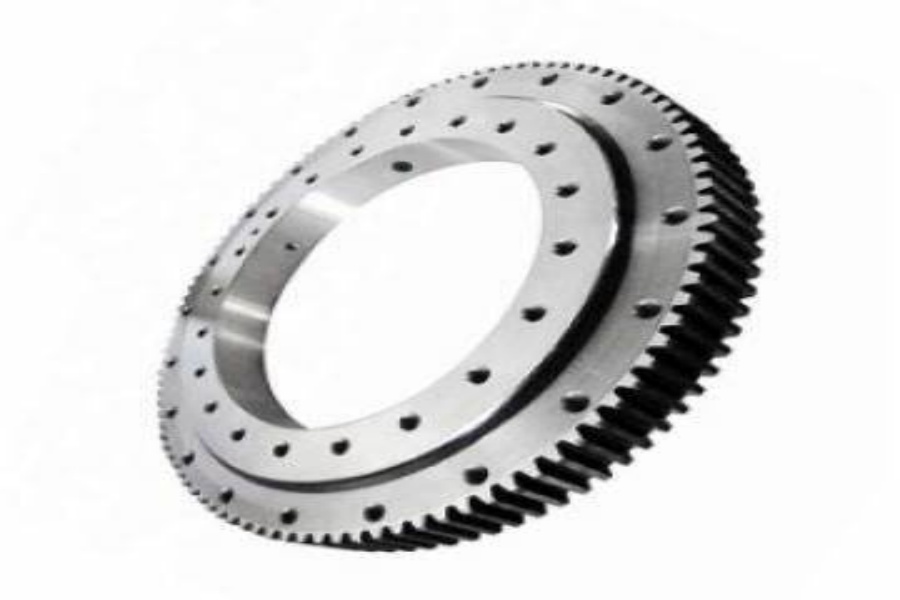
Single Row Slewing Ring Ball Bearings The Backbone of Compact Rotational Systems
In the realm of precision engineering and industrial machinery, single row slewing ring ball bearings have become indispensable components for applications requiring smooth rotational movement within confined spaces. These bearings enable critical functions in equipment ranging from medical imaging devices to compact construction machinery, balancing load capacity with space efficiency. As industries increasingly demand miniaturization without compromising performance, single row slewing ring ball bearings are proving vital in achieving both precision and reliability in modern mechanical systems.
What Is a Single Row Slewing Ring Ball Bearing
A single row slewing ring ball bearing is a rotational bearing system featuring a single circular row of ball elements positioned between two concentric rings, designed to handle combined axial, radial, and moment loads in applications requiring 360-degree rotation. The inner and outer rings are typically manufactured from high-grade alloy steel, hardened and ground to precise tolerances, while the ball elements distribute loads evenly across the raceway. Integrated seals and lubrication channels protect the bearing from contaminants like dust and moisture, ensuring longevity in harsh environments.
The significance of these bearings lies in their compact design and versatile load-handling capabilities. In CT scanners, they enable the silent, precise rotation of gantries during medical imaging procedures. For solar tracking systems, they allow photovoltaic panels to follow the sun’s path with minimal energy consumption. Their low-profile construction makes them ideal for robotic arms in automated assembly lines, where space constraints prohibit bulkier bearing solutions. The single row configuration provides a cost-effective solution for moderate-load applications while maintaining the accuracy required in precision instruments like telescope mounts and radar systems.
Global Innovations in Single Row Slewing Ring Ball Bearing Technology
Precision Engineering Advancements
Countries renowned for mechanical innovation, including Germany, Japan, and Switzerland, continue to push the boundaries of single row slewing ring bearing performance. German manufacturers utilize laser-etched raceway surfaces to achieve micron-level smoothness, reducing friction torque by 30% in high-speed dental drill handpieces. Japanese engineers have developed hybrid ceramic ball bearings combining steel races with silicon nitride balls, cutting weight by 45% while maintaining load capacity in aerospace applications. Swiss producers employ vacuum induction melting to create ultra-clean steel alloys, extending bearing life in MRI machines exposed to constant electromagnetic fields.
The renewable energy sector benefits from bearings with self-lubricating polymer cages that eliminate maintenance in solar tracker systems operating in desert environments. The robotics industry adopts variants with integrated Hall-effect sensors, providing real-time positional feedback for collaborative robots handling microelectronics. Medical device manufacturers leverage non-magnetic stainless steel bearings that ensure artifact-free imaging in MRI equipment while withstanding repeated sterilization cycles.
Emerging Markets Enhancing Production Capabilities
Manufacturers in industrializing regions are adopting advanced technologies to improve product quality. Chinese firms implement AI-driven optical inspection systems to detect sub-micron surface defects during production, achieving precision levels once exclusive to premium brands. Indian engineers have pioneered bio-based greases derived from plant oils, outperforming synthetic lubricants in high-humidity food processing equipment. Brazilian companies utilize blockchain-tracked raw materials to ensure compliance with international safety standards for bearings used in pharmaceutical manufacturing.
Challenges remain in mastering micro-scale heat treatment and dynamic load modeling. European manufacturers use computational fluid dynamics to optimize lubrication film thickness in high-speed applications, while emerging markets often rely on empirical methods that limit performance consistency. Access to ultra-high-purity bearing steel remains restricted in some regions, affecting the reliability of bearings in critical applications like semiconductor manufacturing robots.
Overcoming Technical Challenges in Single Row Bearing Applications
The performance gap between industry leaders and developing manufacturers centers on three key areas: material science, manufacturing precision, and smart integration. Premium bearings incorporate diamond-like carbon coatings that reduce wear rates by 50% in continuous-rotation security cameras, while conventional bearings in cost-sensitive markets exhibit accelerated fatigue in similar applications.
Collaborative initiatives are driving progress. University partnerships are developing 3D-printed gradient alloys that transition from flexible cores to hardened surfaces, ideal for bearings in vibration-prone industrial mixers. Another breakthrough involves triboelectric sensor arrays embedded in bearing seals, generating power from rotation to enable self-powered condition monitoring. Workforce training programs using virtual reality assembly simulations have reduced installation errors by 40% in precision optical equipment manufacturing.
The Future of Single Row Slewing Ring Ball Bearings Intelligent and Sustainable
Next-generation bearings will prioritize energy efficiency, self-diagnostic capabilities, and eco-friendly materials. Prototype energy-harvesting bearings now under development convert mechanical vibration into stored electricity for onboard sensors in IoT-enabled machinery. Material scientists are experimenting with flax-fiber reinforced composites offering 60% of steel’s strength with 80% lower carbon footprint for disposable medical equipment bearings.
In smart industrial ecosystems, these bearings will serve as data collection nodes. Imagine smart factories where bearing-embedded sensors predict conveyor belt failures by analyzing rotational harmonics. Agricultural drones could use bearings with pollen density sensors to autonomously adjust flight patterns during crop pollination missions.
Strategic Implementation Guidelines
Precision Mounting Procedures:Use laser alignment tools to ensure bearing concentricity within 5 microns during installation, critical for applications like laboratory centrifuges requiring perfect balance.
Environment-Specific Material Selection:Opt for titanium nitride-coated bearings in coastal robotics applications and PEEK polymer cages for chemical processing equipment exposed to corrosive vapors.
Predictive Maintenance Integration:Implement ultrasonic thickness gauges to monitor raceway wear in real time, scheduling replacements during planned maintenance windows.
Circular Economy Practices:Design modular bearing systems allowing individual component replacement, reducing material waste by 70% during refurbishments.
Single Row Slewing Ring Ball Bearings supplier
Single row slewing ring ball bearings exemplify the synergy between mechanical simplicity and technological sophistication, enabling advancements across industries from healthcare to renewable energy. As global trends favor miniaturization and sustainability, these components are evolving from passive mechanical elements into intelligent system enablers. While established markets continue to lead in nano-engineered materials and digital integration, emerging economies demonstrate that strategic investments in smart manufacturing can accelerate technological parity. The future promises bearings that not only rotate machinery but also generate data, harvest energy, and biodegrade responsibly. For engineers and industry leaders, embracing these dual imperatives of performance and sustainability will be crucial in driving the next wave of industrial innovation.
LYRA Drive is a professional slewing bearings ,slew drive and gears manufacturer provides customized slew bearing, drive and gears.For application-specific engineering solutions, contact LYRA to discuss technical specifications and implementation strategies