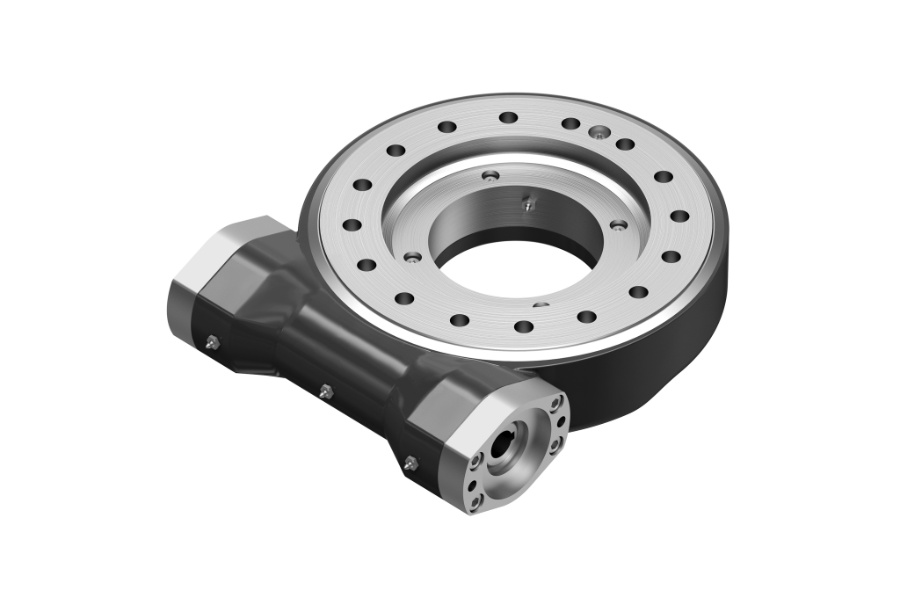
What is SP-H Slew Drive
What is an SP-H Slew Drive?
An SP-H Slew Drive is a heavy-duty rotational mechanism engineered to deliver exceptional torque and precision in the most demanding industrial applications, combining a rugged slewing ring bearing with an advanced gear system—typically utilizing hardened spur or planetary gears. The "SP-H" designation often signifies a series optimized for high-load capacity, extreme environmental resistance, and modular adaptability, distinguishing it from standard or lighter-duty slew drives. These drives are designed to handle extreme axial, radial, and moment loads simultaneously while maintaining smooth 360-degree rotation, making them indispensable for applications such as offshore cranes, mining excavators, or wind turbine pitch systems where reliability under stress is non-negotiable. SP-H models frequently incorporate innovations like multi-stage sealing, forged alloy components, or integrated thermal management systems to ensure performance in harsh conditions like saltwater immersion, abrasive dust, or sub-zero temperatures.
Types of SP-H Slew Drives
SP-H Slew Drives are categorized based on their gear configurations, structural reinforcements, and specialized adaptations for extreme environments. The planetary gear SP-H Slew Drive employs a compact planetary gearbox to achieve high torque density and efficiency, ideal for heavy machinery like tunnel boring machines or offshore winches requiring relentless power transmission. Spur gear SP-H Slew Drives use robust straight-cut gears for simplicity and cost-effectiveness in applications like bulk material handling systems or agricultural machinery where shock loads are common. Hollow shaft SP-H Slew Drives feature a central bore for integrated hydraulic or electrical line routing, critical in offshore drilling rigs or automated port cranes where space optimization and clutter-free operation are paramount. For corrosive environments, sealed SP-H Slew Drives with IP69K ratings and duplex stainless steel coatings resist saltwater, acidic fumes, or high-pressure washdowns, commonly used in marine vessels or chemical processing plants. Customizable SP-H Slew Drives offer tailored solutions such as split housings for field repairs or hybrid gear systems combining spur and planetary gears for unique torque-speed requirements in aerospace launch platforms or deep-sea robotics.
Key Features of SP-H Slew Drives
SP-H Slew Drives stand out for their unmatched durability and adaptability to extreme conditions. Precision-forged gears with case-hardened surfaces ensure minimal backlash (often under 2 arc-minutes), critical for applications like radar systems or precision machining tools where positional accuracy directly impacts outcomes. The use of ultra-durable materials—such as titanium-reinforced gears and fluoropolymer seals—extends service life even under continuous exposure to extreme temperatures (-50°C to 200°C) or corrosive substances. Modular construction allows for rapid component replacement, minimizing downtime in remote or hazardous environments like oil rigs or mining sites. Integrated sensor hubs enable real-time monitoring of parameters like vibration, load distribution, and temperature, facilitating predictive maintenance and reducing unplanned outages. Additionally, adaptive lubrication systems automatically adjust grease viscosity based on operational demands, ensuring optimal performance in both high-speed and high-torque scenarios.
Applications of SP-H Slew Drives
SP-H Slew Drives are pivotal in industries where failure is not an option. In offshore energy, they rotate drilling platforms and adjust wind turbine nacelles in storm-prone seas, leveraging their corrosion resistance and load-bearing prowess. Mining and construction rely on these drives for colossal excavators and tunnel boring machines, where their ability to endure shock loads and abrasive dust ensures uninterrupted operation. Aerospace and defense applications include missile turrets and satellite deployment mechanisms, where precision and resistance to extreme temperatures are critical. Marine technology utilizes SP-H Drives in ship-to-shore cranes and subsea ROVs (remotely operated vehicles), while heavy manufacturing integrates them into steel rolling mills or forging presses for consistent, high-torque performance. Even disaster response equipment, such as heavy-lift drones or debris-clearing robots, benefits from their rugged design in unpredictable environments.
Price Range
The cost of an SP-H Slew Drive varies widely based on size, complexity, and customization. Entry-level models for industrial machinery or large-scale agricultural equipment start around 20,000–50,000. Mid-range units designed for offshore wind turbines or mining excavators typically range from 70,000–150,000, influenced by torque ratings (e.g., 100,000–500,000 Nm) and material upgrades like titanium alloys or marine-grade coatings. High-end custom drives for aerospace, defense, or subsea applications can exceed $300,000, particularly when incorporating features like explosion-proof housings, IoT-enabled diagnostics, or ultra-high-precision gears. Bulk orders or long-term partnerships with suppliers may reduce costs by 10–15%, while expedited production or exotic material sourcing (e.g., ceramic matrix composites) can add 30–60% to the price.
Lifespan of SP-H Slew Drives
The operational lifespan of an SP-H Slew Drive hinges on usage intensity, environmental severity, and maintenance discipline. In moderately demanding applications like offshore wind farms or periodic heavy manufacturing, these drives can operate efficiently for 15–25 years with biannual lubrication, alignment checks, and seal replacements. Extreme-duty use in 24/7 mining operations or deep-sea exploration typically results in a lifespan of 8–12 years, assuming quarterly inspections and proactive replacement of worn components. Harsh environments—such as Arctic drilling sites or coastal salt spray zones—may shorten longevity to 6–10 years, even with advanced protective measures. Key factors include strict adherence to load limits (operating below 90% of maximum capacity), using manufacturer-specified high-pressure lubricants, and ensuring laser-precise installation alignment to prevent uneven gear wear.
How to Choose the Right SP-H Slew Drive
Selecting the optimal SP-H Slew Drive demands a meticulous assessment of operational needs and environmental challenges. Begin by quantifying load requirements—calculate axial, radial, and moment loads using finite element analysis (FEA) or industry-standard formulas, then apply a safety factor of 2x for applications involving shock loads or dynamic forces. For extreme environments, prioritize sealed drives with IP69K ratings, corrosion-resistant alloys, and thermal management systems to handle temperature extremes. High-torque applications like mining or offshore equipment require planetary gear configurations, while spur gear models suffice for moderate-speed, high-impact scenarios like forestry machinery.
Evaluate spatial and weight constraints—modular hollow shaft designs simplify integration into compact systems like underwater robotics, while flange-mounted units provide stability for vertical load applications like tower cranes. Material selection is critical: duplex stainless steel suits marine environments, while titanium alloys are ideal for aerospace weight savings. Partner with suppliers offering domain-specific expertise (e.g., subsea engineering or defense) and demand certifications like DNV-GL compliance or MIL-SPEC testing reports. Finally, analyze total cost of ownership—premium models with predictive maintenance features may have higher upfront costs but significantly reduce lifecycle expenses through minimized downtime and repairs.
Common Mistakes to Avoid
A critical error is underestimating environmental factors—deploying unsealed drives in saltwater or chemically aggressive environments leads to rapid corrosion and catastrophic failure. Improper alignment during installation—even a 0.1mm deviation—causes uneven gear stress, drastically shortening lifespan; always use laser alignment tools and follow torque specifications rigorously. Using generic lubricants instead of high-temperature, extreme-pressure greases accelerates wear and voids warranties. Overloading the drive beyond 90% of its rated capacity strains components, leading to premature gear pitting or bearing failure.
Mismatching materials—such as pairing stainless steel gears with aluminum housings without anti-galvanic treatments—risks electrochemical corrosion in humid conditions. Assuming all SP-H Slew Drives are interchangeable across industries is another pitfall—a drive designed for slow, high-torque mining rigs won’t perform in high-speed aerospace applications. Lastly, neglecting predictive maintenance—such as ignoring vibration sensor data—can turn minor issues into costly breakdowns.
SP-H Slew Drive Supplier
LYRA Drive is a professional slewing bearings ,slew drive, slewdrives and gears manufacturer provides customizedslew bearing, drive and gears.For application-specific engineering solutions, contact LYRA to discuss technical specifications and implementation strategies.