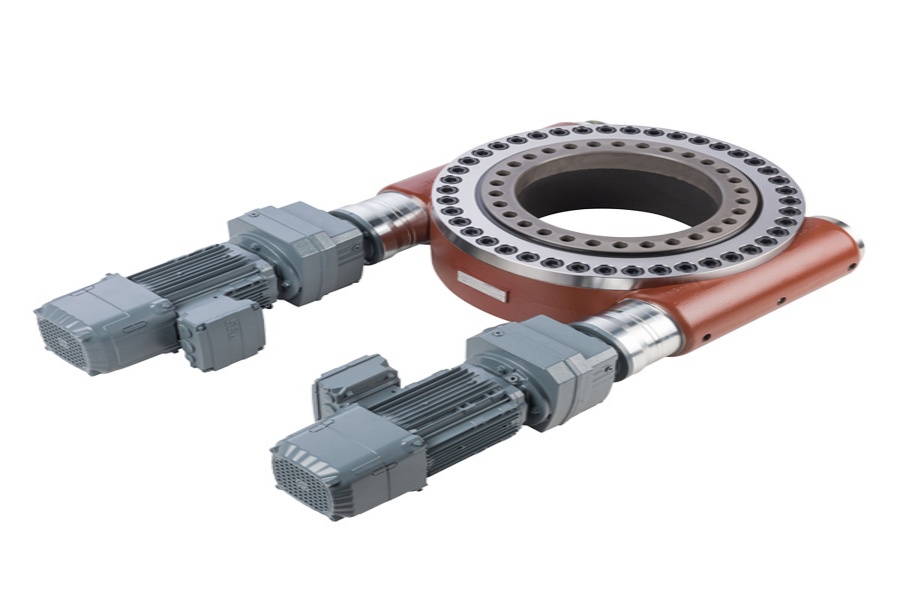
WED Slew Drives Revolutionizing Heavy-Duty Rotational Control
In the rapidly evolving landscape of industrial machinery and renewable energy systems, WED Slew Drives have emerged as critical components enabling precise rotational movement under extreme operational demands. These advanced systems facilitate the operation of equipment ranging from wind turbine yaw mechanisms to heavy construction cranes, combining mechanical robustness with intelligent control. As industries worldwide prioritize efficiency, durability, and smart automation, WED Slew Drives are setting new benchmarks for performance, ensuring reliability in environments where precision and power must coexist seamlessly.
What Is a WED Slew Drive
A WED Slew Drive is an integrated rotational drive system that merges a high-capacity slewing bearing with a precision-engineered gear mechanism, designed to deliver controlled 360-degree movement under substantial axial, radial, and moment loads. The system typically incorporates a helical or planetary gear arrangement paired with a hardened slewing ring, constructed from advanced alloys and composite materials treated for enhanced wear resistance and thermal stability. Multi-layered sealing technologies protect against environmental contaminants such as dust, moisture, and corrosive agents, while optimized lubrication systems ensure consistent performance in both high-speed and high-torque applications across industries like renewable energy, construction, and marine operations.
The critical role of WED Slew Drives lies in their ability to harmonize immense power with exacting precision. In wind energy systems, these drives adjust turbine nacelles to optimal angles, maximizing energy capture while enduring hurricane-force winds and saltwater exposure. For port cranes, they enable the precise positioning of shipping containers weighing hundreds of tons, even in challenging coastal weather conditions. Their modular design allows customization for specific load capacities and rotational speeds, while integrated safety features such as automatic braking systems prevent unintended movement during power failures, ensuring operational integrity in critical applications like offshore oil rigs or aerospace launch facilities.
Global Innovations in WED Slew Drive Technology
Technological Leadership in Advanced Markets
Countries with established engineering expertise, including Germany, Japan, and Sweden, continue to drive advancements in WED Slew Drive capabilities. German manufacturers employ laser-hardened gear surfaces to achieve sub-micron precision, reducing friction losses by 25% in high-speed industrial automation systems. Japanese engineers have developed asymmetric roller bearing configurations that redistribute stress during sudden load shifts, extending component lifespan in mining excavators. Swedish innovators utilize additive manufacturing techniques to create lightweight gear structures with internal cooling channels, enhancing thermal management in continuous-operation scenarios for solar tracking systems.
The renewable energy sector benefits from WED Slew Drives equipped with self-lubricating polymer composites that eliminate the need for frequent maintenance in remote wind farms. The maritime industry leverages drives constructed from hydrophobic alloys resistant to biofouling and corrosion in underwater robotic systems used for offshore pipeline inspections. Robotics applications utilize variants with embedded torque sensors, providing real-time feedback to ensure precise handling of delicate components in automated assembly lines.
Emerging Markets Bridging the Technology Gap
Manufacturers in industrializing regions are rapidly adopting advanced technologies to enhance competitiveness. Chinese producers implement AI-driven metallurgical analysis to optimize material compositions for local environmental conditions, achieving performance parity with global counterparts. Indian engineers have pioneered bio-based lubrication systems derived from plant oils, outperforming traditional greases in high-temperature steel mill applications. Brazilian firms employ blockchain-based traceability systems to ensure material integrity for drives used in Amazonian hydropower projects, improving quality assurance.
Challenges persist in areas such as multi-axis fatigue testing and material homogeneity. European manufacturers utilize digital twin simulations to predict decade-long wear patterns within weeks, while emerging markets often rely on physical prototyping, extending development cycles. Limited access to ultra-high-purity steel production facilities in certain regions impacts the durability of drives deployed in extreme environments like Arctic mining operations.
Overcoming Technical Challenges in WED Slew Drive Applications
The technological divide between industry leaders and developing manufacturers centers on material science, manufacturing accuracy, and smart system integration. Premium WED Slew Drives incorporate nanostructured coatings that reduce surface wear by 40% in high-cycle packaging machinery, whereas conventional coatings in cost-sensitive markets degrade rapidly under similar stress.
Collaborative initiatives are accelerating progress. Academic partnerships are developing 4D-printed shape-memory alloys that adapt to thermal fluctuations in desert solar installations, maintaining gear alignment under extreme temperature variations. Another innovation involves edge computing modules embedded within drive housings, analyzing vibration data to predict bearing wear six months in advance. Workforce training programs using augmented reality simulations have reduced installation errors by 35% in complex installations like bridge construction equipment.
The Future of WED Slew Drives Intelligence and Sustainability
Next-generation WED Slew Drives will prioritize energy efficiency, self-monitoring capabilities, and eco-friendly materials. Prototype kinetic energy recovery systems currently in testing convert rotational inertia into stored electrical energy, powering onboard sensors and reducing external power dependency. Material scientists are experimenting with mycelium-based composites that offer 75% of traditional steel’s strength while being fully biodegradable, addressing end-of-life environmental concerns.
In smart industrial networks, these drives will evolve into autonomous decision-makers. Imagine offshore wind farms where WED Slew Drives adjust turbine orientations based on real-time weather forecasts and grid demand, optimizing energy output autonomously. Autonomous agricultural machinery could utilize drives with soil moisture sensors to automatically adjust irrigation arms, conserving water while maximizing crop yields.
Strategic Implementation Guidelines
Precision Calibration:Deploy laser alignment systems during assembly to ensure gear meshing within 0.02mm tolerance, critical for high-precision applications like satellite antenna positioning.
Environment-Specific Material Selection:Specify titanium-aluminum nitride coatings for coastal crane drives and ceramic-embedded seals for high-temperature industrial kilns.
Predictive Maintenance Integration:Implement fiber-optic sensing networks to monitor internal stress distribution in real time, enabling preemptive maintenance in wind turbine installations.
Circular Economy Practices:Design drives with modular components to facilitate individual part replacement, minimizing waste during refurbishments and supporting sustainability goals.
WED Slew Drives supplier
WED Slew Drives represent the pinnacle of mechanical and technological integration, driving advancements across industries from renewable energy to advanced robotics. As global priorities shift toward sustainability and intelligent automation, these components are transitioning from passive mechanical parts to adaptive, self-optimizing systems. While established markets continue to lead with innovations in advanced materials and digital integration, emerging economies demonstrate that strategic investments in smart manufacturing and collaborative R&D can narrow technological gaps. The future promises WED Slew Drives that deliver unparalleled performance while fostering a sustainable industrial ecosystem. Embracing innovation and eco-conscious practices will be essential for industry leaders to shape the next era of engineering excellence.
LYRA Drive is a professional slewing bearings ,slew drive and gears manufacturer provides customized slew bearing, drive and gears.For application-specific engineering solutions, contact LYRA to discuss technical specifications and implementation strategies.