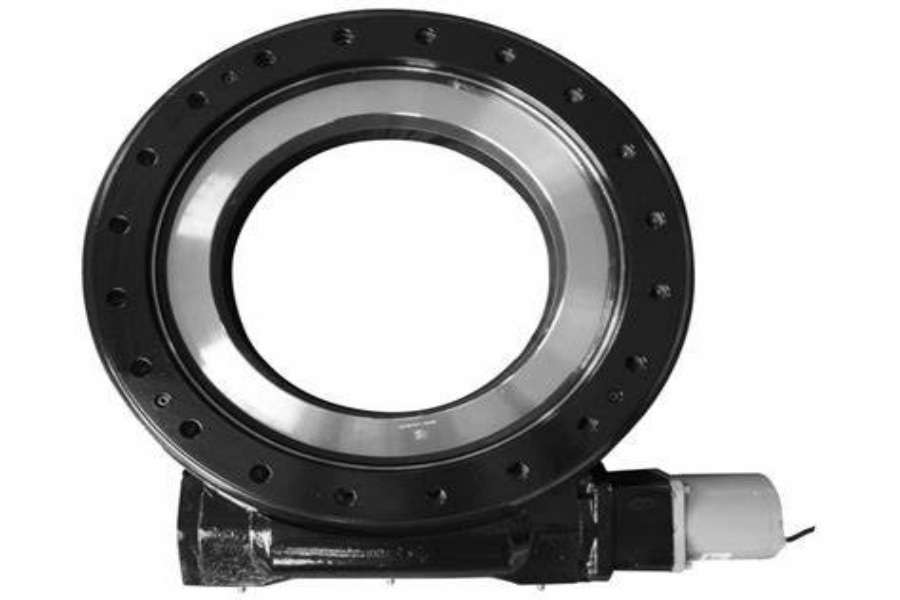
Double Worm Slew Drive Powering Heavy-Duty Precision in Modern Industry
In the demanding world of industrial machinery where torque reliability and positional accuracy are non-negotiable, Double Worm Slew Drives have emerged as a cornerstone technology for systems requiring fail-safe operation under extreme loads. These robust transmission units enable everything from solar farms tracking the sun with military precision to offshore cranes lifting multi-ton cargo in stormy seas. This article explores how Double Worm Slew Drives combine brute strength with intelligent design to deliver unparalleled performance in applications where downtime is not an option.
What is a Double Worm Slew Drives
A Double Worm Slew Drive is an advanced rotational power transmission system featuring two parallel worm gear sets working in tandem to drive a central slewing ring. This dual-worm configuration provides built-in redundancy and torque multiplication capabilities, making it ideal for mission-critical applications like radar antenna positioning, tunnel boring machines, or heavy-duty welding positioners. Unlike single-worm designs, the twin worm arrangement ensures continuous operation even if one gear set experiences issues—a critical safety feature for equipment operating in remote or hazardous environments. The system’s ability to handle extreme axial and radial loads while maintaining precise angular control makes it indispensable for industries prioritizing operational continuity and precision.
How Double Worm Slew Drives Operate
Imagine a solar power plant where thousands of panels must follow the sun’s arc within 0.1-degree accuracy or a ship-to-shore crane transferring containers during gale-force winds. The Double Worm Slew Drive makes such feats possible through its unique dual-input design. Two hardened steel worm screws engage with a large diameter worm wheel integrated into the slewing ring’s outer race. When synchronized motors drive both worms simultaneously, the rotational force is distributed evenly across the wheel’s circumference, eliminating single-point failure risks. The opposing helix angles of the worms create a self-locking effect that prevents back-driving, ensuring loads stay securely positioned even during power outages. Precision ground gear teeth and preloaded bearings eliminate backlash, enabling the sub-degree positioning accuracy required in astronomical observatory domes or missile tracking systems.
Key Features and Advantages of Double Worm Slew Drives
Double Worm Slew Drives distinguish themselves through redundant reliability and massive torque density. The twin-worm design provides 100% load-sharing capability, allowing continuous operation if one motor fails—crucial for offshore oil rig equipment where maintenance delays cost millions daily. A standout feature is their dynamic load adaptability, automatically redistributing torque between worms when handling shifting loads, such as rotating unbalanced excavator buckets or wind turbine nacelles in changing wind conditions.
Unlike planetary gear systems requiring frequent lubrication intervals, these drives often incorporate sealed-for-life lubrication with high-viscosity synthetic grease that withstands temperatures from -40°C to 150°C. The modular construction allows field replacement of individual worms without disassembling the entire slewing ring—a game-changer for mining operations where equipment downtime directly impacts production targets.
Space efficiency is another hallmark. Despite their power, Double Worm Slew Drives maintain compact footprints through stacked gear arrangements. Mobile harbor cranes leverage this to maximize deck space while handling 80-ton containers, while concentrated solar power plants use the compact design to pack more trackers per acre.
Applications Across Industries
Double Worm Slew Drives prove indispensable in sectors demanding unwavering reliability:
Renewable Energy
In solar tracker systems spanning thousands of acres, these drives maintain 0.3-degree sun-tracking accuracy despite seasonal ground shifts and high wind loads. Their corrosion-resistant variants withstand desert sandstorms and coastal salt spray for decades.
Marine and Offshore
Dynamic positioning systems on drill ships use double worm drives to rotate thrusters with millimeter precision, maintaining station in 10-meter swells during Arctic oil exploration.
Defense Systems
Phased array radar installations rely on these drives for rapid 360-degree rotation while supporting 20-ton antenna weights, ensuring uninterrupted surveillance in combat conditions.
Heavy Manufacturing
Giant forging presses employ double worm systems to rotate 500-ton die sets during hot metal forming, with water-cooled housings resisting 1200°C radiant heat.
Performance Enhancements Achieved
Implementing Double Worm Slew Drives transforms operational capabilities:
Military-Grade Redundancy
The dual-worm configuration ensures continuous operation during motor failures. Offshore crane operators report 99.98% uptime even in typhoon-prone regions.
Precision Under Pressure
Advanced encoder feedback enables 0.01-degree positioning accuracy in telescope mounts tracking deep-space objects across 12-hour exposures.
Torque Multiplication
Through optimized gear ratios, these drives generate 50,000 Nm output torque from compact 10 kW motors, enabling tunnel boring machines to rotate 15-meter cutter heads through granite.
Extended Service Life
Case-hardened worms and induction-hardened wheels achieve 100,000-hour lifespans in cement plant kiln drives, outlasting traditional gearboxes by 300%.
Common Mistakes to Avoid
Maximizing Double Worm Slew Drive performance requires vigilant practices:
Ignoring Synchronization Calibration
Even minor timing differences between worm motors create destructive gear meshing. Use laser-aligned encoders and real-time adjustment software during commissioning.
Using Non-Spec Lubricants
Substituting standard grease in high-load applications accelerates wear. Always use extreme-pressure lubricants with 800+ viscosity index for worm gears.
Overlooking Thermal Management
In steel mill applications, failing to install circulating oil cooling systems leads to thermal expansion-induced gear binding.
Neglecting Contingency Programming
Not programming control systems for single-worm emergency operation defeats the redundancy purpose. Always test failover protocols quarterly.
Double Worm Slew Drives supplier
LYRA Drive is a professional slewing bearings ,slew drive and gears manufacturer provides customized slew bearing, drive and gears.For application-specific engineering solutions, contact LYRA to discuss technical specifications and implementation strategies.