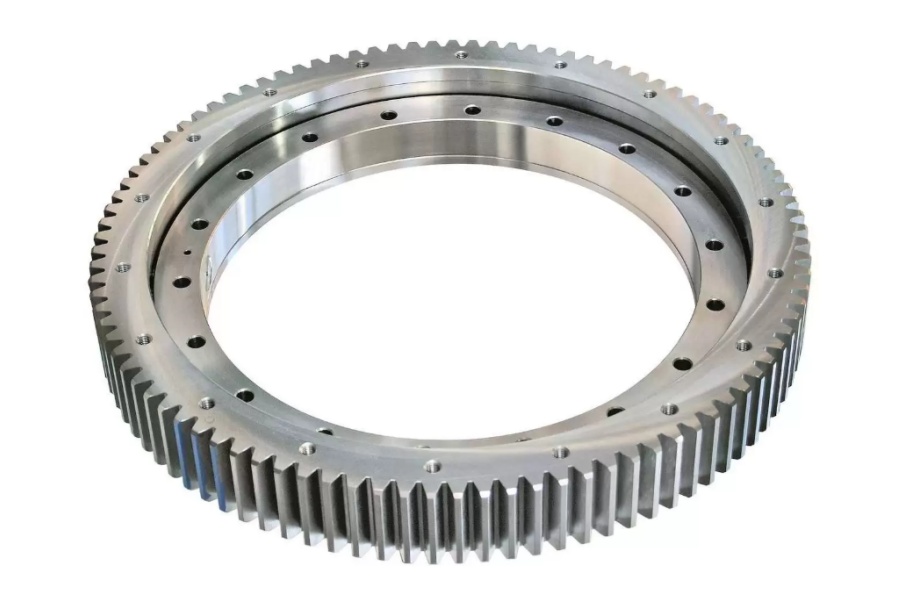
Precision Transmission System Selection: Slew Drive vs Worm Gear
What is Slew Drive?
A Slew Drive is a highly integrated electromechanical drive unit, consisting of a worm gear/planetary gear system, a large slewing bearing, a sealed housing, and a drive motor. It combines three functions—speed reduction with torque increase, power transmission, and load support—into a single compact module, directly outputting 360° rotational motion. Typical applications include solar trackers and crane turntables, where high torque and heavy load capacity are required.
Core Features of Slew Drive
Full-function integration: A single module provides speed reduction, load bearing, and rotation control, eliminating the need for external bearings.
Ultra-high load capacity: The integrated slewing bearing can withstand >5000kN·m overturning moment.
Precise positioning: The worm gear structure achieves ≤0.1° repeat positioning accuracy (self-locking type).
Harsh environment resistance: IP66 protection and lifelong lubrication design adapt to outdoor working conditions.
Quick installation: Pre-assembled modules reduce equipment integration complexity and man-hours.
What is Worm Gear?
A Worm Gear is a basic speed reduction transmission pair, composed of a worm (driver) and a worm wheel (driven part). It uses 90° staggered-axis transmission to achieve high reduction ratios (typically 10:1~100:1) and transmits power through sliding friction. Its core value lies in simple structure, low cost, and reliable self-locking, making it common in light to medium-load scenarios such as conveyors and small turntables.
Core Features of Worm Gear
High reduction ratio: Single-stage transmission can achieve 100:1 reduction, saving space.
Reverse self-locking: Natural self-locking when the lead angle <5°, no need for additional brakes.
Low cost: The manufacturing cost of cast worm wheels + steel worms is 40% lower than that of gear systems.
Compact layout: Right-angle input and output simplify mechanical structure design.
Noise control: Sliding friction transmission results in noise ≤65dB(A).
Slew Drive vs Worm Gear: Core Difference Comparison
Parameter | Slew Drive | Worm Gear |
System positioning | Integrated drive unit (including bearings, gears, seals) | Basic speed reduction component |
Load capacity | Ultra-high (overturning moment >2000kN·m) | Medium-low (torque usually <500Nm) |
Precision grade | ≤±0.1° (precision ground teeth) | ≤±0.5° (greatly affected by backlash) |
Environmental adaptability | IP66 protection, -40℃~120℃ wide temperature range | Requires additional protective covers, suitable for -20℃~80℃ |
Installation complexity | Ready-to-use, reducing 80% of assembly processes | Requires independent design of bearing seats and sealing systems |
Service life | >50,000 hours (lifelong lubrication) | 20,000 hours (regular grease replacement required) |
Cost structure | High unit price ($1,000~$20,000) | Low unit price ($50~$500) |
Guide to Typical Application Scenarios
Choose Slew Drive when:
Directly bearing overturning moment is required (e.g., solar tracker bases).
High-precision positioning is needed (e.g., radar antennas/medical equipment turntables).
Space is limited and high integration is required (e.g., excavator slewing platforms).
Long-term operation in harsh outdoor environments is necessary (e.g., wind turbine pitch systems).
Choose Worm Gear when:
Light-load and low-speed transmission is needed (e.g., small conveyors/rotary display stands).
Budget sensitivity is a priority (e.g., material handling carts).
Simple self-locking function is required (e.g., door and window opening/closing mechanisms).
Maintenance convenience is prioritized (e.g., food processing equipment).
Performance Upgrade Solution: Worm Gear in Slew Drive
High-end Slew Drives adopt precision worm gears as the core transmission pair, breaking through traditional limitations with three technologies:
Material upgrade: Worms are made of 20CrMnTi with carburizing and quenching (HRC60); worm wheels use centrifugally cast ZCuSn10P1.
Precision control: Worm grinding accuracy reaches grade 5, with tooth surface roughness Ra0.4μm.
Lubrication optimization: Synthetic oil + polymer additives reduce the friction coefficient to 0.03.
Cost-Effectiveness Decision Model
Item | Slew Drive Advantage Scenarios | Worm Gear Advantage Scenarios |
Total cost of ownership | Heavy-load equipment (reducing maintenance downtime losses) | Light-load equipment (40% initial investment savings) |
System complexity | Space-constrained/high integration requirements | Simple transmission chain design |
Life cycle value | Critical equipment with >10-year service life | Consumable equipment with <5-year service life |
Professional Solution Providers
LYRA Drive offers both types of product technologies:
High-performance Slew Drive:
Torque range: 500Nm~500kNm
Optional precision worm gear or planetary gear structure
IP68 protection/-40℃ cold-resistant type
Custom Worm Gear:
Module: 1~20mm; reduction ratio: 10:1~100:1
Nickel-phosphorus plated worms extend wear life by 3 times