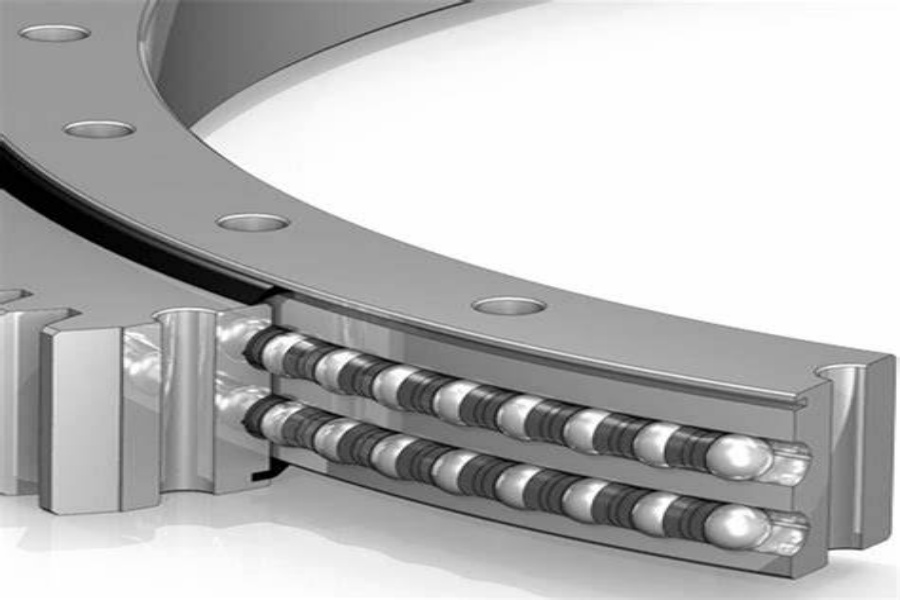
Double Row Ball Slewing Ring Bearings The Backbone of Heavy-Duty Rotation
In the realm of industrial machinery where massive loads meet precise movement requirements, Double Row Ball Slewing Ring Bearings have established themselves as critical components enabling reliable rotational performance. These robust bearings facilitate operations across industries from wind energy generation to port logistics, offering enhanced load capacity and durability compared to single-row designs. This article explores how Double Row Ball Slewing Ring Bearings deliver superior performance in demanding applications by combining structural strength with engineering precision.
What is a Double Row Ball Slewing Ring Bearings
Double Row Ball Slewing Ring Bearings are circular mechanical assemblies featuring two concentric rows of ball bearings positioned between an inner and outer ring. This dual-row configuration significantly increases load-bearing capacity compared to single-row variants, enabling the simultaneous management of axial, radial, and moment loads in heavy equipment. The separated ball tracks allow optimized stress distribution, making these bearings ideal for applications such as offshore cranes, tunnel boring machines, and radar pedestals where extreme forces and continuous operation are standard. Their design accommodates higher tilting moments while maintaining smooth rotation, providing engineers with versatile solutions for complex load scenarios.
How Double Row Ball Slewing Ring Bearings Function
Consider a container crane lifting forty-ton shipping containers in bustling seaports or a wind turbine nacelle adjusting to shifting wind patterns. The Double Row Ball Slewing Ring Bearing enables these operations through its carefully engineered structure. The bearing comprises two parallel raceways containing precision-ground ball bearings, separated by a cage system that maintains equal spacing. When rotational force gets applied through gear teeth typically integrated into the outer ring, the dual ball rows share the load proportionally, preventing localized stress concentrations. This balanced load distribution allows the bearing to handle sudden shock loads common in mining excavators while maintaining alignment accuracy within 0.1 degrees. Preload adjustments during assembly eliminate internal clearance, ensuring vibration-free operation even at maximum capacity.
Key Features and Advantages of Double Row Ball Slewing Ring Bearings
Double Row Ball Slewing Ring Bearings distinguish themselves through enhanced load capacity and operational versatility. The twin ball rows effectively double the contact area compared to single-row designs, enabling axial load capacities exceeding 10,000 kN in tunnel boring machine applications. A defining characteristic is their adaptive load distribution, automatically compensating for uneven weight distribution in applications like mobile harbor cranes lifting off-center containers.
The separated raceway design allows independent lubrication channels, enabling customized grease formulations for each ball row. Offshore installations utilize this feature by filling the upper row with water-resistant grease and the lower row with high-temperature variants to address different environmental challenges. Unlike crossed roller bearings requiring precise alignment, the ball bearing design accommodates minor mounting surface imperfections, simplifying installation in field conditions.
Modular sealing systems provide multi-layered protection against contaminants while allowing easy seal replacement during maintenance. In cement plant applications, specialized labyrinth seals prevent fine powder ingress while withstanding 150°C operating temperatures. The availability of integrated gear teeth options transforms these bearings into complete drive systems, eliminating separate gearbox requirements in solar tracker installations.
Applications Across Industries
Double Row Ball Slewing Ring Bearings serve pivotal roles in sectors requiring heavy load rotation:
Wind Energy
Turbine yaw systems employ these bearings to position nacelles weighing over 500 tons, with corrosion-resistant variants enduring coastal salt spray for 20-year service life spans.
Construction Machinery
Tower cranes utilize double row bearings to achieve 360-degree rotation while supporting boom weights exceeding 100 tons, their hardened raceways resisting deformation under variable wind loads.
Material Handling
Bucket wheel excavators in lignite mines rotate 200-ton cutting assemblies using these bearings, with sealed designs preventing abrasive coal dust ingress during continuous operation.
Defense Systems
Missile launch platforms incorporate double row bearings for smooth azimuth rotation, achieving targeting accuracies within 0.05 degrees under full combat load.
Performance Enhancements Achieved
Implementing Double Row Ball Slewing Ring Bearings delivers measurable operational improvements:
Load Capacity Doubling
The dual-row configuration supports 80% higher moment loads compared to single-row equivalents, enabling compact bearing sizes in shipboard crane applications.
Service Life Extension
Optimized stress distribution extends bearing lifespan by 150% in steel mill ladle turrets, reducing replacement frequency from annual to biennial cycles.
Energy Efficiency Gains
Reduced friction from precision-ground raceways decreases rotational torque by 25% in radar rotation systems, lowering power consumption in 24/7 surveillance operations.
Maintenance Cost Reduction
Integrated wear sensors and zerk fittings enable targeted lubrication, cutting maintenance time by 40% in offshore drilling rig applications.
Common Mistakes to Avoid
Optimizing bearing performance requires addressing these frequent oversights:
Uneven Preloading
Applying inconsistent preload across raceways accelerates wear patterns. Use hydraulic tensioning tools to ensure uniform pressure distribution during installation.
Lubrication Mismatch
Using single grease type for both rows negates temperature adaptation benefits. Consult manufacturers for dual-grease specifications in applications with thermal gradients.
Corrosion Neglect
Failing to specify stainless steel variants in coastal crane applications leads to raceway pitting within 18 months. Implement annual salt deposition tests in marine environments.
Overlooking Dynamic Loads
Designing for static loads alone causes premature failure in rock crusher applications. Always factor in 150% dynamic load multipliers for shock-prone equipment.
Double Row Ball Slewing Ring Bearings supplier
LYRA Drive is a professional slewing bearings ,slew drive and gears manufacturer provides customized slew bearing, drive and gears.For application-specific engineering solutions, contact LYRA to discuss technical specifications and implementation strategies