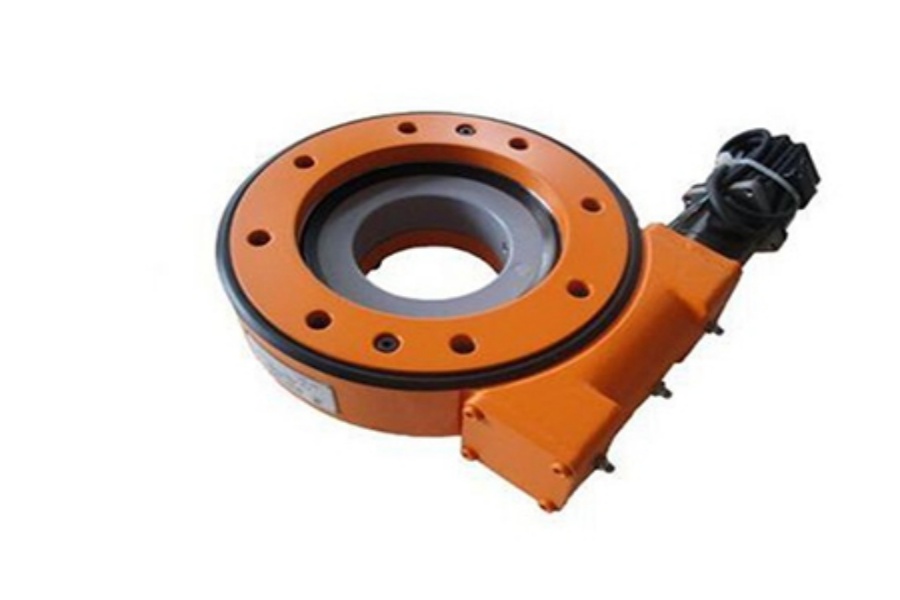
What is Aerial Work Vehicle Slew Drive
What is an Aerial Work Vehicle Slew Drive?
An Aerial Work Vehicle Slew Drive is a precision-engineered rotational mechanism designed to enable controlled 360-degree movement in aerial work platforms, such as boom lifts, cherry pickers, or telescopic handlers, ensuring operators can safely and accurately position personnel, tools, or materials at elevated heights. This critical component integrates a robust slewing ring bearing with a gear system—typically worm or planetary gears—to handle dynamic loads and environmental stresses encountered in construction, utility maintenance, or emergency response scenarios. By combining high torque capacity with smooth rotational control, these drives provide the stability and reliability required for tasks ranging from window washing on skyscrapers to repairing power lines in challenging weather conditions, making them indispensable for industries that prioritize safety and operational efficiency in aerial operations.
Types of Aerial Work Vehicle Slew Drives
Aerial Work Vehicle Slew Drives are categorized based on their mechanical design, load-handling capabilities, and environmental adaptability. Worm gear slew drives utilize a worm and wheel configuration to offer self-locking functionality, preventing unintended platform movement during power loss or mechanical failure, making them ideal for boom lifts and telescopic handlers where safety is paramount. Planetary gear slew drives employ a compact planetary gearbox to deliver higher torque density and efficiency, suited for applications requiring rapid rotation, such as rotating platforms in firefighting vehicles or high-speed scissor lifts. Hollow shaft slew drives feature a central bore for routing hydraulic lines or electrical cables, streamlining design in aerial platforms where space optimization and clutter-free operation are essential. Sealed slew drives, built with IP67+ ratings and corrosion-resistant materials, withstand harsh outdoor environments like coastal regions or industrial sites exposed to moisture, dust, and chemical agents. Hybrid designs combine worm and planetary gears to balance torque and speed for specialized tasks, such as heavy-material handling platforms or rescue vehicles requiring both power and precision.
Key Features of Aerial Work Vehicle Slew Drives
These drives are distinguished by their ability to deliver reliability and precision under demanding conditions. High load capacity ensures they can manage dynamic forces from personnel, equipment, and environmental factors like wind or vibration, often supporting weights exceeding 1,000 kg while maintaining smooth rotation. Safety mechanisms such as self-locking gears or redundant braking systems prevent accidental movement, critical for platforms used in human occupancy or hazardous environments. Weather-resistant construction includes sealed housings, stainless steel components, and UV-resistant coatings to protect against rain, dust, saltwater, and temperature extremes, ensuring longevity in outdoor or marine settings. Compact designs optimize space within the aerial platform’s structure without compromising strength, while low-maintenance features like lubricated-for-life systems or easy-access grease ports minimize downtime. Precision control with minimal backlash (under 5 arc-minutes) allows operators to position platforms with millimeter accuracy, essential for tasks like structural inspections or delicate repairs.
Applications of Aerial Work Vehicle Slew Drives
Aerial Work Vehicle Slew Drives are essential across industries requiring elevated access and maneuverability. In construction, they enable workers to rotate platforms for installing façade panels, welding steel beams, or painting high-rise structures with precision. Utility maintenance crews rely on them to position technicians repairing power lines, streetlights, or cellular towers, often in challenging weather or terrain. Firefighting vehicles use these drives to orient water cannons or rescue platforms during emergencies, ensuring rapid response and stability in life-threatening scenarios. Film production teams utilize them to stabilize camera operators on telescopic booms for aerial cinematography, capturing smooth footage in dynamic environments. Warehouse automation systems integrate slew drives into rotating platforms for inventory retrieval at heights, enhancing efficiency in logistics operations. Even municipal services, such as tree trimming or bridge inspections, depend on their reliability to complete tasks safely and efficiently.
Price Range
The cost of an Aerial Work Vehicle Slew Drive varies significantly based on design complexity, load capacity, and environmental specifications. Standard worm gear drives for mid-sized aerial platforms with moderate load requirements typically range from 5,000 to 15,000, offering a balance of safety and affordability. Planetary gear drives designed for high-speed or high-torque applications, such as firefighting turrets or industrial scissor lifts, may cost between 10,000 and 25,000, depending on torque ratings and material upgrades. Customized solutions, including explosion-proof designs for hazardous environments or ultra-compact units for confined spaces, can exceed $50,000, particularly when incorporating advanced materials like titanium alloys or IoT-enabled sensors for real-time diagnostics. Bulk purchasing agreements for fleet operators often reduce per-unit costs by 10–15%, while expedited manufacturing or specialized coatings for extreme conditions may increase prices by 20–30%.
Lifespan of Aerial Work Vehicle Slew Drives
Operational longevity depends on usage intensity, maintenance practices, and environmental exposure. In moderate-use scenarios like urban construction or utility maintenance, these drives typically last 10–15 years with biannual lubrication, alignment checks, and seal replacements. Heavy-duty applications such as firefighting or 24/7 industrial use may reduce lifespan to 7–12 years due to frequent high-stress cycles, necessitating quarterly inspections and proactive component replacements. Harsh environments like offshore oil rigs or coastal regions with salt spray and humidity can shorten service life to 5–8 years, even with advanced sealing and corrosion-resistant materials. Key factors for maximizing lifespan include adhering to load limits (operating below 80% of maximum capacity), using manufacturer-recommended high-pressure lubricants, and ensuring precise installation alignment to prevent uneven wear on gears and bearings.
How to Choose the Right Aerial Work Vehicle Slew Drive
Selecting the optimal drive requires a comprehensive evaluation of technical and operational needs. Begin by calculating combined axial, radial, and moment loads, factoring in dynamic forces like wind resistance or sudden movements, and apply a safety margin of 1.5x to accommodate unexpected stresses. Prioritize safety features such as self-locking gears or redundant braking systems for platforms used in human-inhabited or high-risk environments. Assess environmental challenges—opt for IP67+ sealed drives with stainless steel components in coastal or chemically aggressive settings, while standard models suffice for controlled indoor use. Consider spatial constraints: hollow shaft designs simplify cable management in compact platforms, while flange-mounted units provide stability for vertical loads. Partner with suppliers with proven expertise in aerial equipment certifications (e.g., ANSI, OSHA compliance) and request documentation like load-test reports or material certifications. Evaluate total cost of ownership by weighing upfront expenses against long-term reliability—premium drives with predictive maintenance capabilities may justify higher initial costs through reduced downtime and repair frequency.
Common Mistakes to Avoid
Underestimating dynamic load calculations, such as ignoring wind forces or sudden shifts in platform weight, leads to premature wear or catastrophic failure. Deploying non-explosion-proof drives in flammable environments risks safety violations and operational hazards. Neglecting alignment precision during installation causes uneven gear stress and accelerated wear—always use laser alignment tools and adhere to manufacturer torque specifications. Skipping lubrication schedules or using incompatible greases increases friction and overheating, degrading performance and voiding warranties. Overlooking corrosion protection in coastal or industrial settings results in rapid component degradation, necessitating costly replacements. Prioritizing low-cost options over certified, quality-assured drives compromises safety and reliability, endangering operators and increasing long-term expenses.
Aerial Work Vehicle Slew Drive Supplier
LYRA Drive is a professional slewing bearings ,slew drive and gears manufacturer provides customized slew bearing, drive and gears.For application-specific engineering solutions, contact LYRA to discuss technical specifications and implementation strategies.