Drive Applications
The performance gap between global leaders and developing manufacturers hinges on three critical factors: material innovation, manufacturing precision, and smart system integration. Premium SP-I Slew Drives incorporate nanocarbon coatings that reduce surface wear by 50% in high-cycle industrial robots, whereas conventional coatings in budget-focused markets degrade rapidly under similar operational stress.
Collaborative research initiatives are driving advancements. University partnerships are developing 4D-printed adaptive alloys that adjust their molecular structure in response to temperature fluctuations, maintaining gear alignment in solar farms exposed to desert heat waves. Another breakthrough involves edge computing units embedded within drive assemblies, analyzing vibration patterns to predict bearing failures nine months in advance. Workforce training programs using augmented reality guides have reduced installation errors by 50% in complex systems like bridge construction cranes.
The Future of SP-I Slew Drives Intelligence and Sustainability
Next-generation SP-I Slew Drives will focus on energy-efficient operation, self-diagnostic capabilities, and eco-friendly materials. Prototype kinetic energy recovery systems currently under testing convert braking inertia into stored power for onboard sensors, reducing energy consumption by 25%. Material scientists are experimenting with algae-based composites that provide 70% of traditional steel’s strength while being fully compostable, addressing end-of-life environmental impact.
In smart industrial ecosystems, these drives will operate as autonomous decision-makers. Imagine smart cities where SP-I Slew Drives adjust traffic monitoring cameras based on real-time congestion data, optimizing urban mobility without human intervention. Agricultural drones could utilize drives with soil nutrient sensors to autonomously adjust fertilizer spray patterns, maximizing crop yields while minimizing chemical waste.
Strategic Implementation Best Practices
Precision Alignment Protocols:Use laser-guided calibration tools during assembly to ensure gear meshing within 0.02mm tolerance, critical for applications like satellite dish positioning requiring sub-arcminute accuracy.
Environment-Specific Material Choices:Select titanium-zirconium coatings for coastal infrastructure projects and ceramic-infused seals for high-temperature manufacturing plants.
Predictive Maintenance Integration:Deploy ultrasonic monitoring systems that detect subsurface cracks in raceways, enabling repairs during scheduled downtime in wind turbine installations.
Circular Design Principles:Implement modular architectures allowing individual gear replacement, reducing material waste by 60% during drive refurbishments.
SP-I Slew Drives supplier
SP-I Slew Drives embody the convergence of mechanical ingenuity and technological innovation, driving advancements across sectors from clean energy to advanced manufacturing. As global industries pivot toward sustainability and automation, these components are evolving from passive mechanical parts into intelligent, adaptive systems. While technological leaders continue to push boundaries with advanced materials and digital integration, emerging markets demonstrate that strategic investments in smart manufacturing and collaborative R&D can bridge innovation gaps. The future promises SP-I Slew Drives that deliver peak performance while supporting a sustainable industrial ecosystem. For industry stakeholders, adopting forward-thinking strategies and eco-conscious practices will be pivotal in shaping the next chapter of engineering excellence.
LYRA Drive is a professional slewing bearings ,slew drive and gears manufacturer provides customized slew bearing, drive and gears.For application-specific engineering solutions, contact LYRA to discuss technical specifications and implementation strategies.