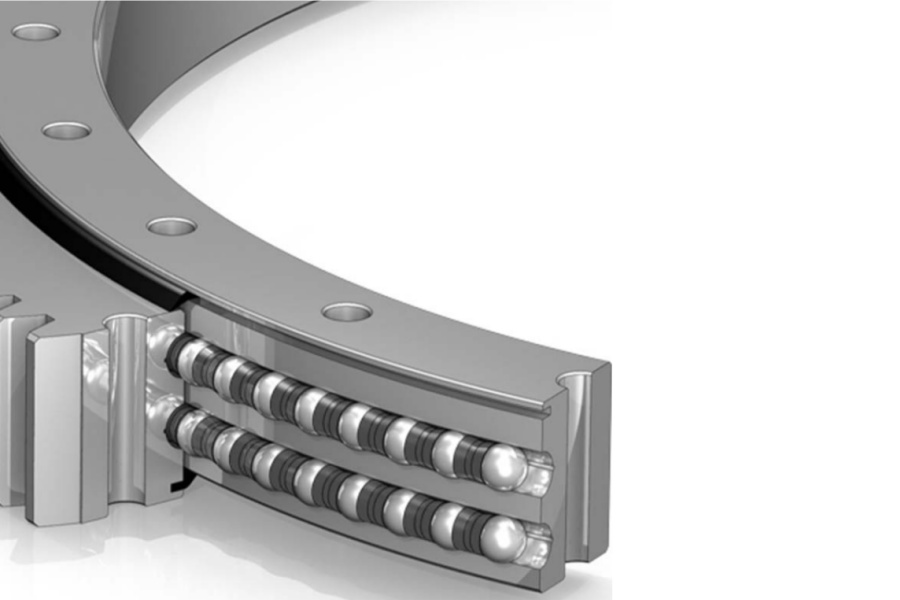
Double Row Ball Slewing Ring Bearings: The Heavy-Duty Powerhouse for Demanding Rotation
What is a Double Row Ball Slewing Ring Bearing?
A Double Row Ball Slewing Ring Bearing is a large-diameter, low-profile rolling-element bearing specifically engineered to handle combined loads – significant axial (thrust), radial, and tilting moment forces – simultaneously. Its defining characteristic is the presence of two concentric rows of balls running in dedicated raceways machined into the inner and outer rings. This dual-row configuration is the key to its superior load-bearing capabilities compared to single-row designs. The balls are typically guided by cages to ensure proper spacing and minimize friction. Precision-ground raceways and hardened rings ensure smooth operation and extended service life, even under substantial stress. These bearings are designed for slow rotational speeds or oscillatory movements rather than high-speed rotation.
The Critical Role of Pitch Bearings
While our focus is on Double Row Ball Slewing Rings, understanding their close relative, the pitch bearing, is essential, particularly in wind energy. Pitch bearings are a specialized type of slewing ring bearing used exclusively in wind turbines. They are mounted between each rotor blade and the hub. Their primary function is to enable the precise pitching (rotating) of the blades around their longitudinal axis. This adjustment is critical for controlling the power output of the turbine: feathering the blades to reduce lift in high winds or storms, and optimizing the angle of attack to maximize energy capture under varying wind conditions. Pitch bearings experience complex, constantly changing loads, including enormous bending moments from the blade weight and aerodynamic forces, significant axial loads, and operational vibrations. Reliability is paramount, as failure necessitates costly and dangerous turbine downtime. While various designs exist (including crossed roller, single-row four-point contact, and double-row ball), the Double Row Ball Slewing Ring is often chosen for larger turbines due to its exceptional moment load capacity inherent in the two-row design.
Understanding Double Row Angular Contact Slewing Bearings
The term "Double Row Angular Contact Slewing Bearing" is often used interchangeably with, or as a specific descriptor for, Double Row Ball Slewing Ring Bearings. It highlights a crucial design feature: the angular contact geometry. In these bearings, the raceways for each row of balls are machined at a specific contact angle relative to the bearing axis (commonly 45° or 90°). This geometry is fundamentally different from radial ball bearings. The angular contact design is optimized to handle combined loads much more effectively than a purely radial design. Each ball transmits force along a line angled towards the bearing's axis. This configuration allows one row to primarily handle axial loads in one direction and tilting moments, while the other row handles axial loads in the opposite direction and radial loads. The synergy between the two angular contact rows creates the bearing's remarkable stability and resistance to tilting moments under heavy off-center loads. This inherent rigidity makes them indispensable in applications where structural deflection must be minimized.
Key Features and Advantages of Double Row Ball Slewing Ring Bearings
Double Row Ball Slewing Ring Bearings offer a compelling set of features that make them the preferred choice for heavy-duty applications:
Exceptional Load Capacity: The dual-row design is the primary advantage, significantly increasing capacity for axial, radial, and especially tilting moment loads compared to single-row alternatives. They excel where loads are complex and substantial.
High Rigidity and Stiffness: The two rows of balls, combined with robust ring cross-sections, create an incredibly stiff structure. This minimizes elastic deformation (deflection) under load, crucial for maintaining precision and alignment in structures like cranes, excavators, or large radar systems.
Superior Moment Load Resistance: Their design is inherently optimized to resist tilting moments, which occur when a load is applied off-center from the bearing's rotational axis. This is a critical capability in lifting equipment and rotating platforms.
Smooth and Precise Rotation: Precision manufacturing of raceways and controlled ball guidance ensures low friction torque and smooth, controlled rotation or oscillation, even under maximum load.
Compact Design for High Capacity: Despite their high load ratings, double row ball slewing rings maintain a relatively low cross-sectional height, offering an excellent strength-to-size ratio, saving valuable space in machinery design.
Versatility in Mounting: They can be designed with various mounting configurations (bolt hole patterns, pilot diameters, seals, lubrication systems) and integrated features like gear teeth (internal or external) directly on the rings.
Durability and Long Service Life: Manufactured from high-quality, hardened steel and designed for demanding environments, these bearings offer extended operational life with proper maintenance and lubrication.
Diverse Applications Demanding Double Row Ball Slewing Ring Bearings
The unique combination of high load capacity, rigidity, and moment resistance makes Double Row Ball Slewing Ring Bearings essential across numerous heavy industries:
Wind Turbines: Primarily as Pitch Bearings (as detailed earlier) and increasingly as Yaw Bearings in the nacelle base for larger turbines requiring higher moment capacity. They handle the massive, dynamic loads from the rotor and blades.
Construction Machinery: The backbone of heavy excavators, where they form the swing bearing between the upper structure (house) and the undercarriage, enabling 360-degree rotation under extreme digging and lifting loads.
Material Handling: Essential in large cranes (mobile, tower, offshore), stacker-reclaimers, and ship-to-shore cranes for slewing the boom or entire superstructure, handling immense loads at significant radii.
Mining Equipment: Used in draglines, bucket-wheel excavators, and large mining shovels for slewing functions under severe shock loads and abrasive conditions.
Industrial Robots and Automation: Found in large robotic welding cells, heavy-duty positioners, and automated assembly lines requiring high payload capacity and precise positioning.
Medical Equipment: Large imaging devices like CT scanners and radiation therapy machines utilize them for smooth, precise, and vibration-free rotation of heavy gantries.
Defense and Aerospace: Radar and satellite communication antennas, missile launchers, and gun turrets rely on their precision, rigidity, and ability to handle large moment loads.
Packaging and Printing: Large rotary platforms and indexing tables in heavy industrial printing and packaging machinery.
Test Equipment: Used in large dynamometers and structural testing rigs where applying controlled moments and forces is critical.
Factors Influencing Double Row Ball Slewing Ring Bearing Price
The cost of a Double Row Ball Slewing Ring Bearing is not a simple figure; it's influenced by a complex interplay of technical specifications and market factors:
Size and Dimensions: Diameter is the most significant driver – larger bearings require exponentially more material and complex machining. Ring cross-section height and bolt circle details also impact cost.
Load Capacity Requirements: Bearings engineered for higher axial, radial, and moment loads demand larger ball diameters, more balls, wider raceways, and thicker, higher-grade ring materials, increasing manufacturing complexity and cost.
Material Grade and Quality: The type of steel (e.g., 42CrMo4, 50Mn), its purity, and the depth and quality of hardening (induction or through) significantly affect performance, longevity, and price. Premium grades cost more.
Precision and Tolerances: Tighter manufacturing tolerances for raceway geometry, roundness, parallelism, and runout require more sophisticated machining and inspection processes, elevating costs. Accuracy classes (e.g., P5, P4) dictate this.
Gear Teeth: Incorporating precision-machined gear teeth (internal or external, spur or helical) onto one of the rings adds considerable machining time and cost. Tooth quality (profile, hardness) is critical.
Sealing Systems: High-performance sealing (multiple lip seals, labyrinth designs, specific elastomers) to exclude contaminants and retain lubrication, especially for harsh environments (offshore, mining), adds cost.
Lubrication System: Integrated lubrication channels, fittings (grease nipples, centralized ports), and potentially pre-installed lubrication require additional machining and components.
Mounting Features: Customizations like specific pilot diameters, non-standard bolt hole patterns, alignment marks, or special surface treatments add complexity.
Surface Treatments & Coatings: Corrosion protection (zinc plating, specialized paints like Geomet) or raceway surface enhancements for wear resistance increase cost.
Quality Assurance & Certification: Rigorous inspection protocols (NDT, dimensional checks, hardness testing), traceability documentation, and specific certifications (ISO, DNV GL, ABS) add administrative and testing overhead.
Quantity and Customization: Higher volumes typically reduce per-unit costs. Fully custom bearings designed from scratch are significantly more expensive than modifying standard designs or buying catalog items.
Manufacturer Expertise and Reputation: Established manufacturers with proven designs, advanced manufacturing capabilities, and robust R&D often command premium prices based on reliability and performance assurance.
Raw Material Costs and Logistics: Fluctuations in steel prices and transportation costs impact the final price.
Supplier of Double Row Ball Slewing Ring Bearing
Choosing the right supplier for Double Row Ball Slewing Ring Bearings is as critical as the bearing design itself. These are complex, mission-critical components where failure can lead to catastrophic downtime and immense costs. LYRADRIVE stands as a premier partner in this demanding field. We distinguish ourselves through:
Deep Engineering Expertise: Our team possesses profound knowledge of slewing bearing mechanics, metallurgy, and application demands. We don't just sell bearings; we provide engineered solutions.
Advanced Manufacturing Capabilities: Utilizing state-of-the-art CNC machining centers, precision gear cutting equipment, and controlled heat treatment processes, we ensure consistent, high-quality production meeting stringent tolerances.
Robust Quality Management: Adherence to ISO 9001 standards is foundational. Our comprehensive quality control includes rigorous material inspection, in-process checks, final dimensional verification, non-destructive testing (NDT), and thorough load testing simulations to guarantee performance and longevity.
Material Excellence: We source only high-grade, traceable bearing steels and subject them to precisely controlled hardening processes to achieve optimal core toughness and raceway surface hardness for maximum fatigue life and wear resistance.
Customization Prowess: LYRADRIVE excels in designing and manufacturing bespoke double row ball slewing rings. We work collaboratively with clients to tailor dimensions, load ratings, sealing systems, gear specifications, lubrication setups, and mounting features to perfectly integrate into your specific application.
Application Focus: With extensive experience across key sectors like wind energy (pitch & yaw), heavy construction, mining, and material handling, we understand the unique challenges and design bearings to withstand them.
Global Support & Logistics: We provide responsive technical support throughout the project lifecycle, from design consultation to installation guidance and maintenance recommendations, backed by efficient global logistics.
Competitive Value: While focused on premium quality and performance, LYRADRIVE strives for efficient manufacturing and competitive pricing, delivering exceptional long-term value through bearing reliability and reduced total cost of ownership.
Conclusion
Double Row Ball Slewing Ring Bearings are indispensable engineering solutions where immense loads, challenging moments, and the need for rigid, reliable rotation converge. Their dual-row angular contact design delivers unparalleled capacity and stability, powering everything from the giants of renewable energy harvesting to the titans of construction and mining. Understanding their design principles, capabilities, and the factors influencing their cost is crucial for optimal application selection. Partnering with a technically proficient and reliable manufacturer like LYRADRIVE ensures access to bearings engineered for peak performance, durability, and seamless integration, ultimately driving operational efficiency and minimizing downtime in the world's most demanding machinery. When the application demands the ultimate in load handling and rotational integrity, the Double Row Ball Slewing Ring Bearing stands as the proven heavy-duty powerhouse.