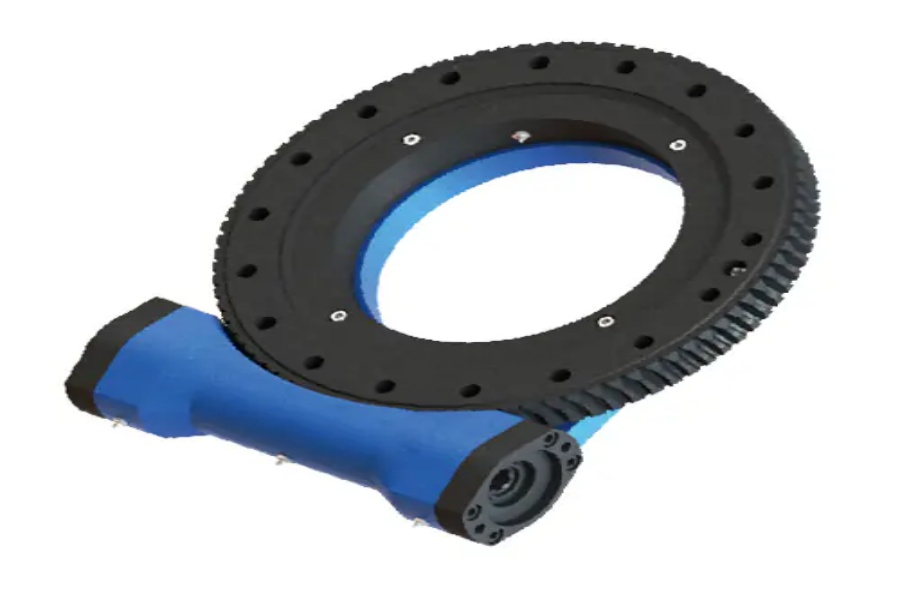
Exploring the Exceptional Role of WE Slew Drive in Welding Positioners
In modern welding operations, welding positioners play a pivotal role by precisely maneuvering workpieces to position seams for optimal welding access, ensuring consistent quality and efficiency. At the heart of these advanced systems lies the WE Slew Drive, a compact yet powerful rotational transmission component that has revolutionized how positioners handle complex movements. This article dives into how the WE Slew Drive elevates welding positioner performance through its innovative design, reliability, and adaptability.
What is a WE Slew Drive?
A WE Slew Drive is a highly engineered rotational mechanism designed to provide precise and controlled movement for heavy-duty machinery, combining a slewing ring bearing with an integrated gear system—typically a worm or spur gear configuration. This component is essential for applications requiring smooth 360-degree rotation under substantial loads, such as cranes, solar trackers, or industrial robotics. The "WE" designation often refers to a specific model series or brand variant, emphasizing features like enhanced load distribution, modular design, or customized sealing solutions. Unlike standard slew drives, WE models may incorporate proprietary technologies to optimize torque efficiency, reduce backlash, or withstand extreme environmental conditions, making them a versatile choice for industries demanding reliability and precision in motion control.
How WE Slew Drive Works in Welding Positioners
Imagine a welding positioner as a robotic arm that rotates, tilts, or flips heavy metal parts so welders can access seams from ideal angles. The WE Slew Drive acts as the “muscle and brain” behind this motion, combining rotation, torque control, and precision into a single integrated unit. Built around a slewing ring bearing, it integrates a motor, gear reduction system, and mounting interfaces within a compact housing. One ring attaches to the positioner’s base, while the other connects to the rotating platform or tilt mechanism. When the motor activates, it drives the gears to rotate the slewing ring smoothly, enabling precise angular adjustments—whether slowly aligning a delicate aerospace component or rapidly flipping a massive steel beam.
Key Features and Advantages of WE Slew Drive
The WE Slew Drive stands out due to its modular design, which eliminates the need for users to source and assemble individual components like motors, gears, and bearings separately. This plug-and-play approach slashes assembly time and reduces the risk of misalignment errors. Its self-locking capability, a hallmark of its worm gear-driven design, ensures that loads stay securely in place once positioned—critical for safety when handling heavy or unbalanced workpieces. Unlike traditional chain-driven systems, this self-locking feature prevents unintended movement, even during power outages or sudden stops.
Another standout trait is its space-saving profile. By integrating the drive system within the slewing ring’s footprint, the WE Slew Drive minimizes the positioner’s overall size without sacrificing power. This compactness is a game-changer for workshops with limited floor space. Additionally, its high torque-to-size ratio allows it to handle both lightweight precision parts and bulky industrial components, adapting seamlessly to diverse welding tasks. Maintenance is simplified too, with easily accessible grease ports and corrosion-resistant coatings that extend service life in harsh environments like shipyards or outdoor construction sites.
Applications of WE Slew Drive in Welding Positioners
The WE Slew Drive shines in two primary roles within welding positioners: rotational control and tilting/flipping mechanisms.
In rotational systems, the drive provides smooth, continuous rotation of the positioner’s worktable. For instance, when welding cylindrical tanks, the WE Slew Drive enables 360-degree rotation at variable speeds, allowing welders to maintain a consistent arc without repositioning themselves. This is especially valuable in automated welding cells, where robots rely on flawless, repeatable motion to execute perfect seams. The drive’s precision ensures that even at ultra-low speeds—essential for welding thin materials or intricate patterns—the movement remains jerk-free, eliminating defects like porosity or uneven bead formation.
For tilting and flipping applications, the WE Slew Drive’s robust construction and precise control come into play. Take an L-shaped positioner designed for large structural beams: the drive’s worm gear system allows one arm to tilt the beam 180 degrees while a secondary rotary axis adjusts its horizontal angle. This dual-axis flexibility lets welders access overhead seams or hard-to-reach joints without manual repositioning. In automotive manufacturing, where components like exhaust systems require multi-angle welding, the drive’s ability to stop and hold position at any angle ensures flawless access, reducing rework and speeding up production lines.
How WE Slew Drive Enhances Welding Positioner Performance
The integration of WE Slew Drive directly translates to measurable improvements in welding outcomes:
Precision and Repeatability:
The drive’s gear reduction system and high-resolution encoders enable micron-level positioning accuracy. In industries like aerospace, where turbine blades demand exact weld placements, this precision minimizes heat distortion and ensures compliance with strict tolerances. Repeatability—achieving the same position cycle after cycle—is crucial for mass production, and the WE Slew Drive delivers consistency even after thousands of rotations.
Load Capacity and Durability:
Constructed from hardened steel and featuring reinforced gear teeth, the drive handles asymmetrical loads without deflection. For example, in wind tower manufacturing, positioners must rotate massive, unevenly weighted segments. The WE Slew Drive’s rigidity prevents flexing, maintaining alignment under stress and reducing wear on the slewing ring.
Speed and Efficiency:
By combining rapid motion with precise stops, the drive slashes non-productive “idle time” during welding setups. A case in point is agricultural equipment repair, where positioners equipped with WE Slew Drives can quickly flip plow blades between weld passes, cutting total job time by up to 30%. Variable speed settings also let operators fine-tune rotation for different materials—slower for aluminum to prevent burn-through, faster for thick steel plates.
Safety and Reliability:
The self-locking worm gear design eliminates the need for external brakes, reducing mechanical complexity and failure risks. In nuclear facility maintenance, where safety protocols are extreme, this feature ensures that radioactive components remain stable during welding, protecting both workers and equipment.
Common Pitfalls to Avoid When Using WE Slew Drives
While the WE Slew Drive is engineered for reliability, improper use can undermine its performance:
Overloading Beyond Capacity: Exceeding the drive’s rated load—say, by mounting an oversized workpiece—can deform gears or crack the slewing ring. Always verify weight limits before operation.
Neglecting Lubrication: Despite its sealed design, periodic greasing is essential. Skipping maintenance in dusty environments can lead to abrasive particle buildup, accelerating wear.
Misalignment During Installation: Even minor angular deviations during mounting can strain the drive. Use laser alignment tools to ensure the motor and slewing ring are perfectly coaxial.
Ignoring Environmental Factors: While the drive is weather-resistant, prolonged exposure to saltwater or chemical fumes without protective covers can degrade seals.
WE Slew Drive supplier
The WE Slew Drive isn’t just a component—it’s a transformative force in welding technology. By merging power, precision, and adaptability into a compact package, it addresses the core challenges faced by modern welding operations: faster throughput, tighter tolerances, and safer workflows. As industries push toward automation and smarter manufacturing, drives like the WE Slew Drive will remain indispensable, enabling welders to tackle tomorrow’s challenges with today’s proven reliability. Whether crafting delicate medical devices or monumental steel structures, this innovation ensures that every weld is not just a join, but a testament to engineering excellence.
LYRA Drive is a professional slewing bearings ,slew drive and gears manufacturer provides customized slew bearing, drive and gears.For application-specific engineering solutions, contact LYRA to discuss technical specifications and implementation strategies.