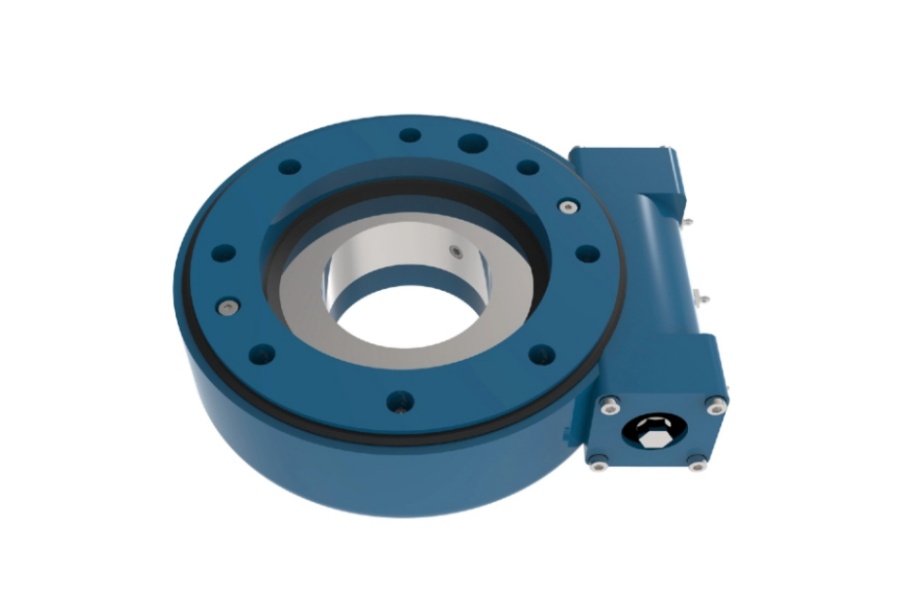
Exploring the Enveloping Rotary Drive Unit SE7
What is the Enveloping Slewing Drive SE7?
Enveloping Slewing Drive SE7 is a highly engineered, integrated drive system designed to provide smooth, precise, and powerful rotational movement. Unlike conventional drives, its defining characteristic lies in its unique gear geometry. The SE7 utilizes a hardened, precision-ground enveloping worm that wraps around a concave, hourglass-shaped worm wheel. This specific meshing geometry creates significantly more tooth contact area compared to standard worm gears. The result is an inherently robust assembly capable of transmitting exceptionally high torque loads within a compact footprint. The SE7 is typically supplied as a complete, sealed unit, incorporating high-capacity bearings (often crossed roller bearings), seals, housings, and mounting interfaces, ready for direct integration into machinery. This integration simplifies design, enhances structural integrity, and ensures optimal performance out-of-the-box.
Enveloping Rotary Drive Principle
The core principle behind the Enveloping Slewing Drive SE7 is the enveloping action between the worm and the worm wheel. The worm features a concave profile that precisely matches the convex curvature of the worm wheel teeth. As the worm rotates, its threads progressively engage with multiple teeth on the wheel simultaneously across a wide arc of contact. This multi-tooth engagement is fundamentally different from the limited point or line contact found in standard worm gears or spur/helical gears. The enveloping action distributes the transmitted load over a much larger surface area of the gear teeth. This dramatically reduces localized contact stress, minimizes wear, and significantly increases the drive's overall torque capacity and resistance to shock loads. Furthermore, the sliding action inherent in worm drives provides a natural self-locking capability under certain conditions (depending on the lead angle), preventing back-driving without the need for additional braking mechanisms, enhancing safety in many applications. The precision manufacturing of both worm and wheel ensures minimal backlash and smooth, quiet operation even under heavy loads.
Enveloping Rotary Drive Unit in Extreme Conditions
The Enveloping Slewing Drive SE7 truly distinguishes itself when operating beyond the limits of conventional drives. Its robust design and inherent characteristics make it the preferred solution for environments characterized by:
Exceptional Loads: SE7 units handle massive static and dynamic loads, including severe shock loads encountered in heavy lifting (cranes, hoists), material processing (crushers, mills), and large-scale positioning systems.
Harsh Environments: Sealed housings and high-quality seals protect critical internal components from pervasive contaminants like dust, grit, moisture, and corrosive agents prevalent in mining, construction, offshore platforms, and pulp & paper mills.
Temperature Extremes: Engineered with materials and lubricants (often synthetic, high-temperature greases) suitable for operation in freezing Arctic conditions or the intense heat found near furnaces or in foundries.
Continuous Operation: The high efficiency (for a worm drive) and reduced contact stress translate to lower operating temperatures and exceptional durability, enabling reliable 24/7 operation in critical processes like power generation or continuous production lines.
Demanding Precision: Despite the high loads, the enveloping principle and precision manufacturing allow the SE7 to maintain controlled, precise rotational positioning, essential in radar systems, telescope mounts, solar trackers, and sophisticated automation, even when exposed to environmental stressors.
Enveloping Slewing Drive SE7 Characteristics
The SE7 embodies a suite of advanced features engineered for peak performance and longevity:
Unmatched Torque Density: Delivers exceptionally high torque output relative to its compact size and weight, optimizing space utilization in machinery design.
Exceptional Load Capacity: Designed to withstand extreme radial, axial, and moment loads simultaneously, often specified by its static and dynamic load ratings.
High Rigidity & Precision: The integrated structure with high-capacity bearings ensures minimal deflection under load, maintaining positional accuracy and repeatability.
Low Backlash: Precision grinding and optimized pre-loading result in minimal backlash, crucial for accurate positioning and smooth motion control.
Robust Construction: Utilizes high-strength alloy steels for gears, hardened and ground for wear resistance. Housings are typically high-grade cast iron or steel.
Superior Sealing: Multi-layered sealing systems (often including labyrinth seals and high-performance lip seals) provide excellent protection against ingress of contaminants and egress of lubricant.
Integrated Design: Comes as a complete, pre-lubricated, and pre-assembled unit, simplifying installation and maintenance while ensuring component compatibility.
Self-Locking Potential: Offers inherent resistance to back-driving (dependent on the specific worm lead angle), enhancing safety in vertical or inclined applications without requiring constant brake engagement.
Smooth & Quiet Operation: The enveloping action and precision manufacturing contribute to remarkably smooth and quiet running, even at high loads.
Enveloping Slewing Drive SE7 Applications
The combination of power, precision, durability, and compactness makes the SE7 indispensable across a vast spectrum of demanding industries:
Heavy Machinery: Cranes (slewing, luffing), excavators, tunnel boring machines, ship loaders/unloaders, offshore cranes, winches.
Material Handling: Rotary feeders for bulk solids, heavy-duty indexing tables, palletizers/depalletizers, large conveyor drive turntables.
Renewable Energy: Solar tracker drives (single-axis and dual-axis), pitch and yaw drives for wind turbines.
Construction & Mining: Concrete boom pumps, drilling rigs, crusher adjustments, screening equipment.
Industrial Automation: Heavy-duty robotic arms, precision turntables for machining and welding, large assembly positioners, automated storage and retrieval systems (AS/RS).
Defense & Aerospace: Radar antenna positioning, missile launcher traversal/elevation, telescope mounts, flight simulators.
Infrastructure: Bridge rotation mechanisms, dam gate operation, large valve actuators.
Specialized Manufacturing: Steel mill equipment (coilers, furnaces), paper mill rollers, printing presses.
Factors Influencing Enveloping Slewing Drive SE7 Pricing
The cost of an Enveloping Slewing Drive SE7 is determined by a complex interplay of factors:
Torque & Load Ratings: Higher required torque capacity and load ratings (radial, axial, moment) necessitate larger gears, bearings, and housings, significantly increasing material costs and manufacturing complexity.
Size & Configuration: Physical dimensions (diameter, height) and specific mounting configurations (flange type, shaft outputs) impact material usage and machining requirements.
Precision Requirements: Ultra-low backlash specifications demand significantly tighter manufacturing tolerances and more sophisticated grinding/finishing processes, driving up cost.
Materials & Heat Treatment: The use of premium alloy steels and specialized heat treatment processes (like case hardening, induction hardening) for enhanced strength and wear resistance adds cost.
Bearing Type & Quality: High-precision, large-capacity bearings (especially crossed roller bearings) are a major cost component. Sealing requirements also influence bearing selection and cost.
Sealing Specifications: The level of ingress protection (IP rating) required dictates the complexity and quality of the sealing system. Extreme environment sealing (e.g., for subsea or highly abrasive dust) is costly.
Lubrication System: Standard grease filling is common, but requirements for centralized lubrication systems, specific high-performance lubricants, or special lubrication intervals add cost.
Customization: Modifications from standard catalog offerings (special mounting flanges, shaft extensions, coatings, custom gear ratios, unique environmental protection) incur engineering and manufacturing overheads.
Quantity: Economies of scale apply; unit costs decrease for larger production runs.
Supplier Expertise & Reputation: Manufacturers with proven expertise in high-precision enveloping drives, rigorous quality control (ISO certifications), and a strong reputation for reliability command a premium reflecting the value of guaranteed performance and reduced downtime risk.
Supplier of the Enveloping Slewing Drive SE7
LYRADRIVE stands as a leading global engineering specialist focused on the design, development, and manufacturing of high-performance rotary drive solutions, including the advanced Enveloping Slewing Drive SE7 series. Leveraging deep expertise in gear technology, materials science, and precision engineering, LYRADRIVE delivers robust and reliable SE7 units tailored to meet the specific torque, load, precision, and environmental demands of the most challenging industrial applications worldwide. Their commitment to quality, rigorous testing protocols, and application engineering support ensures customers receive optimal drive solutions backed by technical proficiency