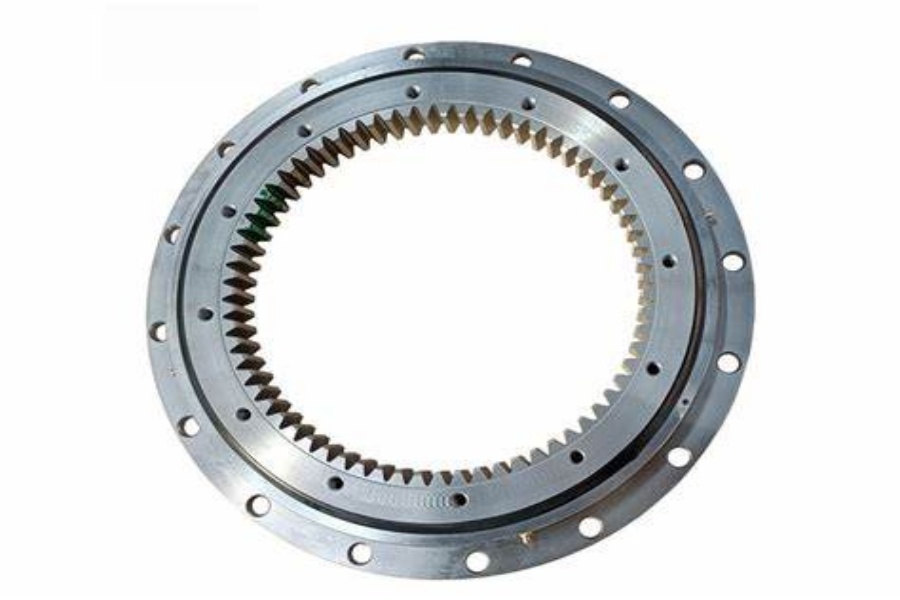
The Versatile Power of Flanged Ball Slewing Bearings in Modern Machinery
In the intricate landscape of industrial machinery where precision rotation and load management are paramount, Flanged Ball Slewing Bearings have emerged as indispensable components enabling seamless movement across diverse applications. These bearings facilitate everything from the precise rotation of medical imaging equipment to the robust pivoting of construction cranes, combining structural ingenuity with operational efficiency. This article delves into how Flanged Ball Slewing Bearings enhance performance by offering robust load handling, simplified installation, and adaptability in demanding environments.
What is a Flanged Ball Slewing Bearings
Flanged Ball Slewing Bearings are specialized rotational assemblies designed to manage combined axial, radial, and moment loads while enabling smooth 360-degree rotation. Distinguished by an integrated flange—a protruding rim on one or both rings—these bearings provide a secure mounting surface that simplifies attachment to machinery. The flange design eliminates the need for additional mounting plates or adapters, making them ideal for applications like robotic arms, wind turbine pitch systems, or industrial turntables where space optimization and quick installation are critical. Their single or double row ball bearing configuration balances load capacity with compactness, catering to systems requiring moderate to heavy load handling without compromising rotational precision.
How Flanged Ball Slewing Bearings Operate
Imagine a tower crane rotating heavy materials across a construction site or a solar tracker adjusting panels to follow the sun’s path. At the core of these movements lies the Flanged Ball Slewing Bearing. The bearing’s inner ring, often flanged, bolts directly to a stationary base, while the outer ring connects to the rotating component. Precision-engineered ball bearings, housed within raceways, distribute loads evenly as the outer ring turns. The integrated flange provides a rigid mounting interface, ensuring alignment stability and reducing stress on fasteners. Preload adjustments during assembly eliminate free play, enabling smooth, vibration-free rotation—essential for applications like radar antennas or automated assembly lines where even minor misalignment disrupts accuracy.
Key Features and Advantages of Flanged Ball Slewing Bearings
Flanged Ball Slewing Bearings distinguish themselves through structural versatility and engineered durability. Their flanged design streamlines installation, allowing direct mounting to machinery surfaces without brackets—a game-changer for retrofitting older equipment or assembling modular systems. A standout feature is their high rigidity, achieved through hardened raceways and precision-ground balls, which minimizes deflection under asymmetrical loads common in crane booms or excavator attachments.
Unlike plain bearings requiring frequent lubrication, many flanged variants come pre-packed with high-performance grease and feature triple-lip seals that repel contaminants in harsh environments like mining or marine applications. The availability of custom bolt patterns on the flange allows tailored integration into existing machinery, reducing design overhaul costs. Additionally, their modularity supports easy replacement in field repairs, slashing downtime in industries like offshore energy or material handling.
Space efficiency is another hallmark. By consolidating mounting and rotational functions into a single unit, these bearings reduce system footprint—critical for mobile equipment like cherry pickers or compact robotic cells. Despite their streamlined profile, they handle impressive loads, with some models supporting axial forces exceeding 100 tons, a capability leveraged in tunnel boring machines or shipyard gantries.
Applications Across Industries
Flanged Ball Slewing Bearings excel in sectors demanding reliable rotation under load:
Construction and Heavy Machinery
In tower cranes, these bearings enable smooth 360-degree rotation while supporting massive loads. Their sealed designs withstand dust and debris on construction sites, ensuring longevity despite abrasive conditions.
Renewable Energy
Wind turbine pitch and yaw systems utilize flanged bearings to adjust blade angles and nacelle orientation. Corrosion-resistant variants endure salt spray in offshore installations, maintaining performance through decades of service.
Medical Equipment
CT scanners and MRI machines rely on these bearings for silent, precise rotation. The flange’s rigidity prevents vibration, ensuring high-resolution imaging critical for diagnostics.
Automation and Robotics
Automated welding cells and packaging lines employ flanged bearings to rotate end-effectors with micron-level accuracy. Custom bolt patterns allow seamless integration into robotic arms, enhancing production speed and consistency.
Performance Enhancements Delivered
Integrating Flanged Ball Slewing Bearings elevates system capabilities in measurable ways:
Enhanced Load Stability
The flange’s rigid mounting surface distributes stress evenly, preventing localized deformation. In steel rolling mills, this stability ensures consistent sheet thickness by maintaining roller alignment under extreme pressures.
Reduced Installation Time
Pre-drilled flange holes and standardized bolt patterns cut assembly time by up to 40% compared to traditional bearing setups. Mobile crane manufacturers benefit from rapid on-site installations, accelerating project timelines.
Energy Efficiency
Low-friction designs incorporating advanced greases reduce torque requirements, lowering energy consumption in solar trackers by 15-25% compared to bushing-based systems.
Extended Service Life
Hardened steel components and multi-layered seals extend bearing lifespan in abrasive environments. For example, mining conveyor systems using these bearings report 50% longer service intervals than those using unsealed alternatives.
Common Pitfalls to Avoid
Even robust bearings require informed handling to maximize performance:
Ignoring Mounting Surface Flatness: Uneven mounting surfaces induce stress concentrations. Always machine mating surfaces to specified tolerances and use alignment pins during installation.
Mismatching Lubricants: Substituting standard grease for high-temperature variants in kiln applications accelerates wear. Follow manufacturer guidelines for lubricant compatibility.
Over-Torquing Fasteners: Excessive bolt tension warps the flange, causing uneven load distribution. Use torque wrenches and follow recommended tightening sequences.
Neglecting Environmental Seals: In food processing plants, failing to specify FDA-approved seals leads to contamination risks during washdowns.
Flanged Ball Slewing Bearings supplier
LYRA Drive is a professional slewing bearings ,slew drive and gears manufacturer provides customized slew bearing, drive and gears.For application-specific engineering solutions, contact LYRA to discuss technical specifications and implementation strategies.