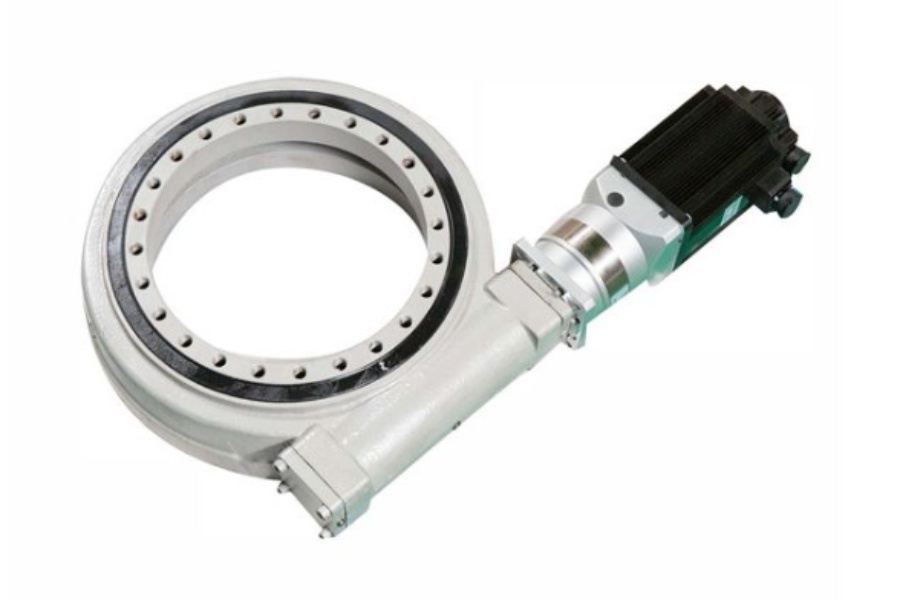
What is Truck Crane Slewing Drive
What is a Truck Crane Slewing Drive?
A Truck Crane Slewing Drive is a heavy-duty rotational mechanism integrated into mobile crane systems mounted on trucks, designed to enable precise 360-degree rotation of the crane’s boom and load under varying operational conditions. This critical component combines a robust slewing ring bearing with a gear system—typically worm or planetary gears—to manage axial, radial, and moment loads while ensuring smooth and controlled movement during lifting, positioning, or material handling tasks. Engineered for durability and reliability, the slewing drive allows operators to maneuver heavy loads with accuracy, even in challenging environments such as construction sites, industrial facilities, or emergency response scenarios. Its ability to withstand dynamic forces, including wind resistance, sudden load shifts, and repetitive start-stop cycles, makes it indispensable for ensuring operational safety and efficiency in mobile crane applications.
Types of Truck Crane Slewing Drives
Truck Crane Slewing Drives are categorized based on their gear systems, load capacities, and adaptability to specific operational demands. Worm Gear Slewing Drives utilize a worm and wheel configuration to provide self-locking functionality, preventing unintended boom movement during power loss or mechanical failure, making them ideal for applications requiring high positional stability, such as precision lifting in congested urban areas. Planetary Gear Slewing Drives employ a compact planetary gearbox to deliver higher torque density and efficiency, suited for cranes requiring rapid rotation speeds or frequent directional changes, such as material handling in logistics yards or assembly lines. Hollow Shaft Slewing Drives feature a central bore to accommodate hydraulic lines or electrical cables, streamlining the crane’s design by reducing external clutter and enhancing maintenance accessibility. Sealed Slewing Drives are constructed with IP67+ ratings and corrosion-resistant materials to withstand harsh environments like coastal regions or chemical plants, where exposure to moisture, salt, or abrasive particles is common. Customized Hybrid Drives combine multiple gear types or integrate advanced features like IoT sensors for real-time load monitoring, catering to specialized tasks such as heavy infrastructure projects or disaster recovery operations.
Key Features of Truck Crane Slewing Drives
The performance of Truck Crane Slewing Drives hinges on several advanced features tailored to the rigorous demands of mobile crane operations. High Torque Capacity ensures the drive can handle extreme loads, often exceeding 100 tons, while maintaining smooth rotation and precise control during lifting or positioning tasks. Safety Mechanisms, including redundant braking systems and anti-backlash gears, prevent accidental movement or load slippage, critical for ensuring operator and worksite safety. Durability Enhancements such as hardened steel gears, forged raceways, and multi-stage sealing systems protect internal components from wear, contamination, and environmental damage, extending service life in demanding conditions. Compact and Modular Designs allow seamless integration into the crane’s structure without compromising the truck’s mobility or payload capacity. Adaptive Lubrication Systems ensure consistent grease distribution across gears and bearings, even under high-speed or high-stress conditions, minimizing friction and overheating. Precision Engineering with minimal backlash (typically under 3 arc-minutes) enables operators to position loads with millimeter accuracy, essential for tasks like placing structural beams or handling delicate equipment.
Applications of Truck Crane Slewing Drives
Truck Crane Slewing Drives are indispensable across industries that rely on mobile lifting solutions for complex tasks. In construction, they facilitate the precise placement of steel beams, concrete panels, or prefabricated modules during building projects, often in tight urban spaces with limited maneuverability. Infrastructure Development teams use them to install utility poles, bridge components, or railway tracks, where stability and accuracy are paramount. Emergency Services deploy truck cranes equipped with these drives for disaster recovery operations, such as clearing debris after storms or rescuing stranded vehicles. Industrial Maintenance crews rely on them to lift and position heavy machinery, turbines, or storage tanks during repair or replacement tasks. Logistics and Warehousing operations utilize slewing drives to handle oversized cargo, containers, or manufacturing equipment in ports or distribution centers. Even renewable energy projects, such as wind turbine installations or solar farm construction, depend on their ability to manage heavy, irregularly shaped loads in remote or challenging terrains.
Price Range
The cost of a Truck Crane Slewing Drive varies significantly based on design complexity, load capacity, and customization requirements. Standard Worm Gear Drives for mid-sized cranes with moderate lifting capacities typically range from 15,000 to 40,000, offering a balance of performance and affordability for general-purpose applications. Planetary Gear Drives designed for high-torque or high-speed operations, such as heavy-duty industrial cranes, may cost between 30,000 and 80,000, depending on gear ratios, material quality, and additional features like integrated sensors. Custom-Built Solutions, including corrosion-resistant models for marine environments or explosion-proof designs for hazardous sites, can exceed $100,000, particularly when incorporating advanced alloys, IoT connectivity, or specialized coatings. Bulk procurement agreements for fleet operators often reduce per-unit costs by 10–20%, while expedited production timelines or rare material requests (e.g., titanium components) may increase prices by 25–50%.
Lifespan of Truck Crane Slewing Drives
Operational longevity depends on usage patterns, maintenance rigor, and environmental conditions. In moderate-duty applications like urban construction or periodic industrial use, these drives typically last 10–15 years with biannual lubrication, alignment inspections, and seal replacements. Heavy-Duty Scenarios, such as 24/7 port operations or mining projects, may reduce lifespan to 7–12 years due to constant high-stress cycles, necessitating quarterly maintenance and proactive component upgrades. Extreme Environments, including offshore oil rigs or coastal regions with saltwater exposure, can shorten service life to 5–8 years, even with advanced protective measures like stainless steel housings or triple-lip seals. Key factors for maximizing longevity include adhering to load limits (operating below 85% of maximum capacity), using manufacturer-recommended high-viscosity lubricants, and ensuring precise installation alignment to prevent uneven wear on gears and bearings.
How to Choose the Right Truck Crane Slewing Drive
Selecting the optimal slewing drive requires a thorough evaluation of technical specifications and operational demands. Assess Load Requirements by calculating combined axial, radial, and moment forces, factoring in dynamic elements like wind loads, sudden movements, or uneven weight distribution, and apply a safety factor of 1.5–2x to account for unpredictable stresses. Prioritize Safety and Compliance by choosing drives with certifications like ISO 4301 or FEM 1.001 for crane applications, ensuring adherence to industry safety standards. Evaluate Environmental Conditions—opt for IP68-rated sealed drives with corrosion-resistant coatings in marine or chemically aggressive settings, while standard models suffice for controlled indoor environments. Consider Space and Weight Constraints: Compact planetary gear drives or hollow shaft designs optimize space in truck-mounted systems, whereas flange-mounted units provide stability for vertical lifting tasks. Partner with Experienced Suppliers who offer technical support, customization options, and documentation such as load-test reports or material traceability certificates. Analyze Total Cost of Ownership by balancing initial expenses with long-term reliability—investing in premium drives with predictive maintenance features may reduce downtime and repair costs over time.
Common Mistakes to Avoid
Underestimating Dynamic Loads, such as ignoring wind forces or sudden load shifts, leads to premature gear wear or catastrophic system failure. Neglecting Environmental Protections in coastal or industrial areas results in rapid corrosion and component degradation—always specify marine-grade materials or advanced seals for harsh conditions. Improper Lubrication Practices, such as using incorrect grease types or skipping scheduled maintenance, accelerates friction and overheating, shortening drive lifespan. Overlooking Alignment Precision during installation causes uneven stress distribution and accelerated wear—use laser alignment tools and adhere to manufacturer torque specifications for mounting bolts. Choosing Generic Drives for Specialized Tasks, such as using standard models in explosive atmospheres, compromises safety and regulatory compliance. Prioritizing Initial Cost Over Quality often backfires, as budget drives may lack durability certifications or critical safety features, increasing long-term operational risks.
Truck Crane Slewing Drive Supplier
LYRA Drive is a professional slewing bearings ,slew drive and gears manufacturer provides customized slew bearing, drive and gears.For application-specific engineering solutions, contact LYRA to discuss technical specifications and implementation strategies.